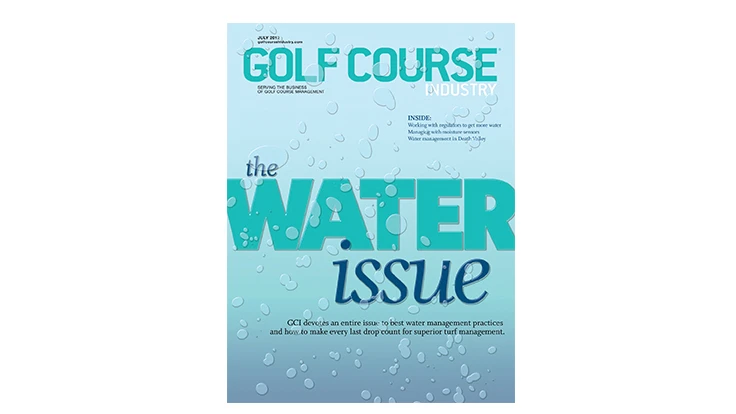
It was six years ago that the agronomy team at the Desert Mountain Club in Scottsdale, Ariz., realized that the pricing on our commodities – reclaimed water, fertilizer, seed – was on the rise. That’s always cause for concern for any club but especially so at Desert Mountain with six Jack Nicklaus Signature courses on 550 acres of turf. Comprised of six turf types, the courses accommodate 150,000 rounds of golf annually.
Typically we use 400,000 pounds of seed and 600,000 pounds of fertilizer in a year. In addition, we’re located in the Sonoran desert where water is one of our most precious, and expensive, resources. Desert Mountain partnered with the city of Scottsdale and the state to utilize treated effluent, or reclaimed water, to reduce our water footprint. Using 1 billion gallons annually makes us the largest user of reclaimed water in the metro Phoenix-Scottsdale area. We move that water through 11 on-site pump stations and eight reclaimed water lakes.
Dealing with the sheer volume of running an operation of this size and the cost it entails, I recognized the need for a comprehensive records system to keep track of just how much water we were using and just how much we really needed. Reducing energy and operating costs while continuing to maintain the greens in championship condition to provide a golf experience the members have come to expect on these award-winning courses also became a goal. In addition, reaching these goals would reduce our footprint on the land as no decision is made here without considering the indigenous plants and the wildlife that make this property home.
One of the areas I thought we could reduce our use of reclaimed water as well as fertilizer was in our leaching schedule. We had been flushing the salts and alkali out of the soil 20 times per year, requiring a significant output of water and power. It was at that time that I enlisted the help of Walt Norley at UgMo, a leader in advanced soil moisture monitoring, to create a wireless ground sensor that would tell me the TDS (total dissolved salts) in the soil which I could compare to the industry standard. Sensors installed, we monitored and waited for the TDS level to rise. It didn’t, and we were able to eliminate the guess work and reduce the flushing to six times per year for a savings of 3-4 million gallons of water and a 10-15 percent reduction in our greens fertilization.
The sensors also captured moisture level, soil temperature and other variables. But what good was all this disparate data if we couldn’t integrate it into our existing software that would help us monitor our peak water and energy usage, our storage lake levels and, most importantly, pinpoint how much water (and the energy to pump it to the courses) and fertilizer were actually needed in order to become better stewards of the land and save money?
Tweaking the technology. In my two decades in the agronomy industry, the best words of wisdom I can give are these: It’s okay to have problems but it’s even better to ask for help. The agronomy department utilizes four separate softwares: Rainbird, Microcom, Arizona Public Service and UgMo. But together they’re incompatible and we needed them to communicate in real time so that if our weather station tells us the courses received rain the night before, we could adjust the irrigation to water less that day, among other situations that require fine tuning on a daily basis. The agronomy budget could not withstand the purchase of all new software so once again I turned to experts in the business.
![]() |
Through UgMo’s partnership with IBM, I learned that IBM’s Intelligent Operations Center (IOC) and Water Information Hub (WIH) systems could unite the four softwares into one platform to help us gather analytics while continuing to utilize our existing software. This became IBM’s first application of analytics software on a golf course.
A key partner in this effort is Element Blue, an IBM Premier business partner responsible for the installation and management of the IOC and WIH systems. The IOC is an expandable platform designed to provide operational insight across one or multiple domains. The WIH allows users to have a system-wide view of operational and infrastructure performance. Together they create a common platform for information flow across the entire property. The software solution is hosted on the IBM Smart Cloud and managed by Element Blue.
With a customized dashboard and mobile notification capability, we can capture and visualize measurement data from monitors and the wireless ground sensors with which to base our decisions. Data, collected from onsite telemetry systems, including water flow, electricity usage and lake levels is captured, analyzed and displayed by the system in a single unified view of usage across the property. In addition soil moisture, salinity and temperature data is gathered from sensors across the course and combined with the telemetry data to provide an integrated view of course conditions and direct feedback on water and power usage.
In other words, instead of taking 30 days to gather and verify data, we can gather information up to six times per hour, 24 hours per day, allowing us to make decisions within 15 minutes. We can maximize response times to changing course conditions, and to minimize water usage, power consumption, personnel time and other direct costs. Course supervisors can adjust the system to respond to preset thresholds for every measurement collected and can be alerted in real time when thresholds are exceeded. We no longer need to rely on “sneaker net,” meaning that we’re running back and forth to gather updates on course and soil conditions.
The payback. The software installation on the Cochise course will be completed by the end of July and we are projecting a 5-10 percent energy savings, a 20 percent reallocation of reclaimed water to other areas of the property and a 50 percent time savings for the irrigation manager. Eventually, we plan to install the technology on the remaining five courses in the next 1-3 years which will require only the cost to integrate the software into the main platform. I also anticipate that the purchase and integration cost of the software will pay for itself in three years.
With today’s continually rising costs, coupled with increased player expectation of the quality of course conditions and overall golf experience, it is important for superintendents to know the business of running their course on a daily basis and to recognize trends in order to maintain quality and to control costs. As innovative as the Desert Mountain Club is, we did not invent anything new to help us achieve these goals. We simply identified the issues and engaged our partners in helping us find the answers in an inexpensive way. And in the process, we’ll become better stewards of the land and educators in protecting our natural resources.
Shawn Emerson is director of agronomy at Desert Mountain Club.
Get curated news on YOUR industry.
Enter your email to receive our newsletters.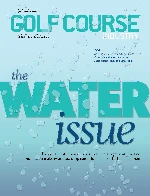
Explore the July 2012 Issue
Check out more from this issue and find your next story to read.
Latest from Golf Course Industry
- Advanced Turf Solutions’ Scott Lund expands role
- South Carolina’s Tidewater Golf Club completes renovation project
- SePRO to host webinar on plant growth regulators
- Turfco introduces riding applicator
- From the publisher’s pen: The golf guilt trip
- Bob Farren lands Carolinas GCSA highest honor
- Architect Brian Curley breaks ground on new First Tee venue
- Turfco unveils new fairway topdresser and material handler