
The weather was good for outdoor projects about a month longer than usual as we ended 2016, so I was needed in the shop even though the golf course was closed to sharpen tools and repair the machines being used when they broke down. The big projects were filling the sand traps to the top with sand and a pond landscaping art project. The ponds are getting a nautical look, stubs of the two power poles that were cut down (100 feet each), are being lined up on the water’s edge to look as if they are driven in waterfront pilings. It looks pretty cool. Some old mooring line draped here and there with a seagull or two would finish off the theme nicely. Also, some fence that fell down needed to be replaced before the ground froze. The fence was scheduled for next season but with this extra month of warm weather it got done this year.
Replacing fence posts required dusting off the three-point, tractor-mounted posthole digger and getting it ready for the landscaping crew to use. Because it had been stored assembled, the PTO shaft was seized. Once seized, PTO shafts are scrap. A quick trip to the dealership and I had a new shiny one. When I got it running, the posthole digger made drilling holes in heavy clay easy. The decorative fences are up, everyone is happy. When done drilling, the PTO shaft found a home in cold storage on the wall, disassembled, coated with anti-seize, waiting for the next time it will be needed.
Putting the shop to bed for the winter meant taking all the reels off and lining them for transport. They are going back to the dealers for regrinding and bearing replacement. The bearings in the rollers and reels seem to last about one-and-a-half seasons without any attention so replacing them each year assures they will operate flawlessly the entire season. This past season I had to do some emergency bearing replacements and when I checked with the dealer it was because they had not actually replaced ALL the bearings. While they had charged us for replacing all of them, they admitted to only replacing “the ones that needed it.” They refunded the bearing charges on the reels I had to rebuild midseason.
I cleaned off the workbenches and painted their tops with the same paint that is used to paint the floor. Picked everything up off the floor to clear the way for the people who use the shop in the winter and paint the floor when the reels are gone. I switched the lift from mower lifting feet to on-road vehicle lifting pads. In the winter people use the shop to repair their cars and trucks. It is a clean, dry, warm place to work on such things and the shop tool set is extensive.
My thoughts keep coming back to the idea of designing and building a turf utility vehicle with a variable frequency AC electric motor in each wheel (4WD), and a large engine-generator to power it. It should also be modular construction, easy to maintain, a design each golf course could build from plans with locally available materials.
I have several generators. I’m thinking of using one of them for the prototype. Once I work the bugs out of the design, I could get a larger one or better yet a marine grade generator that is meant to run while being bounced around. The Kubota engine in most of the mowers is actually a marine generator engine – I found that out when I needed to buy a B-end plate and the dealer I had to get it from was a marina in Florida. For just a fleeting moment, when buying that part, I felt like I was in the same league as his other millionaire customers.
Get curated news on YOUR industry.
Enter your email to receive our newsletters.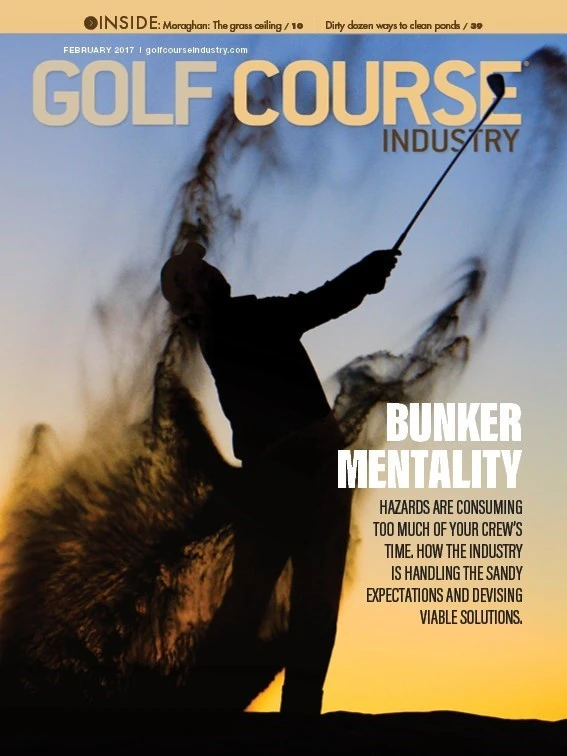
Explore the February 2017 Issue
Check out more from this issue and find your next story to read.
Latest from Golf Course Industry
- Atlanta Athletic Club approves funding for master plan
- PBI-Gordon introduces new field development team
- The Cabot Collection announces move into course management
- Carolinas GCSA raises nearly $300,000 for research
- Advanced Turf Solutions’ Scott Lund expands role
- South Carolina’s Tidewater Golf Club completes renovation project
- SePRO to host webinar on plant growth regulators
- Turfco introduces riding applicator