Globetrotting consulting agronomist Terry Buchen visits many golf courses annually with his digital camera in-hand. He will share helpful ideas relating to maintenance equipment from the golf course superintendents he visits – as well as a few ideas of his own – with timely photos and captions that explore the changing world of golf course management.
A fan for cleaner air
Ralph Arnt, equipment manager at Hazeltine National Golf Club in Chaska, Minn., since 1988, is highly skilled at fabricating anything from scratch. Arnt build an exhaust fan for the express dual-reel grinding machine to remove iron filings when reels are ground and improve air quality for the operator.
The fan’s framework, which was welded together, consists of 0.040-inch-thick aluminum sheet metal ($35) that measures 22 inches by 52 inches, aircraft-type rivets ($25) and 17 feet of 1-inch-by-1/8-inch square steel tubing ($1.13 per foot).
The exhaust fan, which fits in the back of the grinding machine, sticks out from the machine 16 inches at its deepest point. The 12-inch-by-25-inch-high outlet opening allows the fan and motor to fit inside comfortably. Two 20-inch-by-25-inch, pleated furnace filters ($6.50 each) catch the iron filings so they don’t contaminate the air in the mechanic’s shop area. They’re replaced as needed. The used 1,450-cubic-feet-per-minute exhaust fan and motor ($30, $306 new) came from a heater furnace.
A box for tourney prep
Ranald McNeill, director of golf course operations at the Doha (Qatar) Golf Club, hosts the annual Qatar Masters Tournament on the European PGA Tour in January. McNeill’s staff installs all of the tournament equipment (gallery ropes, stakes, etc.) during advance week then tears it down after the event.
To help with the installation and tear-down of the tournament equipment, the maintenance staff built oversized wooden boxes and installed them on the back of golf cart-type maintenance vehicles after the golf bag racks were removed.
The two metal brackets behind the seats are used to mount the fiberglass top used during the rest of the year. It was removed for the tournament so the maintenance carts could drive underneath the tournament ropes with ease.
Each box is made of 3/4-inch-thick, marine-grade plywood measuring 47 1/4- inches by 35 1/2 inches by 11 3/4 inches. The sides are held together with industrial glue and L-shaped screw-type metal brackets. The plywood is coated with water-repellent stain.
The underframe was built using 2-inch-by-4-inch and 4-inch-by-4-inch construction-grade wood held together and mounted to where the rear bumper formerly was with nuts and bolts and heavy-duty nails.
It took about four hours to build each box, and materials for each cost $70. GCI
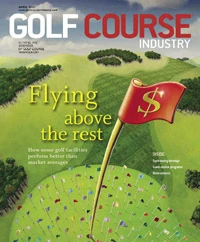
Explore the April 2007 Issue
Check out more from this issue and find your next story to read.
Latest from Golf Course Industry
- The Cabot Collection announces move into course management
- Carolinas GCSA raises nearly $300,000 for research
- Advanced Turf Solutions’ Scott Lund expands role
- South Carolina’s Tidewater Golf Club completes renovation project
- SePRO to host webinar on plant growth regulators
- Turfco introduces riding applicator
- From the publisher’s pen: The golf guilt trip
- Bob Farren lands Carolinas GCSA highest honor