
Waste not, want not
What do aluminum cans, worm farms and propane have to do with your facility’s bottom line? More than you might think.
One of the most common themes within the golf course management profession is how to get more work done with fewer resources. This has led many superintendents to master the art of maximizing what they have and leveraging the full worth of any asset no matter how small or overlooked.
Benjamin Franklin aptly reminded us that a penny saved is a penny earned, but what does that mean for the modern golf course superintendent? The savvy superintendent in today’s economy has created programs and projects that are turning some common items from useless to useful and impacting the financial strength of the operation not to mention earning a few creativity points along the way. Here are a few tried and true ways to waste not, want not.

Green Wastes and Organic Debris Management
One way to turn something that appears useless into something useful addresses organic wastes. This covers a lot of territory from leaves and tree debris to the golf-centric aeration cores gathered from greens or tees. While it is common to use aeration cores as fill material throughout the course, many superintendents are now turning their leaves and tree debris into valuable mulch to be used on site as well. The process is a three-part endeavor. First, choose a site to collect the debris. The collection site should afford the staff easy access but not be too visible as to generate complaints from golfers/guests. Secondly, when your collection area is full, you will need to grind these materials into consistent mulch. You can purchase the equipment yourself or contract a local vendor to handle the grinding as needed. This decision is largely a personal preference but running a quick ROI calculation is always a good idea. Lastly, once the debris has been properly ground, you can install the mulch in flower beds, erosion areas or compost sites throughout the property. This will allow your green wastes to continue their life-cycle on property, eliminate landfill fees and even provide nesting materials and wildlife habitat while the debris pile is waiting for grinding.

Recycling – Turning Trash into Cash
Another way to turn a negative into a positive is to establish basic recycling programs that can turn trash into cash. Even smaller operations can benefit from this type of program. They are easy to start and sometimes as simple as creating a special collection container for cans or bottles.
There is a great story from the GCSAA Environmental Leaders in Golf contest that really shows the potential of these programs. In 2009, the overall winner of the Environmental Leaders in Golf contest was Terry Straton, golf course superintendent at Little River Inn Golf and Tennis Club in California. Terry organized an amazing recycling effort that funded the team’s (Terry, Scoot Cail, Ron Levy and Darrel Low) trip to the Golf Industry Show in San Diego. They raised over $2,000, with $1,300 coming from recycling cans and bottles. There are all sorts of things throughout the golf course maintenance operation that can be recycled. Consider developing recycling programs for things such as batteries (small and large), printer cartridges, light bulbs, ballasts, paper, cardboard, waste oil and other petroleum products, copper and metal piping.

Chemical and Fertilizer Application Reduction
There are those superintendents who look at a problem and have the unique ability to see a bigger picture than most people and, therefore, connect some pretty amazing things.
Mark Hoban, the superintendent at the Rivermont Golf and Country Club in Johns Creek, Ga., is one of those superintendents. Mark saw an opportunity to reduce his chemical and fertilizer costs by literally making his soils healthier. In March 2013, Mark began a compost tea program to enhance soil biology through the introduction of large amounts of diverse microorganisms to the soils on his greens, tees and fairways. Mark researched the process and consulted with a number of organic farmers who had been successful and he felt that his version of the process would also be successful on the golf course.

Mark convinced the owner to invest in a compost system and cited the potential savings in fertilizer and chemicals along with healthier turf as a byproduct of the investment. Mark’s fairways were 40 years old and he had been applying 2.5 lbs of inorganic and synthetic nitrogen on them each of the last seven years. The results were striking. In the first year, fertility on fairways was reduced to .62 lbs of N. In year two, the total N applied was down to .48 lbs. In the third year, the total N was even lower at .35 lbs. These results combined with members commenting that the fairways were the best they had been in years was certainly a win-win process.
Even Mark admitted the turf quality was noticeably high. However, the fertility was just one part of the puzzle. “We had averaged 15 fungicide applications per year on greens leading up to the start of our compost tea program,” he says. “In the first year of using the compost tea program, we cut the number of fungicide applications to three.”
He made five fungicide applications in the second year and spot treated an additional five times. The third year featured excessive heat in May and June, and four apps before June 17 had to be applied.
“I knew I was pushing the envelope of how far I could go and didn’t know until I went too far and Mother Nature showed me excessive heat, traffic and humidity are lethal to bentgrass health and fungicides need to be used ahead of the stress,” he says. Mark had found the magic line to make the program sustainable.
Mark’s worm farm produces enough vermicompost for his brewer to supply his property’s needs, but he admits that it is a fine art to brewing compost tea.
“I learned you needed to measure the dissolved oxygen, dechlorinate the water, control temperature and do microscope readings to determine when it’s actually ready to apply,” he says. “I am able to utilize food waste from the club in the process, and I make thermal compost from clippings, wood chips and tree leaves to add diversity to my brew. One tank of brew has more microorganisms than all the people that have ever lived on planet earth.”

Mark hopes the combination of tea and biannual compost applications this will become the only plant health and fertility used in their landscape, club grounds and native/wildflower areas. He has a two-year program to purchase vermicompost, a high quality carbon and microbial product to blend into his topdressing sand.
“I have found out that the carbon is vital to the soil biology and its symbiotic relationship with the turfgrass and is a catalyst in getting the nutrients that are tied up in the soil to release and become available to the plant as well as adding additional microdiversity,” he says.
Mark has seen evidence in his trials to show that the vermicompost is even controlling dollar spot, which can be a concern with lower fertility programs. He is currently working with researchers at the University of Georgia on this data as well as Dr. Jenifer McBeath out of Alaska with a trichoderma atroviride fungi. Mark has been very successful moving his theories into practice on a daily basis on his course.
Alternative Fuel as a Financial and Environmental Option
The cost of fuel is always a concern to any business that runs equipment on a daily basis. This has led researchers to create a variety of alternative fuels and some have ventured into golf such as biodiesel, a fuel made from used cooking oils. The latest of these fuels to test its worth in the golf industry is propane. The Propane Education and Research Council invested in a one-year case study placing green mowers, tee mowers, fairway mowers and bunker rakes at eight golf courses located across the country.
I had the privilege to participate in the case study during my tenure at the Stone Mountain Golf Club by Marriott. We saw a 30 percent savings year over year in fuel costs. We immediately saw the environmental advantages of removing the likelihood of fuel spills (liability savings) and the ability with the propane canisters to refuel in the field saving labor and increasing productivity. The propane-powered mowers are also affordable because they do not require expensive Tier-4 upgrades. Our equipment technicians were very complimentary of the maintenance requirements being in line with other traditional mowers.
Jim Coker, director of propane applications for R&R Products, was a key player in setting up and servicing the propane case study.

“It was critical to get this equipment onto a variety of golf courses and climates so that we could see just how effective the processes could be and offer an alternative to the dependency on traditional petroleum fuels,” he says. “Propane is produced here in the United States, and delivers a stable, affordable and environmentally superior fuel option.”
Time will tell if propane-powered mowers become commonplace in the golf industry, but there are obviously opportunities to save money and expand your environmental programs.
The golf course industry demands excellence and rewards innovation especially when it comes to evaluating the bottom line. The modern golf course superintendent is finding ways to utilize everything from aluminum cans, to worm farms and even the power of propane to squeeze every ounce of profit out of their operations. The key is to always be willing to see the potential and prove the value of worthy ideas. This work ethic is the difference between good and great, proving that sometimes a penny saved may actually be more than a penny earned.

Down in the dumps
Waste is a way of life on golf courses. Let’s review some of the best programs for handling it.
By Anthony L. Williams CGCS, CGMSince golf’s beginning there has been an ongoing struggle to find an appropriate way to handle the wastes generated by the operation. The more developed the property is, the bigger and more complex the problem of waste management becomes. The superintendent must also factor into their programs the increasing regulatory pressures that impact the fate of everything from leaves and limbs to tires and waste oil. The search for creative and compliant ways to effectively manage waste byproducts is a necessity for the modern superintendent. We are going to review some of the best programs to help keep your operation from being, “Down in the Dumps”
The first step of handling your waste effectively is to identify how much and what type of wastes your property generates. You will likely be dealing with simple organic waste such as clippings, leaves, limbs, spent flowers, etc., inorganic wastes such as retired equipment/parts, tires, batteries, cans, bottles and other packaging, and lastly a very important group, chemicals products. It should be easy to identify the waste items that you are generating, but it is also important to get an accurate estimate of the amounts generated. These items can be tracked by weight or mass measurements, and if you have been literally filling the local landfill, there should be records that indicate the volume of waste generated. Once you have the numbers, you can start taking on a few processes to impact the results.
Leaves, Limbs and Tree Debris
In recent years, many landfills no longer take green waste (leaves, tree debris, etc.). These materials must be sent to special landfills or recycling areas, and the costs can be significant. What can be done to reduce these expenses? One of the best solutions is to establish a small collection area to gather all these materials for storage and periodically grind these into mulch that can then be used on the property in flower beds, trails/walkways and erosion control areas. These types of programs can cut your green waste disposal costs by as much as 50 percent. One of the decisions to be made here is whether to purchase grinding equipment or contract with a local partner to periodically grind the material. The ROI for this project will usually be in favor of contracting the service for grinding. But taking the time to gather estimates and compare the results will always pay dividends. Depending on the size of the area available, you may grind quarterly or annually. Larger operations may defer grinding for as long as three years; this can negatively impact the quality of the mulch produced limiting in some cases how it can be used. Costs of these programs can be as low as a few hundred dollars annually and occasionally bartering and trade options can fund the entire program. Here are a few additional values to this type of program.
- Allows for the organic wastes from trees and vegetation to complete their life-cycle on property
- Reduces the amount of waste sent to landfills annually and saves disposal fees
- Generates mulch for use throughout the property
- While the waste is being stored, it provides nesting materials and habitat for the native wildlife
- Accelerates the cleanup of debris following weather events
- Creates a win-win public relations opportunity for your environmental programs that can be spun in a variety of ways such as saving landfill space, providing habitat and protecting your green assets.

There are a few items to consider before starting this type of program. First, be sure numbers are correct and ROI is realistic before you present the program to property leaders for approval. Make sure the collection area has easy access (the staff will use it properly) and not too visible (members/golfers may hate the look of it). Remember that as the superintendent your commitment to tracking and communicating the progress and the details of the program will ultimately decide if it was successful.

Old Equipment, Tools and Parts
The “graveyard” for old spent equipment is not as common as it used to be with the popularity of large lease equipment fleets rolling over on shorter intervals. However, the financial pressure to get more out of every piece of equipment means you can still find examples of yesteryears equipment hidden in a discreet corner of the property. There are two easy steps to avoid or cleanup this situation. The first step is to develop relationships with local equipment or salvage dealers. These partners can turn your old equipment into cash/credit and work with you on small deals (equipment parts) or even bundled deals for a variety of multiuse “vintage” (past its prime) equipment. Negotiate a win-win deal and the graveyard will soon be gone. The second step is to harvest and organize parts from retired equipment immediately and resist the temptation to park a “donor” fairway unit behind the shop to supply parts for a similar model with fewer hours. Trust me, harvest the parts and store them properly to never have a “dump” on your property map.
Reducing, Recycling and Repairing
Many superintendents have incorporated reducing and recycling programs to limit how much material is available to create the “dump” effect. The fundamentals of all reducing programs are simple – use less, buy less and naturally accumulate less. This applies to fuel, utilities, supplies, etc. These programs range from waterless urinals to using long-lasting LED lights to using alternative fuels such as biodiesel. The premise is to save money while reducing the need for storage and/or disposal of traditional items. Superintendents are recycling lots of things and generating revenues for the effort.
Buck Workman, general manager and CGCS at the Cateechee Golf Club in Hartwell Ga., says, “We take the funds generated from our salvage and recycling programs and use them for employee meals and outings. It motivates the staff and rewards everyone when we do the right thing.”
These programs can be as simple as a recycling collection bin for aluminum cans or be as complex as using a third party to handle waste oil or used tire recycling to reduce liability and add a layer of documentation. Be sure to research any regulations in your area and establish clear benchmarks. Another way to address these ongoing opportunities is to assign a weekly cleanup inspection to your staff. This will engage the entire staff and cover the entire property with many eyes and hands. Establish a simple and clear set of jobs and procedures, and be sure to reward the work and inspect the results. Be vigilant to remove and properly recycle or repair even small things such as broken bunker rakes (good head, bad handle or vise-versa), broken or wandering hand tools, pallets (these elusive creatures stack themselves in odd places after every sod project and large EOP delivery), light fixtures, and the list goes on.
Chemical Disposal Procedures
In a perfect world, we would never need to dispose of chemicals beyond their intended use, but when faced with the need to dispose of chemicals, there are clear and potential liabilities attached to every container. Suppose you arrive on your first day as the superintendent of a course and you stand in front of the chemical building wondering what is inside. There could be any number of things inside that building. Assuming there are no leaks or exposure issues, here is a quick survival guide to properly handle the disposal of chemicals.

The best recommendation is to use the product in a manner that is in compliance with its label. An example would be if an older fungicide product that you were not sure was still viable to spray on greens, could be applied at label rates in the rough to safely use the product as intended while minimizing risks. Then follow label recommended container disposal procedures such as triple rinse, puncture, etc. If you know the product within a container but the label details are unreadable, you can usually find an updated label on any number of websites or contact a local distributor.
The safest way to handle containers with no labels is to leave the products sealed, and turn them in at an official “Clean Day,” pay any fees associated and feel good that no matter what was in the container you did the right thing. “Clean Days” are events that safely collect various chemicals and dispose of them at approved sites to minimize any environmental risks. These community service events are often sponsored by regulatory agencies, environmental groups or similar organizations. You could help sponsor events as an individual, property, GCSAA chapter or other professional association. You can donate time and money or simply raise awareness of the need for and the many benefits of these events.
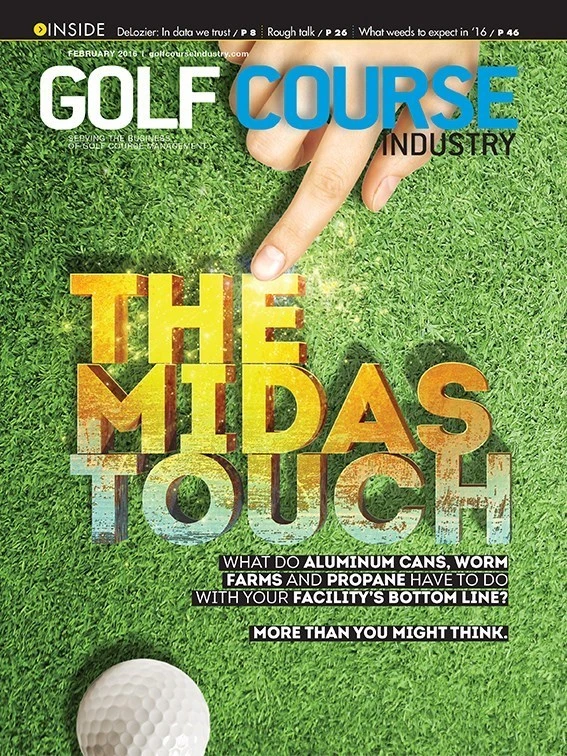
Explore the February 2016 Issue
Check out more from this issue and find your next story to read.
Latest from Golf Course Industry
- GCSAA’s Health in Action 5K/2K reaches fundraising goal
- Landscapes Golf Management to participate in data analyzation initiative
- Reel Turf Techs: Carl Michael
- Atlanta Athletic Club approves funding for master plan
- Maximizing Cultural Practices and Agronomic Benefits with Minimal Surface Disruption
- Real Answers about Spray Nozzle Choices
- From the Course to the Factory: How Customer Insights Drive Innovation
- New & Proven Enzyme Strategies for Sprayable Thatch Management