When the Moody Foundation, a philanthropic organization, became aware the city of Galveston had a municipal course it couldn’t afford to maintain – and planned to bid a management contract publicly – the foundation tossed its hat in the ring, eventually winning the bid. Moody Gardens, which is a destination resort for the Houston market and the name of a company that operates the associated buildings, hotels and a convention center for the city of Galveston, agreed to manage the course and invest the money needed to make it a premier public facility. It was a deal city leaders couldn’t pass up.
“It was basically a gift from the Moody Foundation to the people of Galveston and the state of Texas,” says Buddy Herz, general counsel for the Moody Foundation and chairman of the Moody Gardens Golf Committee.
The Moody Foundation provided funding for the $450-million Moody Gardens complex, which consists of an indoor aquarium, rain forest, space museum, white-sand beach, and a 425-room hotel and convention center that seats as many as 8,000 people within the 65,000-square-foot show center. Moody Gardens manages those facilities for the city without compensation and underwrites any deficits.
The foundation, the city of Galveston and Jacobsen Hardy Golf Course Design worked together to raise the golf course from the sea floor, literally. Galveston Municipal Golf Course – which has been renamed Moody Gardens Golf Course in recognition of the Moody Foundation’s funding of the $15.5-million renovation project – is scheduled to reopen in June.
Jacobsen Hardy was the logical choice to renovate the existing 40-year-old course given the Houston-based design firm’s experience at nearby Galveston Country Club, of which Herz is a member, where it undertook a renovation several years ago.
“The firm is familiar with the challenges of building on Galveston Island, particularly involving the uses of effluent water, complying with the requirements of the Army Corps of Engineers and wetlands issues,” Herz says.
Reshaping the terrain
What made the golf course potentially dramatic also is what made it difficult to rebuild. Located adjacent to the Gulf of Mexico and bisected by Sydnor Bayou, major tidal events would submerge portions of the course occasionally. Bermudagrass and saltwater were a poor mix. Turfgrass was slow to recover following coastal flooding, and the build-up of salts in the soil profile made it difficult to maintain a quality playing surface.
The No. 1 challenge, therefore, was reshaping the terrain and building the ground up and out of tidal areas where seawater occasionally inundated the land. Jacobsen Hardy’s grading and shaping plans concentrated on elevating those areas.
“We developed a balanced cut-and-fill plan that involved 175,000 cubic yards of dirt,” says Rex VanHoose, senior v.p. and managing architect of Jacobsen Hardy. “There was a tremendous amount of water already on the site. That presented a host of playability issues.
“We found an adjacent area and proposed digging a new lake, providing us with significant amounts of fill,” he adds. “The landscape contractor would then dig deeper into a couple of existing lakes to acquire more dirt.”
Senior project executive Bob Walcott estimated his construction firm, Gilbane Building Co., unearthed 200,000 to 250,000 yards of dirt.
While acknowledging the ingenious nature of the lake excavations, Jim Hardy, principal of Jacobsen Hardy, found the humor in it.
“Off-site dirt sells for $14 a cubic yard,” he says. “That would have added a major cost to the project. So we had to find a dirt fairy on site.”
The proposed finished product would be an optical illusion of sorts, Herz says. The greens would appear to be lowered, but in reality, the plan was to raise the entire course an additional two to five feet above the ocean.
A changed layout
With the elevation problem solved, the Jacobsen Hardy team was able to dive into the actual design. Laid out in the 1960s, the existing design was a decent one, although it lacked an adequate practice facility, Hardy says. The only place to practice was a small, narrow parcel where players were restricted to using irons. The architects rerouted many holes, allowing the facility to accommodate a full-size driving range.
“Having a range is very important, particularly in a resort location,” Hardy says. “Many resort guests love to just come hit balls for a few hours.”
Finding enough additional course width and length, while squeezing in a full-sized practice facility, required 50 or more proposed routing plans, Hardy says. Developing a concept that yielded better golf in terms of length, width and linkage, while addressing the Army Corps of Engineers’ environmental concerns, were also difficult tasks.
The development team was fortunate the Army Corps of Engineers’ regional office is located in Galveston. The team checked each new set of proposed plans with the nearby government office. When the team submitted a formal proposal using the regulators’ feedback, they were fairly certain it would be approved.
The sandy seaside location coupled with an ever-present wind, which generally blows from 10 to 20 miles per hour, made the site ideal for a links-style layout with jagged-edge bunkering surrounded by native grasses, reeds and fescues. These characteristics, coupled with the high dunes Jacobsen Hardy designed into the layout, are reminiscent of windswept Scottish and Irish links.
The greens are a bit more bold than the usual Jacobsen Hardy style but still are characterized as a links style.
“They’re more undulating and have more contour than we usually put in, but they’re still very playable,” VanHoose says. “As for approach shots, we left an open entryway into every green to encourage bump-and-run play. And there’s usually a bail-out area to help the higher handicapper.”
The design team did a fantastic job, especially within environmentally sensitive areas, Herz says. The team reversed the first five holes and changed the first six considerably. It tweaked holes seven through nine, significantly tweaked holes 10 through 16, and substantially changed holes 17 and 18.
“We could not have been happier with the final layout,” Herz says.
The choice of paspalum
The development team started designing the course in August 2006. Construction began in March 2007 and was completed in October 2007. The facility has been growing in through the fall, winter and spring months and is on schedule to open in June.
With the constant threat of hurricanes driving seawater onto the fairways and a city requirement to irrigate the course with effluent water, the problems involving salt build-up within the soil profile weren’t about to vanish. Jacobsen Hardy opted to replace the existing Tifdwarf 419 and common Bermudagrass mix with salt-tolerant paspalum, with Sea Isle Supreme on the putting surfaces. Plans were to sprig the grass and sod 20 acres of sloped areas during the summer, but a complication arose when the sod farmer reported the sprigs and sod weren’t going to be ready until September.
“We needed to start grassing in June and July, so we regrouped and hit upon a seeded variety of paspalum called Sea Spray produced by Scotts,” VanHoose says. “We used a hydroseeder and sprayed the entire course except the greens. It worked wonderfully, leaving a seamless transition between fairways and roughs. We double sprigged the putting surfaces with Sea Isle Supreme.”
Developers believe this is the first golf course in the continental United States that, other than the greens, has been seeded completely with paspalum.
One of the ongoing maintenance issues golf course superintendent Steve Yarotsky will face is weed control. Being situated in an environmentally sensitive area, few products are available to control weeds, particularly the original common and coastal Bermudagrass that will inevitably try to reestablish itself.
“Steve is considering using just straight saltwater to control weeds,” VanHoose says.
Related to killing weeds, killing the common and coastal Bermudagrass for the paspalum to thrive is difficult.
“We’ll figure that out as we go,” VanHoose says. “Using salt might be the best solution. It might knock back the paspalum somewhat but not kill it. It will kill the Bermudagrass. Steve can spray a high-salt solution or actually put salt granules on the turf.”
Seashore paspalum expert Ronnie Duncan is working on a program that will help control the return of Bermudagrass to paspalum playing surfaces.
“There’s definitely a learning curve involved with paspalum,” Yarotsky says.
Unexpectedly heavy rains caused by a brush with a major hurricane that dropped eight inches of precipitation in a single day, plus a wetter-than-normal year overall, resulted in a total precipitation that was 15 inches above average in 2007, Yarotsky says. The construction team used matting in the bunkers and other areas to prevent sand and seed from washing away.
Because the existing site was flat, cut-and-fills, new lakes and undulating greens were built to give the course more character. To complete the facelift, landscapers moved 400 existing palm trees throughout the course and added another 300 queen palms. Moody Gardens spent a total of $500,000 on landscaping.
A community asset
The $15.5-million complex breaks down like this: $10 million for the golf course, $2 million for renovating the clubhouse, $1.5 million for a steel maintenance building on an elevated location that will withstand winds of 140 miles per hour, and $2 million to expand an existing desalination plant that cleanses the city-generated effluent water piped from two miles away for use at Moody Gardens and the golf course even more. During the summer, the course will use as much as one million gallons of irrigation water daily.
The Moody Foundation’s willingness to provide an enhanced community asset and absorb any potential losses means Galveston residents will continue to pay green fees of $25 to $30 while visitors will be charged $50 to $75.
And, just as important, the natural environment will continue to thrive.
“The entire course, but particularly the back nine, is environmentally pristine,” Herz says. “Several environmentalists have toured it and loved it.” GCI
Get curated news on YOUR industry.
Enter your email to receive our newsletters.
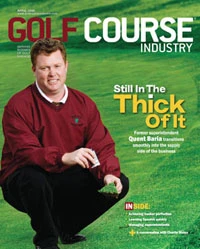
Explore the April 2008 Issue
Check out more from this issue and find your next story to read.
Latest from Golf Course Industry
- Beyond the Page 65: New faces on the back page
- From the publisher’s pen: New? No way!
- Indiana course upgrades range with synthetic ‘bunkers’
- Monterey Peninsula CC Shore Course renovation almost finished
- KemperSports and Touchstone Golf announce partnership
- PBI-Gordon Company hires marketing manager Jared Hoyle
- Mountain Sky Guest Ranch announces bunker enhancement project
- GCSAA names Joshua Tapp director of environmental programs