
Tee box construction and maintenance is one of the more overlooked aspects of the overall golf course construction and maintenance operation. It’s ironic because a course’s teeing grounds make up, along with its greens, one of the two areas of the course visited on every single hole by 100 percent of its golfing customers. The fact remains, however, that sooner or later, whether due to soil compaction, wear due to limited teeing area, faulty drainage, or the need to move or add tees to accommodate changes in golf equipment technology, work will need to be done. If the budget doesn’t allow for a golf course builder, an architect or both, the job falls to the superintendent, who may or may not have experience in course construction.
There are four phases to the tee box construction work: planning, preparation, execution and inspection/documentation of the results. Each is critical, both to ensure a smooth and efficient flow of work and to make sure everyone involved is on the same page regarding scope, budget, scheduling and desired result. For a superintendent taking on this type of construction project for the first time and planning to do the work in-house with the maintenance staff and equipment on hand, these four steps are even more critical.
Planning
The planning phase involves communication with the course owner, general manager or board of directors and/or greens committee chairman if it’s a private club. The superintendent and management must determine how many tees will be involved, the required degree of renovation or reshaping, and if new tees are necessary, how many and where they need to be placed. During that discussion, there will likely be some mention of any limitations on the work in terms of budget, as well as scheduling to minimize disruption of play.
Preparation
Once the scope, budget cap and scheduling considerations are agreed upon, the superintendent begins the preparation stage by researching the cost and availability of materials, equipment, manpower and time necessary to complete the project. If that total exceeds the tentative budget, more discussion with management will be required to either increase the budget or determine which of the elements of the previously agreed upon scope of work can be eliminated or modified.
Jon O’Donnell, president of golf course construction firm Heritage Links, cautions that in calculating costs, superintendents should be sure to include material delivery costs and any taxes, and to track maintenance crew labor hours as part of the cost of work completed. In some states, there is a renovation tax that may be applied, says Doug Long, a Landscapes Unlimited project manager, who adds that before presenting a completed budget to management, superintendents who are Golf Course Superintendents Association of America members may want to ask fellow GCSAA members who have done similar projects to review the budget for accuracy and completion.
It should be noted that as part of the scope of work, consideration should be given not only to the condition of the existing tee boxes, but to their size and their alignment to the hole’s playing surface.
“The first thing, if you’re rebuilding for playability, is that you need adequate tee surface size,” says Pat Karnick, president of golf course builder Wadsworth Golf Construction. “In the South, particularly, Bermudagrass tends to creep in, and your mowing pattern gets smaller and smaller. Also, you want to position your tees so you’re not putting golfers at a disadvantage. Obviously square tees with a straight angle, where the line of play is perpendicular to the tee, are easier.”
The first thing, if you’re rebuilding for playability, is that you need adequate tee surface size. In the South, particularly, Bermudagrass tends to creep in, and your mowing pattern gets smaller and smaller. Also, you want to position your tees so you’re not putting golfers at a disadvantage. Obviously square tees with a straight angle, where the line of play is perpendicular to the tee, are easier.” — Pat Karnick, Wadsworth Golf Construction
Execution
Once scope of work and budget have been defined and materials and equipment have been procured, the work can begin. Again, the extent of the actual construction will determine not only the cost and time involved, but the complexity of the work. The most basic tee surface touch-up can be done by stripping off the tee surface level of turf, laser-leveling it to ensure that the teeing areas are level, and sprigging or re-sodding the surface. Depending upon the soil quality and local climate, a layer of sand may need to be added. In some cases, a layer of pea gravel needs to be added under the 4-6 inches of sand base.
Some courses, particularly those who have recently done work on their greens, may want to reuse the old greens mix instead of straight sand to save money without sacrificing quality, Karnick says.
In some cases, particularly where clay soils are prevalent, compaction of tee box turf has occurred and the sub-surface soil will need to be roto-tilled or otherwise loosened up. Rick Benson of Tifton, Ga.-based Benson Construction recommends lowering the depth by 2 to 4 inches and laser leveling it, then adding sand or greens mix and laser leveling once again to ensure a proper grade.
The need for sufficient slope on both the tee surface and the surrounds to facilitate drainage is a critical element adding cost and time. Proper drainage on the tee surface itself requires anywhere from ½ to 1 percent slope front to back (or vice versa) and the same side to side, Benson says. Wadsworth’s Karnick adds he prefers a 2 percent slope due to water’s slow movement across grass.
Contractors also caution that slope and drainage issues are not confined to the actual tee box surface.
For example, in some instances, slope adjustment involves going as much as 5 to 10 feet outside the tee surface, says Richard Hagy, vice president of golf and irrigation for Aspen Golf. Moving that much dirt to the proper specifications may require an experienced shaper. Likewise, superintendents must tie the side slopes into the existing grade, says golf course architect Richard Mandell.
Irrigation piping and drainage is another element to slope, and proper drainage is configured to drain from the sides of the elevated tee surface. This is to avoid drainage onto the paths, assuming the cart paths are located in close proximity to the tee boxes.
Inspection/documentation
Additional concerns should be addressed for the protection of both the superintendent and the course. O’Donnell cautions superintendents should ensure they have reviewed safety precautions with maintenance staff, as this type of work is different than their usual tasks. He also suggests contacting the course’s insurance company to ensure “construction” is covered for club employees who will be doing the work.
Landscapes Unlimited’s Long also recommends superintendents doing the work in-house be careful about underestimating the time needed to complete the work, re-grass the tees and make the tees playable. Long has seen a number of in-house projects run out of time before either inclement weather ends the work or, conversely, the work runs into the course’s busy season.
And, not insignificantly, there are some elements of self-preservation and job security involved. O’Donnell notes the importance of communicating the purpose and schedule of the work to not only course management, but also to course members or customers to mitigate complaints over disruption of play or construction distractions.
The inspection/documentation phase of the project is designed to ensure the tee box has been shaped and graded correctly to produce the proper slope, the irrigation to the teeing area is working as planned, and the drainage is functioning properly. Once the job has been approved, the final step is to document time, labor and material costs of the project.
“It’s important to document what has been done for a variety of reasons,” Long said. “The owner or the club’s board is going to want to see where the money was spent, and the final figures will be helpful in terms of any future budgeting, or possibly for consideration in course valuation for tax purposes.”
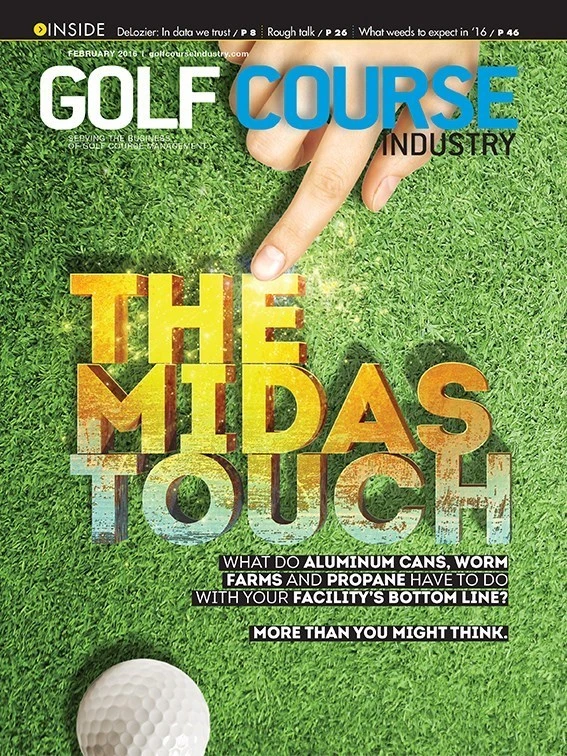
Explore the February 2016 Issue
Check out more from this issue and find your next story to read.
Latest from Golf Course Industry
- Indiana course upgrades range with synthetic ‘bunkers’
- Monterey Peninsula CC Shore Course renovation almost finished
- KemperSports and Touchstone Golf announce partnership
- PBI-Gordon Company hires marketing manager Jared Hoyle
- Mountain Sky Guest Ranch announces bunker enhancement project
- GCSAA names Joshua Tapp director of environmental programs
- AQUA-AID Solutions bolsters Sunshine State presence
- Escalante Golf acquires secluded Illinois course