Sodium’s effect on a turfgrass plant is like putting tape over a person’s mouth, says Hans Gardner, golf course superintendent at Falcon Ridge Golf Course in Mesquite, Nev.
“Salt plugs up the sites on the roots that intake air, water and food, so the plant is only taking up a small portion of what you’re putting down,” he says, equating that to a human who can’t ingest food or water and starves as a result.
“If you don’t get rid of the salt, you’re pretty much wasting fertilizer and water,” Gardner says.
There are natural and man-induced reasons golf courses register high levels of sodium and other salts in soils and water. For example, it’s common for coastal golf courses to suffer from high salt irrigation water. Arid regions, too, are typically predisposed to soils that accumulate salts because irrigation water evaporates quickly before it can move the minerals through the root zone, leaving sodium behind.
Another common reason for the problem is the use of effluent water, which typically has high sodium levels thanks to water softeners and other treatment processes.
With the public’s increasing attention on water conservation and with only about 12 percent of courses currently using effluent water, few would dispute the number of facilities using effluent water will skyrocket in the years to come. That means more superintendents will be charged with navigating the challenges that come with highly sodic irrigation water.
Making applications
Just as there are a number of reasons for salt problems, there are a number of ways to mitigate them. David Soltvedt, CGCS, at the Ridge at Castle Pines North in Castle Rock, Colo., has dealt with what he calls a moderate sodium problem since he arrived at the 18-hole, daily-fee facility in 2004.
If nothing else, in his 12-year career working at six golf courses, he’s learned water quality is relative.
The year Soltvedt arrived at the Ridge, the metropolitan water district forced the facility to switch from well water to an effluent/well water mix. Now, Soltvedt irrigates the course with an 80/20 mix. Since 2004, sodium levels have increased almost 500 percent.
“Our water isn’t that bad – probably a five on a scale of one to 10 in effluent water quality – but nonetheless, our water isn’t making it any easier,” he says. “It’s not so poor that we have to use sulfur injection like many facilities in the southwest.”
For the Ridge, the biggest detriment of having high sodium water has been the soil’s inability to drain properly, especially in low areas. These circumstances resulted in the installation of about a mile’s worth of drainage since 2004, costing the facility about $25,000.
Soltvedt’s ongoing plan to manage the sodic water includes applying wetting agents and calcium sulfate (gypsum). He also uses salt-tolerant turfgrass, Brightstar SLT ryegrass, when he grows in a new sod nursery or fills divots. The course has Poa annua/ryegrass fairways, Providence bentgrass greens, bentrass/ryegrass tees and bluegrass roughs.
Because sodium displaces calcium and magnesium in the soil, Soltvedt applies calcium sulfate at a rate of 500 pounds per acre to greens and tees annually. The application takes place during aerification; the material is applied and dragged in. At $800 a year, the cost of calcium sulfate is just a sliver of the maintenance department’s annual budget, which Soltvedt declined to disclose.
Additionally, Soltvedt spends about $8,000 annually on wetting agents, which are injected in to the irrigation system, to help the water move through the soil.
In Mount Dora, Fla., Philip Morris Jr. also makes regular applications to control a salt problem created by effluent water. The golf course superintendent at Mount Dora Golf Club has been dealing with sodium-plagued, soil-sample results for the 18 years he’s been at the 18-hole semiprivate course. On seven different occasions during his tenure, the green committee has talked about rebuilding the greens as a result of the sodium problems.
“This year, they were talking about spending a couple hundred thousand dollars on rebuilding the greens,” he says. “But with the way the economy is, the bank said we couldn’t rebuild.”
Morris, who maintains the course with a $100,000 annual budget, asked for freedom to experiment this year to control the problem – dull, thinning greens that generally weren’t responding to fertilizer.
“I said, just let me play around; don’t tie my hands down,” Morris says, noting two of the greens were registering sodium levels of 44 percent and 38 percent, classified as very high. “You would have thought I was taking a soil sample from Daytona Beach.”
In April, Morris began monthly applications of a soil amendment called SaLibré at a rate of 32 ounces per acre. By late October, the sodium levels on the two problem greens mentioned above declined to 17 percent, classified as moderate. Morris says he’s happy with the results, considering he uses about a half gallon per application, which costs less than $50 a month.
“With a small budget, you’ve got to be creative, and if you find a product that works, you don’t stray too far from it,” he says.
Adding equipment
Though Soltvedt and Morris haven’t needed to install equipment to mitigate their water quality issues, Gardner can’t say the same. Like most of the golf courses in southeast Nevada, Falcon Ridge Golf Club in Mesquite has a sulfur burner, which is a 5- by 3- by 3-foot machine that heats sulfur on-site to create sulfurous acid, which is the injected into the irrigation system.
Gardner has been at the 18-hole public course, which he maintains with a $1.2 million annual maintenance budget, for a year and a half, and had a hand in purchasing the system. He says all four courses in the area he’s worked on during the past 14 years have had a sulfur burner. Sodium problems are common in southeast Nevada, Gardner says, because many courses use effluent water or water from the Virgin River, which registers high mineral levels in the summer when it runs low.
Gardner grapples with salt levels that vary greatly from hole to hole – from below 200 parts per million to as high as 750 parts per million.
Superintendents use sulfur burners – or the alternative, sulfuric acid injection systems – for two primary reasons: displacing salts from the soil and clearing moss and algae from lakes and waterfalls by lowering pH levels quickly. The machines create sulfurous acid, which lowers the alkaline conditions in the water, which neutralizes the bicarbonates that harden the soil and deny water penetration. This process, assuming the course has adequate drainage, allows sodium and other minerals to be leached out of the soil.
One stigma these units face is they emit strong odor and that can be distracting for golfers and employees. Gardner says that was the case with earlier units, but that’s not a concern with newer ones, like Falcon Ridge’s.
The sulfur burner, which Gardner purchased from Aqua Dulce for about $15,000, burns about five to 10 bags of sulfur per day. Falcon Ridge consumes about a ton of sulfur every three weeks. Gardner estimates he most recently paid about $800 a ton for sulfur, which, like many commodities related to golf course maintenance, has been on the rise. In fact, the cost caused him to cut back in the late summer and early fall months since the weather has cooled down and the sodium-related issues lessened. He plans to run the machine again for a few weeks at a time when the weather warms up in March or April and again in May and June.
For Gardner, the battle to eliminate salt problems is an ongoing process.
“Unless you find a way to get rid of the salts, the plant doesn’t thrive at all,” Gardner says about Falcon Ridge’s turf, which is a bermudagrass base overseeded with ryegrass in the fall.
Gardner augments the sulfur burning process with a twice yearly process in which he aerifies, applies gypsum at about 500 pounds per acre and then waters heavily to leach the salts down into the soil.
The real key, though, is keeping up with the soil’s status through quarterly tests.
“We get the results, and then we do what we need to do when we need to do it,” Gardner says. GCI
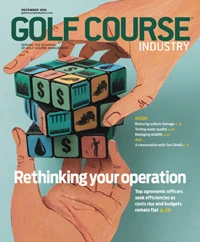
Explore the December 2008 Issue
Check out more from this issue and find your next story to read.
Latest from Golf Course Industry
- Heritage Golf Group acquires North Carolina courses
- Editor’s notebook: Green Start Academy 2024
- USGA focuses on inclusion, sustainability in 2024
- Greens with Envy 65: Carolina on our mind
- Five Iron Golf expands into Minnesota
- Global sports group 54 invests in Turfgrass
- Hawaii's Mauna Kea Golf Course announces reopening
- Georgia GCSA honors superintendent of the year