For the past 12 years, I’ve mended an 18-year-old little orange Smithco spray truck as parts wore out. It is a heavy hauler by turf equipment standards, carrying 1,200 pounds of liquid in its orange fiberglass tank. More precise, the spray truck is a Smithco Spray Star 1602 with TeeJet spray system. It has three booms across the back; the two outside ones lift up and fold down alongside the tank. It is a compact arrangement, but since the shop and storage area have 12-foot high doors, the booms clear (just barely) when up. On the outermost tips of the booms are foam markers. The foaming agent/water mix foams when mixed with air from the onboard compressor and forced through a sponge at the end. The foamers leave a trail of shaving cream like globs of white foam. The booms are raised and lowered using the same Thompson linear actuators that are on our John Deere Aercore 800.
Frequently, I see it on the course from the shop door. The driver riding in its single seat over the front wheels is always dressed in a white disposable spray suit and hood, with purple gas mask cartridges on his spray mask and bright blue disposable gloves. The chemical mix has a bright blue color added to it to warn the rest of us who may work around the machine where chemicals are on the machine (or floor). It takes a great deal of rinsing to get the blue color off of the machine after spraying, but when dealing with industrial-strength chemicals, caution is essential.
To do repairs, I need it to be very clean so I don’t have to work in gloves. For areas I have to work on that still show a hint of the blue warning color, I clean with sodium hypochlorite – Clorox spray bleach cleaner. This not only cleans the color off but chemically oxidizes any of the herbicide/pesticide that may be hanging on.
Other than oil changes, the spray trucks 20-hp gasoline engine has required practically no attention. The belt clutch though stands out as the weak link in the drive line because if the belts come off or break, it is at the most blue-covered times in the middle of a tank run. Tank mixes need constant agitation and can only sit idle for a short time, which puts serious pressure on any repair.
Pump seal, tires, valves, plastic tubing, sight glass, switches, every system on the truck has had part of it replaced. A few more adventurous repairs come to mind. For example, the rear end started making a bad noise and finally one day the machine quit moving forward. The differential drive gear had stripped. After a long consultation over the phone with the parts department a rear end was found in the warehouse that would work if we also changed the universal joint that goes with it. It was here in a couple of days and was installed the day after that.

Get curated news on YOUR industry.
Enter your email to receive our newsletters.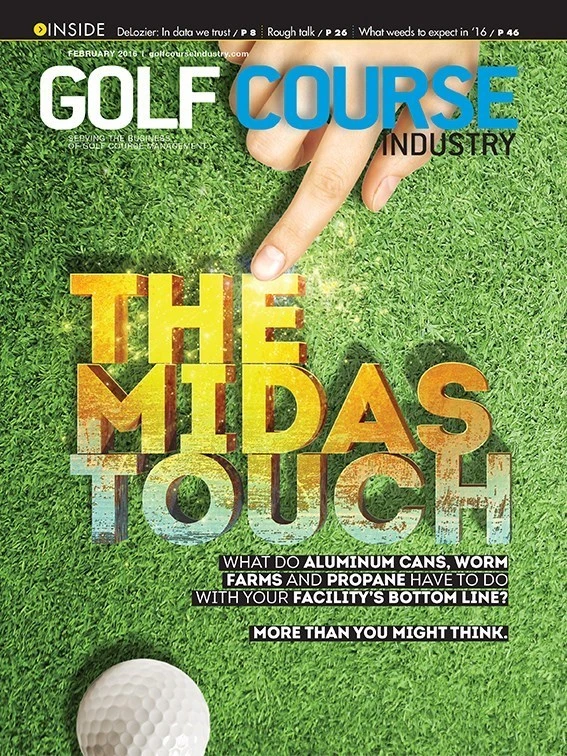
Explore the February 2016 Issue
Check out more from this issue and find your next story to read.
Latest from Golf Course Industry
- GCSAA’s Health in Action 5K/2K reaches fundraising goal
- Landscapes Golf Management to participate in data analyzation initiative
- Reel Turf Techs: Carl Michael
- Atlanta Athletic Club approves funding for master plan
- Maximizing Cultural Practices and Agronomic Benefits with Minimal Surface Disruption
- Real Answers about Spray Nozzle Choices
- From the Course to the Factory: How Customer Insights Drive Innovation
- New & Proven Enzyme Strategies for Sprayable Thatch Management