
Ken Nail’s workdays at TPC Tampa Bay begin when the crew meets at 5:30 a.m. inside a maintenance facility nestled between West Lutz Lake Fern Road, the first tee and ninth green, and a spacious practice area. Once the meeting ends and co-workers scatter to the always packed Florida course, Nail follows a greens mower to the practice green.
He intently observes a few passes. If the Bermudagrass surface doesn’t look as tidy as expected or a mower doesn’t hum as intended, he can immediately troubleshoot. If everything looks and sounds acceptable, he returns to the maintenance facility and creates a checklist for the day. Sunrise means another trek outdoors to inspect how machines are performing on regulation surfaces. Nail then returns to the shop again, this time to begin making repairs. Mowers return to the maintenance facility a few hours later, and Nail checks cutting units and tunes the machines for the next day.
A veteran equipment manager who works in a market where machines operate year-round, Nail avoids rigidity when plotting hours, day, weeks and months. “You can sit there and make a plan for the day,” he says, “and by 5:40 that plan is out the window.”
In a colder spot amid industrial settings in another country, Tim Thurston can relate to what Nail experiences. Thurston worked as a superintendent and sold turf equipment before settling nicely into a role as the equipment manager at Ambassador Golf Club in Windsor, Ontario, a busy public course across the Detroit River from the homonymous American city. He understands why plans matter. He also realizes there will be mornings like the one he encountered in early October, when Ambassador superintendent Steve Hatch needed him to mow greens. “One thing in this position, you never know what you might be needed for,” Thurston wrote in an email shortly after completing the assignment.
Thurston is Ambassador’s gate-opener, arriving at the course on peak-season mornings at 4:30 a.m. He begins the morning walking through cold storage areas, visually inspecting equipment for oil leaks, flat tires and other abnormalities. He then opens the back doors and stages equipment the Ambassador team needs for the day. Greens are mowed daily; fairways are typically mowed on Mondays, Wednesdays and Fridays. When Hatch arrives, the duo chat about the upcoming day. “If he’s going to try to do something different, I find out about it right away,” Thurston says. Surprises are non-existent when the crew arrives. Thurston knows who’s headed where and on what piece of equipment.
Outdoor checks are built into Thurston’s routine. He begins traversing the Thomas McBroome layout around 30 minutes after morning assignments commence. He spends at least an hour on the course checking cuts and listening for odd noises. Repairs and the administrative parts of the job consume late mornings and afternoons. Modern equipment managers spend more time on computers and phones than their predecessors. Thurston estimates he’s on the computer for around three hours per week ordering parts, compiling budgets and communicating via email. “I’m totally fine with being on a computer or phone,” he says. “It’s something I learned from being in sales.”

Shawn Bergey, the equipment manager at Philadelphia Cricket Club, a 45-hole facility with golf courses spread across two campuses, says finding computer time during the peak season can be tricky. “It’s very hard to take five seconds and read my emails or do something like that,” says Bergey, who leads a team of three responsible for maintaining more than 200 pieces of engine-propelled equipment. “I always tell these guys in the shop that we’re firefighters. All we’re doing in the summers is putting fires out, just getting a machine running and getting it out of here to the point where our guys can do their work.”
Grinding becomes a major part of the job during the winter, although Bergey’s team performs what he calls “touchups” on disfigured blades and reels during the peak season. “Just because we’re grinding,” he says, “doesn’t mean that everything else stops.” And outdoor work rarely halts at high-level clubs such as Philadelphia Cricket Club. There’s always another tree to trim or hole to trench, which are tasks requiring specialized equipment requiring regular maintenance.
Asked if it’s possible for an equipment manager to follow a plan, Bergey responds in East Coast candor. “It’s not even close to possible,” he says. “Whoever told you they don’t do a daily schedule is 100 percent correct, because if you do that, you might as well already plan on getting it destroyed.”
Ryan Haptonstall quickly comprehended the necessity of adaptability. A former diesel mechanic who transitioned to the golf industry in 2020, Haptonstall started 2023 at a new job as the equipment manager at Avon Oaks Country Club in Cleveland’s west suburbs. His routine evolves depending on veteran superintendent Terry Boehm’s needs. A room possessing the equipment lift, toolbox and Haptonstall’s desk rests outside Boehm’s office.
“You’re not just working on engines or working on cutting units,” Haptonstall says during a late-summer conversation below the lift. “Yesterday I was a trailer-repair guy. I patched up a hold and fabricated some latches for it. Other days you’re solving other weird kinds of problems, like the windows aren’t going down on Terry’s truck. You have to come up with a lot of weird stuff on the fly. Situational fabrication.”
Haptonstall executes reoccurring tasks early in the day. He pulls into the maintenance facility on the northwest corner of the Avon Oaks property at 5:30 a.m. Neither quiet nor solitude greet him. Busy Interstate 90 sits a well-struck mid-iron from the building and a few loyal part-time crew members retired from other industries are already preparing for their assignments. Haptonstall walks the storage area examining equipment. He considers himself fortunate because experienced operators make similar checks before heading to the course. “A lot of the guys here notice stuff and they are all about the machines,” he says. “They like to be on them. If they notice something, they want me to fix them right away so they can get back out there.”
Greens mowers undergo the most rigorous pre- and post-mowing inspection. Haptonstall regularly places the units on the lift. He checks rollers to ensure there’s “no play in them,” and clips paper to test quality of cut. If the paper requires forceful contact to clip, Haptonstall knows he must swap or grind the reel. Elevating a machine allows him to thoroughly inspect units for leaks, grease and rust.
Prioritization follows the morning hustle. Equipment managers strategically shuffle between tasks on days critical repairs aren’t required.
“I have developed the patience and understanding to step back if I get frustrated and move onto something else,” Kenosha (Wisconsin) Country Club equipment manager Justin Prescott says. “One of the great things about being on the golf course is that there’s so much to do. I can walk away from one project — unless it’s absolutely necessary to get it done — and do something else for a little bit and return to it.”
People create the biggest variable for an equipment manager. Rookie and experienced operators, superintendents, assistant superintendents, sales professionals, mobile service technicians, general managers, pros, kitchen staff and even members can creep into an equipment manager’s day.
“I’ve always been a planner, so that was one of the tougher things,” says Justin King, the equipment manager at Jamestown Park Golf Course, a municipal facility in Jamestown, North Carolina. “When I had something I wanted to get done, it seemed like no matter what, I was getting pulled somewhere. The more I talked to and met the people in the industry, the more I’ve come to realize that’s just how it is. In the last couple of years, I shifted my mindset and just accepted it.”
TPC River Highlands equipment manager Robert Martyszczyk finds on-course communication to be productive. The rolling land bordering the Connecticut River soothes minds and offers abundant spots for casual and technical conversations. Private conservations outdoors, especially with new operators, yield respect for the equipment and the role Martyszczyk plays in keeping it running.
“They might not want to ask a question in front of the group like, ‘Hey, I forgot about this,’” Martyszczyk says. “It’s a good way to get to know the summer crew and build that rapport. They can talk to me and see that I’m approachable.”
Ansley (Georgia) Golf Club equipment manager Trent Manning estimates he spends 10 percent of his time on the course observing equipment, inspecting quality of cut and “coaching” operators. Nail recently encountered issues with the cleanliness of equipment following assignments. He explained to operators in private and group conversations how clean equipment benefits the course and their personal work routines. “Minor things can turn into big things down the road,” Nail says. ArborLinks (Nebraska) equipment manager Bryan Epland jokes that sometimes his job feels like “it’s 30 against one.”
Nobody affects an equipment manager’s routine or morale more than a superintendent, thus making the relationship between the pair the most important interpersonal dynamic within a turf team. Fractures in the relationship can damage workplace culture and negatively impact the presentation and playability of a golf course.
Equipment managers interviewed for this series indicated failure to communicate invasive cultural practices such as aerification, verticutting and topdressing in advance can erode the relationship with a superintendent. Equipment breakdowns are unpredictable; major agronomic events can be placed on a calendar.
“I’ve had superintendents who really didn’t communicate that well,” Nail says. “They would pop things on you at the last minute. It’s like, ‘You really knew about this for a week and you’re just telling me the day before?’ That’s so disheartening.”
Joe Moreira, the equipment manager at 27-hole Etowah Valley Golf Club & Lodge in western North Carolina, says it sends a powerful message when a superintendent shows interest in his position and overall well-being. Family-focused schedules and professional development opportunities demonstrate to an equipment manager their importance to a course’s success. Monday-Friday schedules are common among equipment managers.
Quality relationships aren’t all take. The best professionals understand they are one cog in a larger operation.
“The superintendent can’t think the turf and course are above all more important,” Prescott says. “As an equipment manager, you can’t think the equipment above all is more important. You have to understand you are an integral part of wherever you are. But you have to make sure, just like your machines, to make everything work. If there’s no grass to cut, I don’t have a job.”
Get curated news on YOUR industry.
Enter your email to receive our newsletters.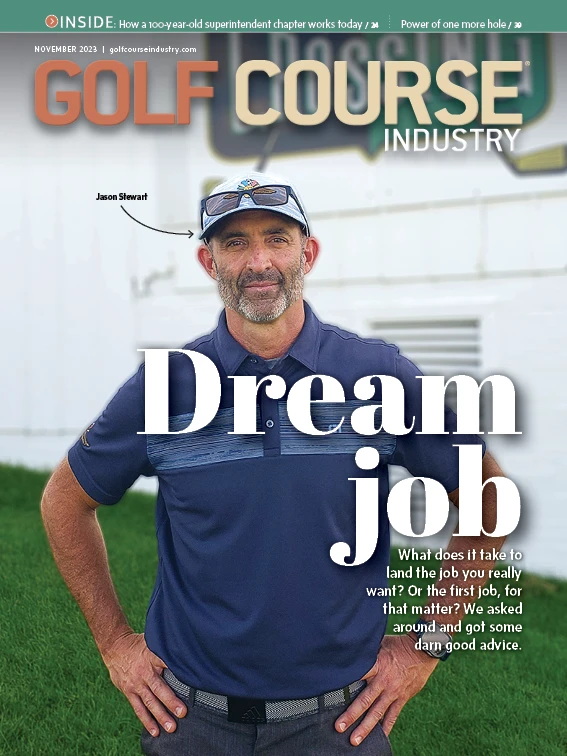
Explore the November 2023 Issue
Check out more from this issue and find your next story to read.