
If you’ve had an irrigation pump station crap out on you, then you know how quickly costly repair bills add up. Avoid these unwanted, budget-busting charges, by better utilizing downtime – especially during the slower off-season months – to make sure your irrigation system’s heart is in top working condition.
Start with a proactive approach. Visit your pumping station come green-up time and use the hours available to you during the slower winter months to make sure your irrigation system’s main driver is ready to go for the upcoming season.
“It is important to do a proper and thorough check of your pumping station to prevent unexpected failures,” says Willie Slingerland, a Watertronics regional sales manager. “Identify possible problems before the pump station is needed for the season.”
Following a winter or offseason hibernation, Bill Stinson, golf pump sales manager/Eastern U.S for Rain Bird, recommends enlisting an experienced golf pump service company/technician to perform preventative maintenance services during non-irrigation months. When possible, use the same technician who winterized the system the previous fall, he says.
This is not as daunting a task as it may seem, taking perhaps three to five hours total to complete. “It is not a lot of time, but it may not be able to be done in-house, says Brian Vinchesi, design engineer for Irrigation Consulting Inc. “But it is worth doing as it will operate the pump system better, prevent catastrophic failure and the pump system will last longer.”
Preventative maintenance goes a long way. “I am a big fan of cleaning out pump houses and cleaning pump systems,” Vinchesi says. “Some pump houses are dirty and cluttered and you can’t move around in them, while others are spotless,” he says. “The cleaner the better for equipment.”

Paint should be touched up on the piping and building. Holes should be sealed. Polishing paint repels dirt accumulation, and painting the walls and floors keeps dust down. “Make sure fans and vents, as well as doors, have operating hardware and repair as necessary,” Vinchesi says.
It also helps hiring a qualified service technician to go through each and every part of the pump station’s operating system, Slingerland says. “There are safety issues with regard to entering and servicing a panel that most likely has three-phase power,” he adds.
Another key area of the pump station to check is the control panel, says Brian Keighin, a principal of Irrigation Technologies. He recommends keeping the interior of the panel clean, making sure door gaskets are intact, pliable and providing a good seal, and checking how cabinet cooling system are operating. This keeps all electronic components at the correct operating temperature and prevents overheating and premature failure, he says.
“Check electrical connections to make sure they are tight,” Keighin adds. “Check and double check that the power is off and there is not transient charge before completing this step. Also, check to make sure all mechanical fasteners are still factory tight. Clean the filter elements, replace damaged/worn elements and check operation of the filter system after cleaning.”
Superintendents must check the station’s flow sensor calibration to determine if it is within the manufacturer’s specifications, Keighin says.

In addition, pump packing seals should be adjusted or replaced if there is excessive water coming from the pump shaft. Dynamic flow testing should be done on each pump. They should be within the design specifications for volume and head.
“An underperforming pump is an indicator of potential failure,” Keighin says.
Each motor’s amp draw should be checked, as well. Too high a draw can identify a motor that is beginning to fail. “Insure that fertigation systems are plumbed properly and not dripping/leaking, and that pressure gauges are working and reading correct values,” Keighin says. “And the station’s heater or building heating system must be working properly to prevent possible freeze damage.”
The experts agree a wise move for superintendents is to have a factory authorized pump service technician complete an annual service on the station.
“Who knows the pump station better than a factory-trained professional who has access to service bulletins and technical information on the pump station,” Keighin says.
Pump station maintenance is a confusing issue. And since most people are not adept at a pump station’s inner workings, maintenance often gets overlooked or mismanaged, says Ashley Wilkinson, a golf and sports turf professor at Horry-Georgetown Technical College.

Inspections of the wet well and intake line should be done bi-annually. “I have seen numerous issues regarding this basic task,” Wilkinson says. “Depending upon location, barnacles, algae, shells and other biotic issues may arise and clog the intake screen. I have seen intake lines literally fold in half as they were unable to draw water.” Many times, a diver will report the intake screen is no longer present due to debris shifting or metal disintegration. This inspection may indicate a jetted intake screen is needed. A jetted intake screen will use high pressure water to blast debris away from the screen to avoid clogs.
A diver should check if the intake line is still two to three feet off the lake bottom to reduce sediment being pulled into the intake line, Wilkinson says. “The diver should check for cracks in the intake line that will allow sediment or fish, and even turtles, to enter the wet well,” he adds. “If this occurs, the wet well may fill with silt/mud and create low pressure issues as the vertical turbines cannot pull the water through the heavy silt.”
Inspect the wet well for gaps and cracks, Wilkinson says. A corrugated wet well is prone to decompose over time, allowing metal particles to collect and, eventually, get sucked into the propellers of the vertical turbine ruining them. If the preferred concrete vault wet well has settled, the gasket keeping a water tight seal may be compromised allowing soil to leak in or, worse, water may leak out and compromise the stability of the pump station pad. Lastly, the diver should check for rust underneath the skid, inspect the condition of the turbine baskets and see if excess silt has filled the bottom of the wet well.
Checking or changing the turbine oil should be done annually. At the same time, greasing the bearings should be done if it is not a sealed unit. Some manufacturers or service associates say to change the oil every 1,000 hours. Checking the packing should also be done. Adjustments should be made to make sure the packing is tight, so the unit is being cooled properly. If excessive heat is being created due to warm packing, the pump will eventually need serious repair.

“My recommendation would be to have all this work done through a service call,” Wilkinson says. “However, with proper training during that call, there is no reason this annual service can’t be completed in-house in the future.”
Checking all electrical connections to make sure no wires have come loose should be an annual task. Small vibrations in the unit and excessive heat during operation or summer use can loosen connections, which may create a short. “I would never tell any grounds manager to open the cabinet,” Wilkinson says. “It’s just too dangerous. But pulling the outside wires to see if they are tight is a reasonable maintenance task.”
When restarting for a new season, the “most crucial” would be those places that are exposed to outside elements. “This means pipes and tubes that have been subjected to high and low temperatures,” say Cary Harris, director of marketing for Gicon Pump. “Make sure there is also no damage from other sources, such as trucks, tractors, etc. Places that are easy to overlook are those that aren’t easy to see. Inside electrical panel, critters build nests and cause damage to wires and components. Pipes that are submerged may also be damaged or rusty.”
Stinson says performance testing will entail operating the station at full capacity to ensure it is meeting specified pressure and flow, and to confirm the incoming power grid can handle full demand. If the system fails the test, run each pump individually at its designed flow and pressure, to uncover performance issues.
“Don’t skimp on the pump station service and repair, as it’s vital and therefore mission-critical,” he says. “Once the inspection is completed, all details should be thoroughly documented. This is important from a trend analysis and predictive maintenance standpoint.” Ignoring known problems and the signs of potential problems will likely result in greater expense, frustration, and often “embarrassment.” Respond immediately to signs/symptoms that surface from the inspection.

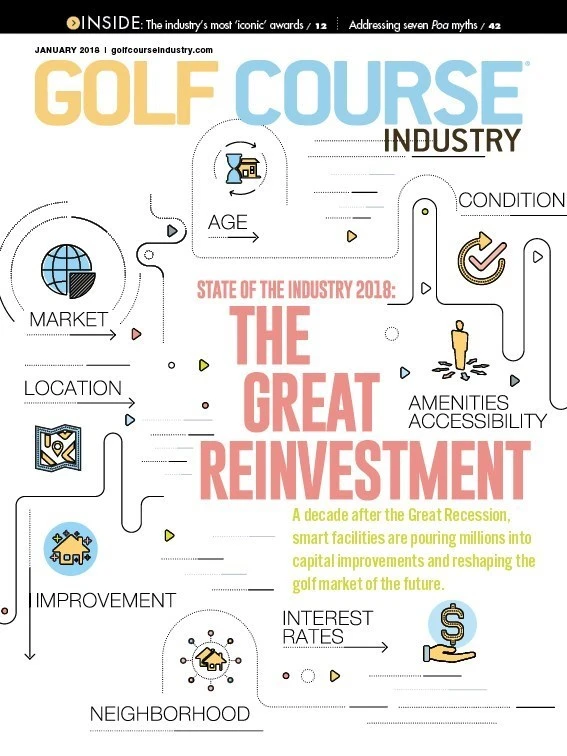
Explore the January 2018 Issue
Check out more from this issue and find your next story to read.
Latest from Golf Course Industry
- Toro continues support of National Mayor’s Challenge for Water Conservation
- A different kind of long distance
- Golf Construction Conversations: Stephen Hope
- EnP welcomes new sales manager
- DLF opening centers in Oregon, Ontario
- Buffalo Turbine unveils battery-powered debris blower
- Beyond the Page 66: Keep looking up
- SePRO hires new technical specialist