Even though LESCO sold its supply chain assets and consumable products inventory to Turf Care Supply Corp. last year, the manufacturing plants that were part of that sale are still vital to the company’s business.
A seed plant in Silverton, Ore., and three manufacturing and blending fertilizer plants – in Martins Ferry, Ohio; Hartsfield, Mass.; and Sebring, Fla. – were part of the sale. Currently, LESCO is the only customer of TCS.
Part of the reason why
LESCO sold its manufacturing assets is the company wanted to invest in opening new Service Centers and Stores-on-Wheels vehicles to boost sales, rather than invest in equipment and machinery in the manufacturing plants, according to chief operating officer Bruce Thorn. The company has 311 Service Centers and 114 Stores-on-Wheels vehicles throughout the country.
“We’ve been doing this for a long time,” says Brian Rowan, associate vice president of merchandising, referring to the company’s distribution business. “It takes a long time to bring good products to market, and the sale of our assets won’t affect that.”
Currently, LESCO is going through a transitional period with TCS, which has been smooth. There have been no changes or impacts that have distracted from the company’s business, according to Thorn.
“We still have strategic partnerships with Turf Care Supply, and it’s only going to improve,” Thorn says. “The only time that we would go to another manufacturing company other than TCS is when the net cost would be better than what Turf Care can supply us, i.e., a remote market we want to enter.”
Part of the company’s continued growth is a pipeline of new granular and liquid fertilizer products, according to Rowan.
“We’re looking for more economical products and distribution,” he says.
Fertilizer production process
Fertilizer sales account for 25 percent of LESCO’s business, so it’s no surprise fertilizer production is important to the company. The plant in Martins Ferry, Ohio, is the biggest of the three fertilizer plants now run by TCS. There are 135 permanent workers, 30 supervisors and as many as 30 temporary workers there. The plant blends pesticides and fertilizers and produces sulfur-coated urea.
The plant, which is an old pipe-coupling factory that LESCO purchased in 1987, doesn’t have a perfect layout because it has been expanded throughout the years, according to Paul Ferrell, director of formulating. Urea is brought up the Ohio River and unloaded at the plant – dumped onto a conveyer below ground that takes the urea above the plant via an elevator. About 100,000 tons of urea a year go through the plant.
During the past three years, the price of urea has increased 50 percent because it’s tied to natural gas.
Two tanks, each containing 30,000 gallons, heat the sulfur to 280 degrees. The urea is about 75 degrees. Because the process involves adhering them together, the urea needs to be heated. The coating occurs continuously in large, long rotating drums. When the sulfur-coated urea comes out of the drum, it’s 160 degrees. Then, the polymer is coated in another drum to seal the sulfur-urea mix.
During the process some particles stick together. These are called “popcorn” and are unusable for the lawn care and golf markets, so the company sells them to farmers, who don’t need a specific size particle. One-half percent of the product produced is “popcorn.”
The urea is produced in three different sizes: the largest for the lawn care market, the smallest for greens and tees in the golf market, and the size in between for fairways in the golf market.
Another section of the plant contains bins that hold as much as 1,100 tons of fertilizer. All bins are filled by overhead conveyors.
For packaging, limestone is used as filler in the bags because the nitrogen-phosphorus-potassium ratio won’t equal 50 pounds. Bulk density and particle size factor into producing bags of fertilizer. Corn cobs, nut shells and clay also can be used as filler, but clay tends to stick to the product, according to Ferrell.
Labels on the fertilizer bags aren’t pre-printed because state regulations can change. The labels are approved by the Environmental Protection Agency and then stuck on the bags at the plant. The bags are color coded – red for insecticides, green for fertilizers, blue for post-emergent herbicides, yellow for pre-emergent herbicides and orange for fungicides.
Seed
Although it might be overshadowed by the fertilizer business, LESCO has a strong foothold in seed, which is 15 percent of its business. The big difference between the fertilizer and seed segments of the market is that with seed, the company is competitively in the same boat as everybody else because the majority of seed is grown in Oregon, according to Thorn.
“We work with a number of individuals to grow and test seed,” he says. “Right now, we have the No. 1 [National Turfgrass Evaluation Program]-rated bentgrass – Authority creeping bentgrass. From our contract research and development folks, we’ll have 15 to 20 new varieties a year. We’re constantly looking for more seed varieties. When we see trends taking place, we can redirect our own efforts.”
Despite all the new varieties, no contracted researcher and developer for the company is working on seashore paspalum.
Thorn says the company, now that it has sold its manufacturing assets, can be more focused on developing new products and look to other partners to manufacture them. n
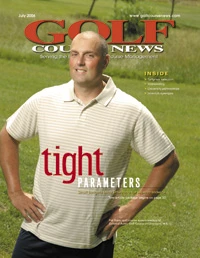
Explore the July 2006 Issue
Check out more from this issue and find your next story to read.
Latest from Golf Course Industry
- Advanced Turf Solutions and The Aquatrols Company release soil surfactant
- Heritage Golf Group acquires North Carolina courses
- Editor’s notebook: Green Start Academy 2024
- USGA focuses on inclusion, sustainability in 2024
- Greens with Envy 65: Carolina on our mind
- Five Iron Golf expands into Minnesota
- Global sports group 54 invests in Turfgrass
- Hawaii's Mauna Kea Golf Course announces reopening