As most of us know the golf course restoration and irrigation business is booming. It is hard to find a qualified builder or irrigation contractor that has room in their schedule to do small projects, let alone large scale 18-hole renovations or irrigation systems. One down side of these “good times,” however, seems to be a “downturn in” or a “lack of” product quality.
Unfortunately, of late, while reviewing irrigation materials for projects or watching systems operate after installation, I have noticed many more product issues than I usually do or have in the past. I have always seen isolated problems, but lately it seems to be across the board along a wide variety of products, including pipe, wire, sprinklers, controls and manufactured assemblies. It has ranged from sprinklers not staying in adjustment to the wrong breaker being installed in a manufactured electrical assembly to pipe not being properly cut into lengths at the factory to a used (bad) circuit board being installed on a new controller.
Poor quality equipment has a number of downsides, but the one I find most troubling is the time it takes for someone – usually the superintendent – to figure out there is a quality issue and the frustration that occurs in the meantime because of it. I recently watched a superintendent and his two assistants waste a day-and-a-half chasing down a control gremlin that was finally diagnosed as a manufacturer known product defect, but none of the distributor or applicable manufacturer field and service personnel knew anything about it. Many times, you don’t know there is an issue until there is a large dry spot or dead turf. In other instances, something just plain doesn’t work and you cannot water at all. It’s always worse in the summer to get help because people are on vacation or shorthanded or would rather be doing something else than dealing with your problems.
The easiest way to circumvent product issues is to catch them before they are installed. Take a good look at the products when they arrive on site and look for gouges, scratches, nicks and that things such as pressure settings are correct.
The real issues show up once the equipment is in the ground and working. Now that things are buried, troubleshooting is more difficult. Rely on distributor personnel and colleagues who have similar systems to determine if they have seen the same issues and how did they find them. Also rely on them to fix the issues because manufacturers are not always upfront about announcing their product issues.
Quality issues should also be compensated for whether it be you or the contractor making the fix. This includes both the material and labor costs. If it is really bad, assess a dollar amount to the responsible party for pain and suffering. When you buy a product, you expect it to perform the way it was promised to and designed for. When it doesn’t, hold those who made that promise responsible, otherwise product problems continue to occur.
I have also seen a definite quality downturn in product shipping. It seems that everything used to be shipped on a truck inside a contained trailer. Now a lot of things are being shipped on an open trailer pulled by a large ton pickup truck. Product is more difficult to move and not as well protected. No one likes to communicate bad news, either. Recently we had a pump station that was supposed to be delivered on a Monday and the trucker broke down on Friday, but he didn’t let anyone know until he was tracked down that Monday afternoon – crane, contractor and electrician all waiting around costing money.
Product and installation quality issues are a problem for everyone involved in a project – manufacturer, distributor, contractor, end user and even the designer. Fewer issues, the better, but there are most likely going to be an issue or two in any significant project. When you have an issue you think is installation or product oriented, let the responsible party or parties know immediately. The more eyes on a problem, the sooner it gets rectified. You may also save one of your colleagues the same heartache.
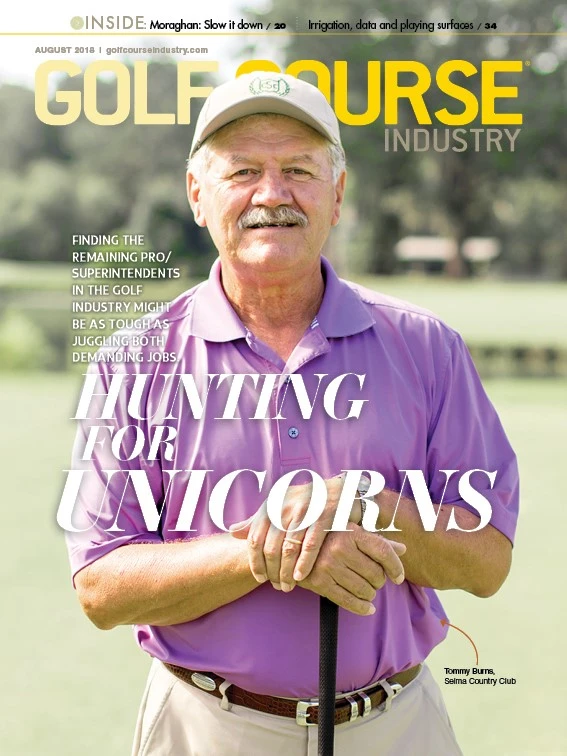
Explore the August 2018 Issue
Check out more from this issue and find your next story to read.
Latest from Golf Course Industry
- From the publisher’s pen: Technology diffusion and turf
- Applications open for 2025 Syngenta Business Institute
- Smart Greens Episode 1: Welcome to the digital agronomy era
- PBI-Gordon promotes Jeff Marvin
- USGA investing $1 million into Western Pennsylvania public golf
- KemperSports taps new strategy EVP
- Audubon International marks Earth Day in growth mode
- Editor’s notebook: Do your part