
Smirks start, eyes roll, chuckles ensue. Randall Pinckney realizes the reactions when peers hear about his latest agronomic endeavor.
Pinckney is seven months into his tenure as superintendent at Sewickley Heights Golf Club in the hilly, swanky and secluded Pittsburgh suburb of Sewickley. Large parts of his days are filled with preserving and protecting Poa annua.
Sewickley Heights’ leaders are embracing Poa. On greens. On an ambitious timetable. “I get a lot of cross-eyed looks: Why would you not go to bentgrass?” Pinckney says.
What the Poa is happening at Sewickley Heights?
Like supporting an NFL team with six Super Bowl rings or eating sandwiches topped with fries and coleslaw, promoting Poa greens are a Pittsburgh thing. Sewickley Heights director of golf David Malatak says one must grasp the region’s private club landscape to understand why it would renovate greens and resod them with its existing Poa.
A weed in some places, the stuff that makes greens slippery elsewhere, Poa is a desired turfgrass on Western Pennsylvania greens. Nine-time U.S. Open host Oakmont Country Club sits atop the region’s golf hierarchy. Poa is the dominant variety on Oakmont’s greens. It’s also the dominant variety on the greens of Sewickley Heights’ private club neighbors.

“In Western Pa. it’s understood,” Malatak says. “That’s why the club voted 90 percent to get this done – because that’s what we always wanted. When we started telling people in my era in our area what we are doing, people are like, ‘OK, that’s great.’ Doing the project might be crazy, but putting the Poa back down doesn’t seem that crazy to a lot of golf pros that I know.”
Crews from GCBAA member Aspen Golf started mobilizing at Sewickley Heights Aug. 22. Less than two weeks later, GCI toured the work with Pinckney, Aspen Golf vice president Richard Hagy and architect Jim Cervone, ASGCA. Pinckney has spent the majority of his career in Maryland; Hagy and Cervone have worked everywhere yet reside in Western Pennsylvania. A schism exists when they are describing the project to various audiences.
“In this area the major clubs have (Poa) and people look at you and say Poa is what you need to do,” Hagy says. “But some people look at me like, ‘They are doing what? Why aren’t they putting bentgrass down?’ Everybody wants their Poa in this area and we can give that to them.”
Opened in 1961 and designed by Jim Harrison, Sewickley Heights spent its first half-century with push-up Poa greens resting on clay-based soils. As drainage deteriorated, the club resorted to bentgrass for the first time in its history, seeding four greens to the variety in 2011. Bentgrass, though, didn’t click with the membership, Malatak says.
Golf drives decisions at Sewickley Heights – the club doesn’t have a pool or tennis courts – and after six months of deliberation the membership felt comfortable pursuing a major project to enhance its greens. The project has a rapid rhythm, with a goal of completing around two greens per week during a two-month period.
The process entails stripping sod, coring, overhauling drainage, reconfiguring the irrigation system for greens and approaches, placing 4 inches of gravel and 12 inches of an 80-5-15 sand, soil and peat mix, and relaying sod from another green. “The cool thing about this as a whole is that we would always have a green open so they could core out, drain and flop sod from one green to another green when it was ready,” Pinckney says. “We never had sod laying on tarps.”
Sod from Boyd Turf in New Wilmington, Pa., supplements the existing Poa. The sod is grown via plugs taken from Sewickley Heights. Pinckney worked closely with Jeff Michel of M&M Consulting to develop the proper mix. M&M collected samples from the greens rebuilt in 2011 and the 11th green, Sewickley Heights’ best-performing Poa green, according to Michel. Testing was conducted through Brookside Laboratories to understand the physical and chemical composition of the rebuilt greens and 11th green and to mimic those properties in the new mix. M&M also sampled successful Poa-based greens at other clubs. Cooperation from Wendell Boyd and Brian Bates, and developing a custom fertility package consisting of Gypsum, Pro Mag, poly-coated potassium sulfate and poly-coated methylene urea which was blended into the mix at 5 lbs/ton of mix by the plant are allowing workers to float and install sod without additional input during construction, Michel says. “The resulting media has physical and chemical properties that will lead to an extremely high probability of success with this project,” he adds.
Sewickley Heights has three acres of greens, with the biggest surfaces exceeding 8,000 square feet. All 19 greens – the putting green is also being resodded with Poa – remained opened until Aug. 22. Once work started, members continued playing on unaffected holes, although the entire course will eventually close in early fall. Other work includes moving the second and third greens to new locations, renovating the ninth and 15th tees, and adding multiple bunkers. To protect sod, the membership granted Pinckney and his crew permission to halt aggressive greens management during the month leading into the project. The decision helped navigate a toasty start to 2016: the course had received less than 10 inches of rain through August. Sewickley averages close to 40 inches per year. Regular messages from club president Matt DiAndreth, greens chairman Ted Kotarsky, Pinckney, Malatak, and communications sent via the private club social network program Clubster helped members understand the reasons for pre-construction decisions such as decreasing green speeds.
“It’s one of the most unique projects I have heard about in the business,” Pinckney says. “With the rapid scope of the project – the schedule is quick – and to fully core out and resod Poa annua greens all in one season is something that … It’s a big challenge for me knowing what I was going into and going through the process and talking with people in the business, I don’t know anybody that has done it.
“There are a couple of clubs that will do one green. My staff isn’t just worried about one green. They are worried about the whole course. It’s the Poa annua still not dying and where on any other project you would let the greens go to crap because you are rebuilding them. Here we have to keep them healthy and going back to the club allowing us to do that was huge.”
Preparation and communication led to an encouraging start. The first Poa stripped and moved displayed 3- and 4-inch roots within two weeks after being placed. The green, one of the four bentgrass surfaces, was mowed twice, rolled twice and topdressed during the stretch.
Cutting Poa proved tricky early in the process. Crews used three sod cutters before identifying one that could produce even strips. New blades are being installed weekly to ensure 3-foot strips are even before being rolled up. Thickness ranges from five-eighths to three-quarters of an inch. “We would like to be at a half-inch, but if we are cutting a half-inch, what happens is that as soon as we hit a spot, then we have nothing and we are wasting sod,” Hagy says. “So we are going a little bit thicker to make sure we are not wasting. We can always fill in a spot that’s low later, but we don’t want to waste a lot of sod.”
Projects involving stripping and reusing existing Poa sod on the same course’s greens are rare, according to Hagy, who has spent 35 years in the industry. Hagy lauds Pinckney for the smooth start. “One of our biggest concerns was to make sure we had big enough roots to work with when we went in to strip, Hagy adds. “And, fortunately, Randall did a great job of making sure we had that. Nothing is going to waste so it’s going very good. I couldn’t ask for a better start to project.”
Pinckney served as the superintendent when Manor (Md.) Country Club underwent a major renovation which included installing A-1/A-4 bentgrass greens. His ability to steer Manor CC through construction and grow in convinced Sewickley Heights’ leaders he could guide the club through a tricky renovation on a short timetable, Malatak says. Most of Pinckney’s recent experiences involves managing bentgrass in the Transition Zone, although he managed bentgrass/Poa greens at Piney Branch (Md.) Golf Club, where he received his first head superintendent job.
After a punishing summer, Pinckney and his crew are welcoming cooler fall temperatures. Winter damage is a concern, and Pinckney says covers will be used on greens that have experienced past problems and greens sodded in the later stages of the renovation. Moving excess sod to Sewickley Heights’ nursery will provide insurance in the event of a harsh winter. “We want snowfall, but not freeze-thaw and open desiccation from the wind,” Pinckney says.
Next year, Pinckney adds, will represent “a learning curve” for his crew. Developing the ideal soil mix to promote healthy Poa and installing hookups for SubAir Systems as part of the renovations provide further protection for issues that might arise.

Early in his involvement at Sewickley Heights, Cervone says the club emphasized it relishes slick greens and the flavor of its putting surfaces. But subtle work with percentages and slopes will offer more potential pin placements. Cervone has worked with Aspen on multiple projects, and came close to working with Pinckney on a renovation in the early 2000s. Living in Western Pennsylvania allows Cervone, who was involved in numerous fast-paced projects during China’s golf boom, to be on site two or three times per week.
Operating on expedited timetables is the norm for Aspen, which sent a team of 30 workers led by project manager Ken Morgan to Sewickley Heights. The team also includes an employee solely dedicated to coordinating GPS measurements.
“I have been on several projects where we have gone in to augment an existing green and stripped it and relayed sod, but never something to this degree,” Cervone says. “I think the club should be applauded. Everybody has embraced it and it’s certainly worthy of getting it out there to let people know what we are doing. It’s unique for sure.”
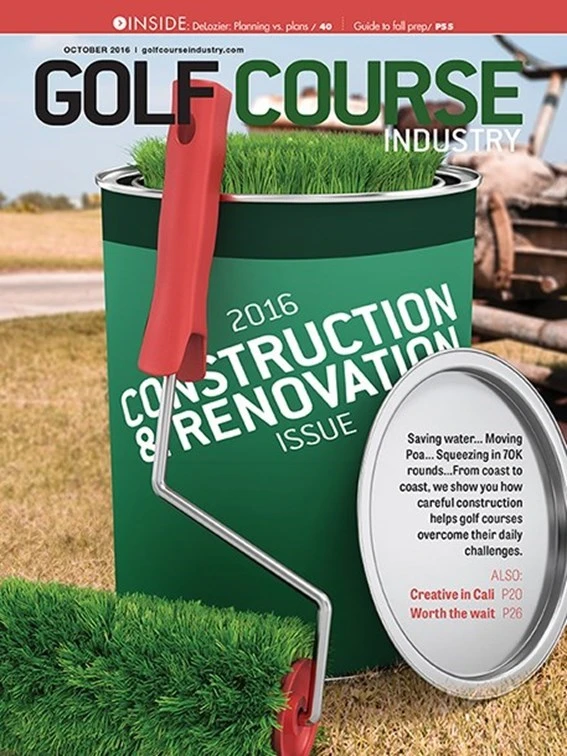
Explore the October 2016 Issue
Check out more from this issue and find your next story to read.
Latest from Golf Course Industry
- From the publisher’s pen: Technology diffusion and turf
- Applications open for 2025 Syngenta Business Institute
- Smart Greens Episode 1: Welcome to the digital agronomy era
- PBI-Gordon promotes Jeff Marvin
- USGA investing $1 million into Western Pennsylvania public golf
- KemperSports taps new strategy EVP
- Audubon International marks Earth Day in growth mode
- Editor’s notebook: Do your part