If you’re a regular reader of this column, you know I favor a comprehensive master planning approach to renovation. However, the reality for 2009 is that most renovations will focus on fixing specific problems rather than improving design. The renovation projects I see now are irrigation replacement, bunker sand replacement and greens regrassing. In a cost-sensitive environment, you can minimize your renovation cost through targeted design and minimally invasive course construction techniques.
If you want to make true design changes, it’s important to work well beyond the remodeled green or bunker to tie in changes to the surrounding ground and make it look right. But as a work area increases, the cost of resodding it increases substantially, more so than simply replacing bunker sand and/or adding liners, and often becomes cost prohibitive.
If cost is a hindrance, changes should focus on necessary design improvements, such as routing overland drainage around bunkers, moving bunkers closer to the green, or downsizing bunkers to reduce future maintenance costs. Changes should be targeted to areas that allow working from inside the bunker as much as possible.
Aside from design, it’s important to retain a contractor who has experience in targeted renovations because it’s difficult to budget for cleaning up after a messy contractor. I spoke with some of the best contractors I’ve used on smaller renovations to learn about their secrets about working clean. They said it’s a matter of having an attitude of “leaving it better than we found it” and a methodology that emphasizes small machines, hand work and minimizing damage.
“Our philosophy is to leave it the way we found it, which is a lot more expensive,” says Max Beins, president of Wildcat Golf in Wichita, Kan. “It’s difficult to compare bids when one company bids to restore the damage and others have no intention of cleaning up.”
To minimize the need for cleanup, Wildcat often uses conveyor belts to fill bunkers with sand from the cart path to avoid driving on turf.
Beins says the company has lost many bids for renovation work during the first phase of a project but is often brought in for the second renovation phase because of its reputation for working clean, even at higher cost.
Minneapolis-based Park Construction’s philosophy centers on not opening up too many areas before others are complete to minimize a mess, says Don Slegers, golf division manager. It also chooses its equipment carefully, buying Ford trucks instead of other brands because they’re substantially lighter and using equipment with nonaggressive rubber treads. When hauling material, crews are instructed never to load to maximum capacity. Slegers also stresses communication between the contractor and club members is always paramount.
Don Henderson, president of Land Constructors in Southlake, Texas, seconds the notion that besides attitude, equipment choice is a key to working clean.
During bunker renovation, he avoids using any type of bulldozer. Instead, he uses lightweight Cat 310.5 minihoes, which have rubber cleat tracks that can move along cart paths without damaging them. He changes buckets for different tasks within the bunker to minimize damage, and like the others, relies on a qualified hoe operator and a lot of hand labor inside the bunker. He adds sand to bunkers using a Tycrop dump trailer towed by turf utility vehicles rather than tractors that can go anywhere with minimal damage.
Jeff Cordes, regional manager for Lincoln, Neb.-based Landscapes Unlimited jokes, “We keep the plywood industry in business by covering all haul routes.”
The company also uses plastic covers on exposed areas during rain events and uses central stockpiles, planning optimal haul roads, hauling material in small amounts, working its way out of corners and cleaning up as they go.
So, what does all this mean for your targeted renovation? Even more so than for bigger projects, you should consider:
- Choosing contractors based on references for similar projects.
- Accepting a higher bid because a low bid may cost you more in the long run to clean up behind the contractor.
- Clearly specifying the methodology, equipment, haul routes and cleanup in the construction agreement because each is integral to your project’s success.
- Asking for the company’s most experienced small-projects operators.
Even for small “surgical” procedures, it makes sense to do all you can to improve the course. Thus, while many clubs feel using a golf course architect for smaller projects isn’t cost effective, using one that’s sensitive to construction realities can help you develop the best possible program to balance cost and constructive design changes that make sense within your budget. GCI
Jeffrey D. Brauer is a licensed golf course architect and president of GolfScapes, a golf course design firm in Arlington, Texas. Brauer, a past president of the American Society of Golf Course Architects, can be reached at jeff@jeffreydbrauer.com.
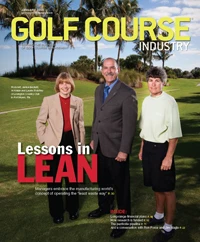
Explore the January 2009 Issue
Check out more from this issue and find your next story to read.
Latest from Golf Course Industry
- The Cabot Collection announces move into course management
- Carolinas GCSA raises nearly $300,000 for research
- Advanced Turf Solutions’ Scott Lund expands role
- South Carolina’s Tidewater Golf Club completes renovation project
- SePRO to host webinar on plant growth regulators
- Turfco introduces riding applicator
- From the publisher’s pen: The golf guilt trip
- Bob Farren lands Carolinas GCSA highest honor