Bald Peak Colony Club spends time and money to properly renovate and expand its golf course maintenance facility.
Are you considering renovating or expanding the maintenance building(s) at your golf course? A review of the maintenance facility improvement project at Bald Peak Colony Club in Melvin Village, N.H., provides information that might help you with such a project.
Bald Peak, a private club designed and built in the early 1920s, is the centerpiece of a gated residential community tucked into the rural countryside along the shoreline of Lake Winnipesaukee, the largest body of water in New Hampshire.
The original 70-year-old maintenance facility was a renovated, 4,500-square-feet barn that had insufficient lighting and ventilation. Bald Peak’s two mechanics operated in limited workspace. Equipment was stored outside at several locations throughout the grounds. The need for change was apparent, so in the fall of 2000, the management team began discussing long-range plans to replace the facility.
To start with, it’s important for the superintendent or club officials to involve qualified professionals at the earliest possible stage of any major project, according to Todd Pollini, superintendent of golf and grounds, and Ralph G. Beckett, a long-time club member and green chairman. The professionalism they bring to the process can increase communication to the entire membership.
Bald Peak’s first step was hiring Braintree, Mass.-based Sports Club Management to perform a safety compliance audit of the entire operation.
“It clearly detailed conditions, including the areas where we were deficient,” Pollini says. “It laid out the [Occupational Safety and Health Administration] regulations and federal laws and analyzed our facilities in relationship to them. It took the project from a concept of better conditions to the level of needing a new facility because of X or Y or Z.”
The detailed report helped the club determine during the early planning stages that renovating the existing facility wouldn’t accomplish their goals because it wasn’t big enough and there were too many compliance problems.
In June 2001, the club put together a 10-person, long-range planning committee. About 85 percent of the membership belongs to at least one other club somewhere else in the country. Three of the committee members belonged to clubs that expanded their maintenance facilities and brought that knowledge to the table.
“They all agreed we shouldn’t crimp on space,” Pollini says. “The clubs that had done so were asking for additional space within two or three years. We wanted a facility that would last 50 years. So instead of starting with a set price range, they decided it would be more efficient and cost effective over the long term to define what was needed first and then determine the cost.”
The Bald Peak project also included the renovation of employee housing on the premises. Because many employees come from other regions of the country to work at the club during the summer, on-site housing allows the club to attract and retain the number of qualified individuals they need. The two existing facilities were adjacent to each other. The committee proposed combining the two renovations into a single project.
Explore regulations
Every municipality has requirements for permitting and documenting construction, renovation or expansion projects. Golf facility management should discuss these issues with the city’s planning or zoning board at the development stage of the process. The information then can be shared with the architect, engineer or design/build firm to reduce changes during the design phase and avoid construction delays.
“The town of Moultonboro required a new site plan for our facility to clearly define boundary lines,” Pollini says. “Our site covers hundreds of acres, so this was an extensive and expensive part of our project development.”
Most golf course managers, architects, engineers and contractors are familiar with state and national regulations, but it’s important to make sure all information is up-to-date in these areas before developing the design.
Develop a wish list
In the summer of 2001, as the committee interviewed firms to design the project, Pollini was working to develop a punch list of the facility’s features.
“You have to do your homework,” he says. “We visited other courses and talked with those involved with facility renovation projects. We also made sure to address issues that had come up in our safety audit.”
Bald Peak’s goal was to develop an environmentally sound, safe and modern facility, and the committee took a proactive approach to achieve that. Along with other features, their stipulations included: ample workspace for the mechanics; office facilities for Pollini; an indoor wash-bay system to protect against water runoff; a containment area for waste oil; a series of state-licensed and-certified fuel tanks; a separate, contained reel grinding area; separate storage areas for paint and fertilizer; and a separate, contained painting area.
With an average of 20 to 23 golf course maintenance employees each season, a safe, comfortable environment also was planned. Features included an employee lounge with storage areas and kitchen facilities, and separate men’s and women’s restrooms, showers and sleeping quarters.
The design process
Bald Peak’s committee interviewed several firms before determining to use the services of a design/build company rather than separate architectural firms and construction companies. The company selected an in-house architect. Pollini, his assistant and the two mechanics worked closely with the architect to develop the floor plan. They combined his expertise in the layout with their knowledge of what they wanted to achieve functionally.
While the original punch list might not have been as detailed as one supplied by an architectural firm, it provided a sound base that was less challenging to adjust during the construction process. An engineering firm reviewed and approved the design before construction began. Overall costs were reduced, and the club ended up with outstanding facilities for the expense, according to Beckett and Pollini.
Bald Peak expanded its maintenance facility from 4,500 square feet to 22,000 square feet. It also added 4,000 square feet of pole barn storage for trucks and tractors plus topdressing, sand and salt bins.
“Don’t be concerned about making it too big,” Pollini says. “That won’t happen. All of our space is being utilized. It doesn’t take long to fill it up.”
The employee housing renovation created comfortable living space for as many as 42 people within the three-story structure. The former maintenance facility was converted to a common recreational area and is positioned between the two larger structures, creating a separation between the work and residential spaces.
Presenting the proposal
Because Bald Peak is a seasonal club that has about a 3.5-to-four-month period during which the majority of the members are present at the same time, the project presentations needed to occur within that time frame.
Christian Coulter, CCM, Bald Peak’s general manager, was the key communicator throughout the presentation process.
“The general manager has more exposure to the membership than the superintendent does,” Beckett says. “Chris was very open to questions and comments at any time. He and the committee were excellent communicators to the board and membership during official presentations and town-hall meetings. Our club requires a membership vote on expenditures of $250,000 or more. This project was approved on the first vote.”
Construction began in the fall of 2002, and the maintenance staff moved into the new maintenance facility in June of 2003. The project took 2.5 years from the first stage of development to completion.
“If our Web site had been up and running during the process, we would have provided constant updates on the project,” Pollini says. “That resource wasn’t available to us at the time. But this project demonstrates the club’s commitment to employee safety and excellent working conditions because they undertook it before focusing on renovating the golf course and restoring the clubhouse.”
Pollini and Coulter conducted tours for the members when the facilities were completed.
“The tours were well attended and a big success,” Beckett says. “It’s obvious all the employees take pride in the facility and have a greater sense of its value to the club, which is reflected in job performance.”
Rating the results
Bald Peak is heading into the third year in the new facility, and the results are outstanding, according to Pollini.
“I’d rate it nine to 9.5, with 10 being ideal,” he says. “There are a few things I’d tweak if we were to do it again, but they’re minor compared to the positive big picture. The workflow is much more efficient. The design emphasizes safety, which reinforces our training in those areas. We’ve gone 15 months without an accident report.”
The impact of the maintenance facility project on employee morale and improved job performance is impossible to measure in dollars, Pollini says.
“The golf course is what brings the members to the club,” he says. “The quality of the maintenance facility only enhances the finished product and the course itself, and it shows. There is value gained for all the club members by having a quality maintenance facility. It’s not just money spent.” GCN
Steve and Suz Trusty are freelance writers based in Council Bluffs, Iowa. They can be reached at suz@trusty.bz.
Get curated news on YOUR industry.
Enter your email to receive our newsletters.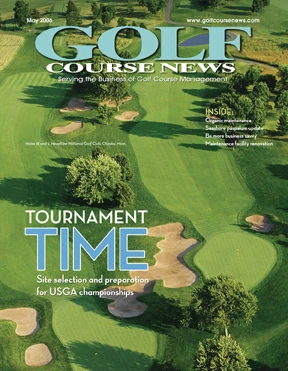
Explore the May 2006 Issue
Check out more from this issue and find your next story to read.
Latest from Golf Course Industry
- GCSAA’s Health in Action 5K/2K reaches fundraising goal
- Landscapes Golf Management to participate in data analyzation initiative
- Reel Turf Techs: Carl Michael
- Atlanta Athletic Club approves funding for master plan
- Maximizing Cultural Practices and Agronomic Benefits with Minimal Surface Disruption
- Real Answers about Spray Nozzle Choices
- From the Course to the Factory: How Customer Insights Drive Innovation
- New & Proven Enzyme Strategies for Sprayable Thatch Management