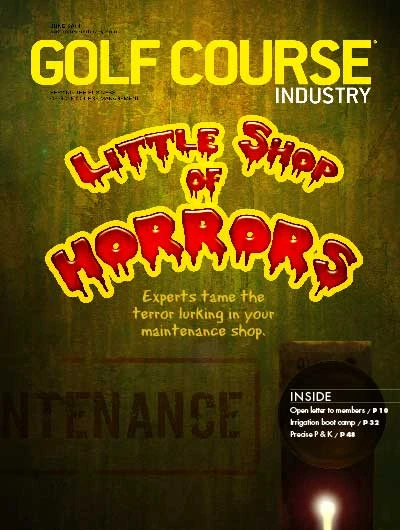
The maintenance shop at Walnut Creek Country Club in South Lyon, Mich., is likely smaller than your living space.
To round it off, Hector Velazquez, the club’s equipment manager, says he’s operating within a realm of 1,000 square feet.
The tight confines don’t bother Velazquez.
“Personally, I like a small shop,” he says. “It keeps everything close to you.”
Velazquez is a maintenance shop guru, having rearranged his shop four times in two years at Walnut Creek. The process can be tedious, yet the reward is high. More importantly, the risk is low.
“I still have my fingers, I still have my toes,” says Velazquez, who has spent 14 years working in golf course shops. “I have not experienced anything really serious in a shop, whether that’s attributed to maintaining a clean shop with training. ... I would like to think that’s helping.”
The perils of a maintenance shop, regardless of its size, are numerous and often overlooked when evaluated alongside the demands of maintaining other parts of a facility.
In short, not many shops resemble the one at Walnut Creek, where curious members sometimes visit.
“In over 25 years as a superintendent, I only remember one time when a member made a comment about my shop,” says Mickey McCord, founder of McCord Golf Services and Safety. “You always get comments about the course: ‘The greens are too fast or too slow. The bunkers are not raked properly.’ There’s virtually no interest in going in that shop.”
Until something goes wrong.
A combination of flammable and hazardous materials, electrical outlets, poor lighting, noise, abundant equipment and high employee traffic can make the maintenance shop one of the most dangerous parts of your facility.
Some experts and superintendents consider a shop a danger zone for any employee.
“It’s the most unsafe place,” says Todd Miller, president of Golf Safety, which provides safety programs to more than 400 courses. “Country clubs, for the most part, are fairly safe. There aren’t a lot of accidents in and around them. Machinery is the first place where an accident can happen and second is the shop, where slips and falls happen.”
Maintaining a safe shop doesn’t require a large budget or vast space. But it’s not as easy as throwing yellow and black tape on the ground and stowing equipment not required for daily use.
Here are six trouble points and ways to avoid mishaps.
Don't let it start to burn
Portable fuel cans are a necessity and nuisance.
Bill Godkin, Owner of CESafety, works with more than 60 golf courses and presents superintendents with a checklist of fuel-related issues to consider.
“Do you have flammable gas cans?” Godkin says. “Are they sealed and labeled? Are they in a flammable storage cabinet? Who’s pumping the gas and diesel fuel? Have they been trained? Are they wearing goggles and gloves?”
Debbie Swartz, a regional sustainability expert for ePar, has worked with superintendents since 2003. She says extinguishers should be placed in highly visible spots and checked regularly.
Loose rags, paper and wood should not be placed near the flammable storage cabinet, McCord says.
Fertile spot for accidents
Chuck Barber, CGCS, can relate to Velazquez. His shop at St. Charles County Club in St. Charles, Ill., is more than five decades old and was considered small even by 1950s standards. The chemical and fertilizer room is 6 by 10. The small area causes big concerns.
“Trust me,” Barber says, “it’s something I lose sleep about.”
Proper storage and training are required when dealing with pesticides and fertilizer, McCord says. “It’s a touchy subject,” he says. “The stuff we use is not as hazardous as people make it out to be if it’s stored properly. It is (hazardous) if people who not have been trained are handling them. That’s the issue.”
Only trained members of the staff can enter the chemical and fertilizer room at Walnut Creek. When inside the room, they are greeted by clear signage and sheets documenting usage.
“There’s a lot of money in that room and there are very few people allowed in there,” Velazquez says. “They keep each other accountable. It keeps a lot of mistakes from happening.”
Swartz encourages placing a spill kit in rooms storing pesticides and fertilizer. Some states require the practice.
“If something does spill off the shelf, you want to put something down to absorb that material so nobody slips into that material,” she says. “And hopefully there’s no drain so the material doesn’t make it out into the environment.”
Swartz recommends three spots for spill kits in a maintenance shop: storage room, shop area for hydraulic devices and on the sprayers themselves.
Safe investments A small investment in maintenance shop safety can yield long-term savings for a facility. Todd Miller, president of Golf Safety, which provides safety programs to more than 400 golf clubs, says his research shows that every $1 spent on safety will save a facility $3. “It’s a very good investment for a club,” Miller says. Mickey McCord, founder of McCord Golf Services and Safety, says superintendents should view safety as an investment instead of an expense. McCord’s company produces a 12-part video series. The videos, which are in English and Spanish, last between 9 and 17 minutes each. Multiple videos are geared toward issues that might arise in a shop. Bill Godkin says money is not an excuse for a lax or non-existent safety programs. “If someone says I don’t want to spend a fortune on training videos, I’m like, ‘They are $300 to $400 from the ABC company,’” says Bill Godkin, owner of CESafety, which produces safety programs for more than 60 golf courses. “My reaction is, if you don’t want to spend that, make your own. You’re the superintendent. You know how to inspect a shop. Do it inside the shop. There’s your training. It’s cheap, but it’s pertinent.” Cultivating a safe shop provides multiple benefits to facilities, says Debbie Swartz, a regional sustainability expert for ePar. “If you are going to prevent an injury or save a life, that’s priceless,” Swartz says. “How can you put money on that? On top of that, economically, if a property were to implement a number of these measures and document them, I think they would have good reason to work with insurance companies to say we have reduced or eliminated our risk because we have taken all of these steps in these areas of potential risk.” A proper safety program helps a facility avoid government fines. Inspectors from Occupational Safety and Health Administration started increasing their visits to golf courses when new construction slowed because of the recession, according to Miller. An OSHA spokesperson told GCI there were 85 inspections conducted and 212 citations issued to golf courses in 2013. There were 26 inspections conducted and 92 citations issued to golf courses in 2014 through May 21. Government fines can be hefty. OSHA fined the Guam International Country Club $32,900 in 2011 for 17 alleged workplace safety violations found at the maintenance shop. OSHA offers free on-site consultation visits from compliance assistance specialists to small- and medium-sized businesses. The visits, which are separate from enforcement, do not result in penalties or fines. They are designed to identify hazards, offer compliance advice and assist in establishing injury and illness prevention. Priority is given to high-hazard worksites. “Unless it is something life-threatening, they will give you a list of things where you are out of compliance and say, ‘Here you go. No fines or penalties. You have a time frame to get things in shape,’” Swartz says. |
Staying upright
Equipment leaks and particles carried in from the golf course can make a shop floor as slippery as a frozen pond.
“Slips, trips and falls lead to more compensation claims than anything else,” McCord says. “You can go back and look at the records. You see sprained ankles, skinned-up knees from guys falling down, broken wrists. Tripping is a hazard from not keeping a shop tidy and not paying attention.”
Cleaning spills immediately and displaying signs until affected spots are completely dry are obvious ways to reduce shop stumbles.
Designate areas for tasks requiring oil and batteries, and direct worker traffic away from those areas, says Swartz. The areas prevent the substances from entering a drain and negatively impacting the environment.
Barber places rugs at door entrances and uses commercial grips to improve traction. Velazquez keeps hose and cord reels off the ground to create fewer tripping hazards.
Don't cut the cord
Older shops mean older electrical systems and not enough safe outlets for machine-operated equipment.
Temporary solutions to the outlet shortage make safety experts nervous.
“Improper use of extension cords is very, very common,” Miller says. “You see splitters, like you would on a Christmas tree with no breakers. People are using splitters instead of having a reasonable number of outlets. You will get overloads and burns because of that.”
Extension cords pose multiple problems, including a hazard for falls. Extension cords without circuit protection are fire hazards, especially when they leave the shop.
Godkin recommends inspecting cords for frays, properly grounding all plugs, avoiding overloading outlets and keeping breakers labeled and clear of obstructions.
A lack of overhead lighting is another issue in some shops. Dim parking lots are additional hazards because of early start or late finish times.
St. Charles installed motion-sensor lighting for the interior yard of its shop. The investment is worth the cost, Barber says. “If it prevents somebody from kicking a machine or car and going to the hospital or urgent care, it pays for itself immediately,” he says. “Little things like that have a big impact.”
Barber is fortunate because an assistant mechanic position is included in his budget. The assistant acts as a facilities manager. Checking and replacing fixtures is one the assistant’s jobs.
Traffic report
Yes, there are cases when outside opinions about its appearance can benefit a shop, according to Swartz.
“I would say keeping an older shop is absolutely more difficult, but it’s not impossible,” she says. “Sometimes it takes a fresh set of eyes to say, ‘What about moving a door?’ It’s not something you think about, but you’re like, ‘Wow, it just made this whole area safer.’”
Moving one door or altering a wall can minimize risk by redirecting employees past potential trouble spots. Velazquez says the staff at Walnut Creek constructed a small wall to direct traffic away from the shop and toward the office. The path is marked with hazard tape. Employees are also told to enter and exit the shop through the same entrance. Visitors are directed through the same spot.
“It makes it safer for everybody,” Velazquez says.
Clear paths also make it easier to reach safety equipment such as googles and spill kits.
“I don’t have to go across the shop, so there’s less potential for danger,” says Velazquez. “Everything is readily and easily accessible. When something happens, it will happen real quick.”
Blocked emergency exits are another traffic-related problem. Miller says creating single-aisle walkways make emergency exits easily accessible.
Get rid of it
An old or broken piece of equipment might have sentimental value. But unless it serves an immediate purpose, it shouldn’t be allowed to linger.
“Some of these people are like pack racks and there is stuff jammed everywhere,” Godkin says. “Organize a cleanup day. Bring in a dumpster and throw away all the crap you don’t need. It will create some valuable storage space.”
Barber has a two-year rule. If anybody on his staff hasn’t used a piece of equipment in two years, he gets rid of it.
Minimal works in Velazquez’s shop. When the floor is crammed, he looks for ways to store objects such as tires along walls.
After multiple tries, Velazquez believes he has found the right setup in Walnut Creek’s shop. He says frequent idea exchanges with green superintendent Scott Rettman turned a small shop into a spacious – and safe – workplace.
“People say my boss, Scott Rettman, and I are like two peas in a pod,” Velazquez says. “It takes a team. It just can’t be one person. It just can’t be the superintendent wanting to improve and the crew doesn’t care. It can’t be one guy on the crew or the technician and everybody else doesn’t care. Scott and I have the same goals and it helps out. It makes my job easier and his job easier.”
Guy Cipriano is GCI’s assistant editor.

Explore the June 2014 Issue
Check out more from this issue and find your next story to read.
Latest from Golf Course Industry
- Editor’s notebook: Green Start Academy 2024
- USGA focuses on inclusion, sustainability in 2024
- Greens with Envy 65: Carolina on our mind
- Five Iron Golf expands into Minnesota
- Global sports group 54 invests in Turfgrass
- Hawaii's Mauna Kea Golf Course announces reopening
- Georgia GCSA honors superintendent of the year
- Reel Turf Techs: Alex Tessman