Much has been written about the downturn in both the U.S. economy and also in the business of golf. Little has been written about remedies to solve the challenges that face golf now and in the future. In previous articles, I have mentioned creating efficiencies through the use of non-traditional scheduling for golf course operations. More specifically, I have referred to the “Ted Horton” method of scheduling, which allows for a core group of golf course workers at the opening hours that is dramatically reduced by 10 a.m. each day. Several core employees work from 10 a.m. to 2:30 p.m. and then an evening crew comes in after the last tee times to fulfill maintenance such as the mowing of rough and fairways. The “Ted Horton” method was used widely by ValleyCrest Golf Course Maintenance and recommended by me to a variety of golf courses over the years.
Non-traditional scheduling can take on a variety of time differentials. Some people are starting at 4 a.m. to stay ahead of play. Others are starting at 2:30 p.m. and working into the moonlight of night. No matter which alternative method is chosen, it will require change. It will be change for the golfers, neighbors, staff and management. Change does not come easy, but it should strongly be considered for golf facilities to prosper in the current economic environment.
Positive points
1. One of the most significant reasons to consider alternative scheduling is to produce the required work in the most efficient manner possible. At most golf courses, the maintenance and setup operate at a high level of efficiency as long as it stays ahead of play. Depending on staff starting times, efficiency can be significantly reduced as early as 8 a.m. but surely by 10 a.m. There is greater efficiency in the time frame that follows the last tee times of the day. Operating at peak efficiency times makes great sense.
2. When there is lesser interference with golfers, it provides greater customer satisfaction. It also can provide for a better pace of play when golfer/worker waiting time is eliminated. We all know how much time is wasted, in the middle of the day, with workers avoiding golfers in their normal routing and also doing routine maintenance practices such as mowing fairways and rough.
3. The number of acres mowed during peak play is less than during a similar time frame in non-peak play periods. It is logical that there is more wear and tear on machinery and greater fuel consumption. How many times must a starter be used to turn machinery on and off during peak play periods?
4. There are a variety of reasons for the use of part-time and seasonal workers in golf course operations. With the use of non-traditional scheduling, it will allow for the use of a core team, but also a variety of part-time positions. Some golf courses currently employ part-timers to do specific jobs such as fairway mowing, ball mark repair and spraying. All of this and more can be done in non-peak hours by part-time employees who would not require a full set of benefits which has hampered payroll costs for many operations.
5. By using workers in non-peak hours, it will logically reduce the number of man-hours required to do the work outlined in the maintenance standards of the golf facility. This will be huge as the minimum wage is set to rise in the years ahead.
Challenges
1. The primary challenge to non-traditional scheduling is getting people to think outside of the box. Most superintendents have always worked a typical 6 a.m. until 2:30 p.m. schedule because that is what they learned as interns. Change is difficult. Rather than making a dramatic change, it may be best to start off with small steps in a transition.
2. For anyone to say it has never been done before is not a fair statement. Superintendents are an ingenious group and tend to find solutions to the challenges in front of them.
Change does not come easy, but it should strongly be considered for golf facilities to prosper in the current economic environment.”
3. Not every labor market will be easy to find staff who can work in non-traditional hours. But I think people will be surprised at the number of people looking for part-time work to supplement another part-time job or even work to supplement their 40-hour work weeks.
4. When implementing different schedules, I have found that often the superintendent opposes the concept thinking he or she would have to work from 6 a.m. until 7 p.m. To the contrary, management is a team effort. Shifts can be split by the superintendent and assistant or even with a foreman. Take a look around the golf facility and you will see other departments that are open from dawn through dark using multiple shifts with multiple supervisors.
5. One of the most difficult positions to fill on a golf course is equipment technician. Major repairs can be done by this skilled individual during normal hours. Any other repairs will need to be done in the field and may require some cross training. Some of the older generation may remember adjusting gang mowers in the field by the operators.
6. Superintendents will need to evaluate the efficiency of standard equipment inventory but may actually find a need for more equipment to counterbalance the highest level of efficiency.
7. Noise ordinances are perhaps one of the biggest obstacles to using non-traditional scheduling. Municipalities have noise ordinances for many types of equipment. Be sure to check on the laws and regulations in your city. Some cities have a different regulation for blowers than for mowers. Some cities have both morning and evening noise regulations that might preclude golf courses from working too early or too late. Double check the regulations for weekends and holidays as they are often more restrictive than during the week. Obviously this presents a challenge as golf courses are busiest on those days.
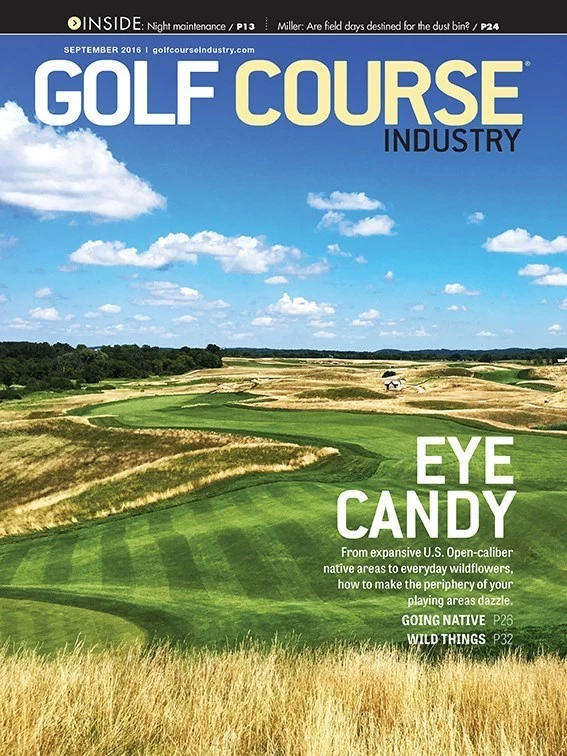
Explore the September 2016 Issue
Check out more from this issue and find your next story to read.
Latest from Golf Course Industry
- Editor’s notebook: Green Start Academy 2024
- USGA focuses on inclusion, sustainability in 2024
- Greens with Envy 65: Carolina on our mind
- Five Iron Golf expands into Minnesota
- Global sports group 54 invests in Turfgrass
- Hawaii's Mauna Kea Golf Course announces reopening
- Georgia GCSA honors superintendent of the year
- Reel Turf Techs: Alex Tessman