We’ve come a long way since the days of wooden and hand-made brick pipe from the early 1900s. If you’ve never seen wooden pipe, the construction is ingenious. There’s an angled wooden lath cut to form a circle. Surrounding this wooden circle is a continuous wrap of aluminum wire that not only holds the structure together but also keeps the swelling of the wood in check. Next, there was clay tile, copper, galvanized, steel, asbestos cement (AC), ductile iron and polyvinyl chloride (PVC) pipe. AC pipe posed the biggest environmental and health threats, and to expose it now requires a white-suited and masked team of EPA specialists.
The PVC pipe evolution began in the 1940s but wasn’t used for irrigation until the mid-1960s when pressurized PVC pipe had been developed. Skeptics at the time criticized the introduction of “plastic” pipe and claimed it could not possibly outperform steel or AC pipe. The early PVC pipe didn’t have strict regulations regarding strength, pressure rating, diameter or even manufacturing. However, once the familiar governing bodies of the American Water Works Association, ASTM International (originally known as the American Society for Testing and Materials) and others got involved, standards were created for PVC pipe manufacturers.
Golf course application of PVC pipe
PVC pipe has been used almost exclusively in the golf course industry since 1970. Golf course irrigation designers, golf course superintendents and installing contractors all have to been aware of the issues involved with PVC pipe and fittings. These include:
• The class of PVC pipe used (CL 160 vs. CL 200 vs.
C 900);
• Adequate thrust blocks (or pipe joint restraints) at all fitting and valve locations and for changes in direction;
• Deflection (bending) limits of PVC pipe (maximum of 5 percent);
• Bedding of pipe and backfill material, particularly in rocky soil;
• In cooler climates, preventing the freezing of any water in the pipe (draining and blowing down the irrigation systems with air);
• For smaller diameter pipe (3 inches and smaller), gluing the pipe properly with the correct primer, glue and method; and
• The anticipated life expectancy of underground, pressurized PVC pipe and fittings.
The development of HDPE pipe
The newest pipe is high density polyethylene (HDPE). It came about as irrigation industry experts tried to improve the flexibility and durability of underground pipe. In the 1930s, European countries began using it for utilities. The United States began using it for gas and water utility lines in the 1950s. As the popularity of HDPE pipe increased, so did the technological advances. Manufacturers developed more fittings and improved the pipe manufacturing process and regulatory agencies developed standards for the industry.
In the late 1980s, HDPE pipe was introduced for golf applications in select areas of the United States.
In 1988, Jim Kirchdorfer of ISCO Industries is said to have been the first in the U.S. to use HDPE pipe entirely on a golf course at Quail Chase, a Kentucky golf course he owned. At that time he had to manufacture the fittings for his project because they were not yet made by any other company. Kirchdorfer introduced HDPE pipe to golf course irrigation systems in the late 1970s using HDPE on the tough applications such as stream crossings, exposed pipe, intake pipe and poor soil conditions.
During this early period of HDPE pipe in golf irrigation, from the late 1980s until the mid-1990s, the selection of fittings for the pipe was limited. Manufacturers would make the fittings needed for each individual project. In the late 1990s, manufacturers finally began making the fittings that were most commonly used for golf irrigation. This was a big shot in the arm for the use of HDPE pipe in the golf irrigation industry.
HDPE pipe vs. PVC pipe
Connecting pipe to pipe or pipe to fittings, such as HDPE tees, is done with a butt-fuse connection. For this method with large diameter pipe (4 inches and above), two lengths of pipe are placed into a specialized fusion machine (most commonly a McElroy Tracstar).
The operator enters the appropriate data into the fusion machine (for example, 8-inch pipe in 60-degree weather conditions). The edges of the two ends to be fused are shaved, a heat plate heats the ends for the correct amount of time, and the ends are then placed together, essentially fusing them together. A “bead” is created around the outside and inside of the pipe where the fusion took place, and this bead should be the same thickness throughout.
After cooling time, the fused pipe is removed and two new pieces are fused in the same manner. The same process is used for fittings such as tees. Some fusion machines maintain a data logger for every fusion process, which can later be printed for reference. For smaller diameter pipe, 3 inches and below, the process is the same, but it’s done by hand with a smaller machine (most commonly a McElroy Pitbull).
If we use our 8-inch pipe and 60-degree weather conditions as an example, 30 to 40 minutes are required for the entire heating and cooling fusion process. The main variables affecting the time are the wall thickness of the pipe and the temperature needed to fuse the pipe correctly.
A qualified contractor can fuse approximately 1,000 feet of 8-inch DR 11, PE4710 resin pipe per day. Butt-fusing takes place above ground, and while it’s being done, others can be opening the trenches where the pipe will be placed. Contractors usually have one work area where butt-fusing takes place, and the fused pipe is then dragged to where it’s needed.
Connecting 2-inch lateral pipe to mainline pipe requires an electro-fused saddle. An electro-fused HDPE saddle can be ordered for all ranges of pipe size, with a threaded outlet of ¾-inch to 2-inches (or larger with fused or threaded outlet). The underside of the saddle contains electrical wire incorporated into the saddle. On the top are two electrical prongs where the electro-fusion machine is attached. During the electro-fusion process, the electrical wire within the underside of the saddle heats the surface of the saddle and fuses it to the pipe. Once again, for each fusion process the appropriate data is entered into the machine. After the saddle has been fused to the top of the pipe, the contractor can drill a hole through the saddle and into the HDPE pipe, where a cast iron elbow is threaded into the saddle for installing a 2-inch lateral gate valve. The contractor also can use a fully fused HDPE elbow with a fused valve. There are numerous and proven methods to make the connection to the electro-fused saddle.
Sprinklers are connected to 2-inch HDPE pipe rather easily. Contractors have found that using 250 feet to 2,000 feet rolls of pipe is the easiest and most economical method. The pipe is run through a “line tamer” machine to straighten it to make it easier to handle and install. Where the sprinklers are actually connected to the pipe, the Lasco Co. has manufactured a mechanical saddle specifically made for this application.
We have found the process of connecting and installing HDPE pipe to actually be quicker than PVC pipe installation. With large diameter HDPE pipe installation, no thrust blocks are needed and no special bedding is needed for the pipe trench due to the wall thickness of the pipe and fittings. For 2-inch lateral pipe, there is no gluing time involved for connecting PVC pipe every 20 feet (HDPE comes in a minimum of 40-feet length up to 2,000-feet coils) and no fittings are needed except for the saddle at the sprinkler swing joint locations.
Technical advantages of HDPE pipe
The methods briefly described above are used to install an HDPE golf irrigation system. Not included in those descriptions are the technical advantages in using HDPE pipe and fittings for golf irrigation applications. They include:
Pipe fatigue factor – When water surges take place within PVC pipe as sprinkler cycles turn on and off, the PVC pipe and fittings expand and contract ever so slightly. Due to the chemical composition of PVC, the material is weakened over time. With HDPE pipe, however, it contracts to its original size without weakening. For this reason, AWWA “derates” PVC pipe, stating that over time, the pressure the pipe can handle is reduced from its originally manufactured pressure rating. There is no such derating for HDPE pipe. The lifespan of PVC pipe is 25 to 30 years; HDPE pipe’s is more than 50 years.
Flexibility – According to manufacturers’ recommendations, larger diameter PVC pipe cannot be deflected (bent) more than 5 degrees. HDPE pipe has a bend radius of 25 times the diameter of the pipe with no detrimental effect to the pipe. This eliminates many of the fittings and thrust blocks required for PVC pipe installation, which in turn, reduces the number of potential main line breaks.
Leakage – Even the best installed PVC irrigation systems experience leakage at fitting and valve locations. With the butt-fusion technique for HDPE fittings and valves, the pipe and fittings become one monolithic unit, which eliminates leaky joints. This saves water and electrical costs as it eliminates pump cycling to maintain pressurization. Environmentally, as more courses choose to use effluent water for irrigation, less leakage means less worry about environmental breaches.
Freeze breaks – In colder climates, golf course personnel must drain as much water as possible from PVC pipe systems before winter to avoid the freezing and breaking of the irrigation system. HDPE pipe can be frozen solid and not break, although draining the irrigation system before winter is still recommended. Worry about breakage is eliminated with an HDPE system.
Going green – Most professionals in the golf industry are concerned about environmental issues – from the materials used to build the golf course to the inputs used to maintain them. The EPA has expressed concerns about PVC at various seminars and would like to see it disappear from the irrigation industry. HDPE pipe is 100 percent recyclable. GCI
Rick Robbins is president of RRI, Inc., which began designing golf course irrigation systems in 1981 and with HDPE in 1997. He can be reached at rrigolf@comcast.net.
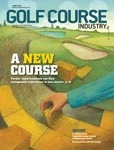
Explore the June 2009 Issue
Check out more from this issue and find your next story to read.
Latest from Golf Course Industry
- Foley Company promotes Tyler Barrett
- Beyond the Page 64: To infinity and beyond
- Plant Fitness expands into Asia Pacific markets
- Ace of a decision
- Idaho course joins Concert Golf portfolio
- Central Turf & Irrigation Supply celebrates 35 years in the industry
- Musser Turfgrass Foundation honors University of Georgia researcher
- Riviera CC donates $1 million for fire relief