One common question I hear is whether to use joint restraints or thrust blocks. On the surface, a joint restraint system appears to be a premium. However, if you survey site soils and contractor installation capabilities, material costs become a smaller part of the installation price.
Contractors generally look at the total cost of installation, not just the price of material. With a thrust block system, items that won’t show up on a bill of material are usually the incidentals like concrete and the labor needed to install the thrust block. Those costs can vary significantly. Remember, when truly considering the total cost of installation, the aforementioned "premium" for a joint restraint system in some cases isn’t as costly as it seems. Less time and labor may be required for an effective installation that’s immediately testable and operational.
When working through your budget, make sure you gather sufficient site information, investigate the marketplace and consider the following:
Thrust block cons:
1. A properly designed thrust block involves much more than dumping a load of concrete behind a bend. The design involves consideration of undisturbed soil, soil-bearing strength, test pressure, pipe size, fitting configuration and trench depth to determine the actual bearing area of the thrust block.
2. The bearing strength of the soil is expressed in pounds-per-square-foot. Therefore, the area behind the thrust block must engage enough soil area to resist the resultant thrust force at a particular change in direction.
3. Tremendous thrust forces are involved: 27,000 pounds of force can be exerted by some fittings at 150 psi. Such forces created by pressure surges could potentially move a thrust block.
4. Thrust blocks, typically dimensioned or engineered on a plan, are difficult to quantify during inspection in accordance with the plan due to various conditions that apply to every thrust block.
Joint restraint pros:
1. A properly designed, restrained pipeline uses the bearing strength and frictional resistance of the soil to turn the pipeline into a thrust block.
2. Parameters are pipe size and type, test pressure, fitting type, trench type, depth of bury, soil type and safety factors.
3. Using joint restraints allows the pipeline to be restrained, buried and tested without waiting for concrete to cure, eliminating the need to leave trenches open for long periods. Water can be turned on as soon as the restraint is set.
4. Joint restraints have been successfully used for more than 25 years in water works, municipality and utility systems. The force of water accelerating through irrigation piping can take its toll on an irrigation system. Even at controlled velocities, surge pressures pounding against fittings day in and day out can destroy faulty fortification and render your system unreliable at best.
Two common problems are related to pipe fittings and wire splices. When considering thrust block vs. joint restraint within your budget, on average joint restraints cost 5 percent more in materials than thrust blocks. But weigh in the total cost and the potential for error before you decide. GCI
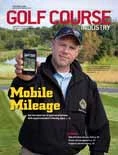
Explore the October 2009 Issue
Check out more from this issue and find your next story to read.
Latest from Golf Course Industry
- Advanced Turf Solutions’ Scott Lund expands role
- South Carolina’s Tidewater Golf Club completes renovation project
- SePRO to host webinar on plant growth regulators
- Turfco introduces riding applicator
- From the publisher’s pen: The golf guilt trip
- Bob Farren lands Carolinas GCSA highest honor
- Architect Brian Curley breaks ground on new First Tee venue
- Turfco unveils new fairway topdresser and material handler