Irrigation systems are one of a golf course’s most expensive assets. For most superintendents, shutting down this system is a rite of fall to make sure there are no headaches or surprises waiting when the system is fired up again in the spring.
Some golf course managers outsource this tedious task, but to ensure everything goes smoothly and to save money, many perform irrigation blowouts in-house.
"As superintendents, we have more of an interest in it because it’s such an expensive system," says Chris Lecour, general manager and course superintendent at The Raven Golf Club at Lora Bay in Collingwood, Ontario, co-host of the 2009 Ford Wayne Gretzky Classic. "It’s not something I would outsource and expect to get the same results for less money than it costs us to complete it ourselves."
Irrigation blowouts are pretty straightforward, Lecour says. He estimates there are about 1,100 irrigation heads and miles and miles of wire at The Raven. He and his crew like to take their time when winterizing their system to make sure it’s blown out properly and to their satisfaction.
"If we don’t do it right in the fall, we will pay for it in the spring," he says. "Not taking the time to blow it out properly only means a huge headache, a big mess and wasted money in the spring when there are other things I should be worrying about."
The blowout process at The Raven takes between three and four days with one to two employees working 11 to 12 hours per day. The course rents a compressor, which costs around $1,500 Canadian; fuel is roughly an extra $650. Lecour is fortunate both his first and second assistants were around when the course was built, so they have a good sense of where all the pipes are located.
The Raven typically closes the last Sunday in October and the compressor arrives that week. "We make sure we do the blowout when there are no golfers on the course," he says. "Usually, we are lucky to have no snow when we start, but inevitably every year it snows while we are doing it. We run through the entire system three to four times during those four days and some low-lying sections of the course we do even more than that.
"We are very thorough," he adds. "We are confident when it’s done that it was done well."
The Raven’s irrigation system is controlled by satellites, so it’s easy to set up a program to control the blow out of the heads on each hole.
"Each head will run for two to three minutes the first time around," he explains. "It’s not like you have to be watching it the whole time. We run 16 heads at two minutes; it will take two hours to run through them. We keep going forward throughout the golf course and turn on certain holes at a time without having to be there to watch them. Then, we come back two or three times to fine-tune the process.
"Depending on the compressor, we can only turn on a certain number of heads per time," he continues. "Once we know we’ve got most of the water out of the system, we go through and turn on each head; then, we watch it to make sure it’s blowing clean before we move on to the next head. We do that at least two times, and three to four in low-lying areas."
Jack Mackenzie, superintendent at North Oaks Golf Club in North Oaks, Minn., says bigger is better when it comes to irrigation blowouts.
"That is as long as you have the bodies to manage the quick couplers, valves and stations," he says. "It’s also critical that the compressor has a regulator to limit the pressure from going over 100 psi."
Mackenzie and his crew use a 1,300 cubic-feet-per-minute (CFM) unit, which can blow out the entire system in less than six hours.
"Three of my staff and I start at the pump house where the compressor is attached and work across the course finishing at the far reaches," he says. "One individual blows the quick couplers and the others blow from the satellites. The pressure rarely exceeds 60 psi and we do a pretty good job with only a once over. We blow until there is only vapor coming from the heads. The only time we have had any breaks in the spring is if somebody overlooks a valve or head."
David Brandenburg, golf course manager at Rolling Meadows Golf Course in Fond du Lac, Wis., also prefers to have his crew perform the irrigation blowout.
"We rent a 750 CFM compressor for two days to blow out our 27-hole course," he says. "A day before, we will water heavy if needed, and open up some pond drains and low heads or quick couplers to remove as much water as possible. Our pump station is in the middle of the course almost perfectly, so we hook the compressor up to the pump house and leave three of our lowest quick couplers open to get rid of some water.
"When they are clear of water and the pressure is over 50, we start running individual heads working uphill of the pump house followed by downhill of the pump house."
This process allows Brandenburg’s crew to get most of the water out the first time. It also allows the system to settle down overnight before starting again the next morning. The irrigation blowout at Rolling Meadows takes three employees – one to stay near the pump house to watch the pressure and winterize the pump house and two to run the heads.
Brandenburg says the goal is 60 psi since 49 is too low to turn some heads on and 75 to 80 will blow the heads right out of the ground. They usually run the compressor for five hours the first day, four hours the next morning and two hours on the third and final time through.
"After the second blowout, where we take each head down to a mist, we pressure down again and go through a third and final time," he says. "I think a contractor would have a difficult time running heads once a year without getting golfers wet or surprising the heck out of them with the screaming noise the heads can make under air pressure. For a new system that they installed recently, or a course that is closed to play, a contractor may be able to do it, but even my own staff has a hard time figuring out where all the heads are located."
To the best of Don Singlehurst’s knowledge, all the courses in the Victoria-area perform irrigation blowouts themselves since outsourcing of this service is not available.
Singlehurst, the superintendent at Royal Colwood Golf Club in Victoria, British Columbia, says the two main reasons his facility does the blowout in-house is the crew knows the layout of the system and they’ve been able to achieve the desired results with no problems to date.
"Unfortunately, if problems do occur, they would not be diagnosed until the spring," he says. "I often wonder if these outsourced companies are responsible for any damage that occurs during a blowout and would they come back in the spring?"
Royal Colwood coordinates its annual blowout with several other golf courses to reduce the cost of the compressor and make sure they don’t all compete for the same dates. Singlehurst requests delivery of the compressor the day before the blowout. Overall, the cost is approximately $700 for the compressor, which includes delivery and pickup, plus in-house labor (approximately $500); diesel fuel adds an additional $175.
Having the compressor onsite one day early allows the mechanic to make sure the unit is functioning properly, Singlehurst says.
"We also make sure all the fittings and hoses are available so there are no surprises first thing in the morning," he says. "And, on the day of the blowout, our mechanic arrives early to start things up. Once we have adequate pressure, three employees go out and manually run the heads in a specified route so we don’t chase the water around."
Generally, it takes Singlehurst and his crew approximately six to eight hours to achieve Royal Colwood’s desired goal of no visible water moving through the system. Singlehurst says he’s had no problems to date.
"Victoria weather can be quite mild compared to other parts of Canada, so the chance of severe damage through freezing and heaving is not very common," he says. GCI
McPherson is a freelance writer based in Toronto.
Get curated news on YOUR industry.
Enter your email to receive our newsletters.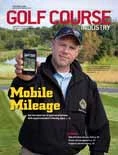
Explore the October 2009 Issue
Check out more from this issue and find your next story to read.
Latest from Golf Course Industry
- Advanced Turf Solutions’ Scott Lund expands role
- South Carolina’s Tidewater Golf Club completes renovation project
- SePRO to host webinar on plant growth regulators
- Turfco introduces riding applicator
- From the publisher’s pen: The golf guilt trip
- Bob Farren lands Carolinas GCSA highest honor
- Architect Brian Curley breaks ground on new First Tee venue
- Turfco unveils new fairway topdresser and material handler