The equipment inventory at Blackhawk Country Club in Madison, Wis., is extensive, but a couple of items are certain to turn the heads of any superintendent or technician. There’s a pair of Ford tractors that are more than 25 years old and a couple of Jacobsen Greens King triplex mowers nearing 14 years of age with between 5,000 and 10,000 hours of operation.
These pieces of equipment are still around not because Blackhawk is stingy with its budget or that superintendent Monroe Miller refuses to embrace new technology, but because these machines continue to perform because they’ve been maintained meticulously.
“We keep some pieces of equipment beyond what would be described as their normal useful life,” says Miller, who has been Blackhawk’s superintendent for 32 years. “I didn’t trade the Greens Kings because they still have some useful life. We bored out the cylinders and installed oversized rings. And we bought a new engine for one mower because we felt the rest of the machine had enough value that we could justify the $1,300 expense.”
|
But the older equipment isn’t expected to perform like its newer counterparts. Life is easier for these aging mowers because they aren’t used in applications in which cutting units are lifted and dropped frequently. They mow par-3 fairways or make long runs on 420 yards of a par-5 fairway.
“We still mow fairways with a 1992 Toro Reelmaster 223-D, and it gives a beautiful cut,” Miller says. “The cutting units on new mowers are almost exactly the same as the old ones. Of course, new machines are more comfortable and quiet, but all we’re doing is mowing grass. Side by side, I can’t tell the difference in the cut between the two mowers, and that’s the truth. Old mowers suit me just fine if they perform. However, at some point, reliability becomes a factor, and they must be replaced.”
But for any golf course maintenance staff, a quality equipment maintenance program will keep pieces working better and lasting longer.
Quality maintenance
The reason for the enviable performance of the older equipment is the quality of Blackhawk’s maintenance program.
|
“Good maintenance is so simple – honestly,” Miller says. “Our equipment manager, David Noltner, has been here 31 years. He comes to work before the rest of the staff and makes all the reel-to-bedknife adjustments. He checks fluid levels everyday and fuels each machine to make sure gas and diesel get in the right tanks. No one else is allowed to touch the equipment.”
The basics of Blackhawk Country Club’s maintenance program include the following.
1. By the book. Believe it or not, Noltner reads and rereads the owner’s manuals for each machine.
“Everything is done by the book, and we don’t stretch intervals,” he says.
The shop uses only genuine original equipment manufacturer parts; and detailed, accurate records are a cornerstone of the maintenance program.
2. Good work environment. The shop is comfortable and well lit, and Noltner has all the high-quality tools he needs. A peek inside his toolbox reveals organization: Sockets in the socket drawer are arranged according to size, and wrenches in the wrench drawer are lined up from smallest to largest. There’s also an adequate-sized lift and, most importantly, Noltner has the time to do the job right.
It’s also significant to note that Noltner views himself as a professional and is respected by the club. On his 25th anniversary, he was invited to the board meeting, acknowledged for his dedicated service and given a generous gift.
3. High-quality grinders are critical. Blackhawk uses automatic reel and bedknife spin grinders. To sharpen the reel, the operator sets the reel on the grinder, makes the necessary adjustments, closes the door and turns on the machine. When grinding is complete, the machine shuts off itself.
“Guests come to Blackhawk because of our greens, so the reels on those mowers get the primary emphasis,” Miller says. “Greens mowers are sharpened as required.”
|
After mowing 10 greens, reels are backlapped. Then, at a point determined by the degree of sharpness, the reel goes back to the grinder.
“Only David makes reel adjustments, and he makes them every time a mower goes out,” Miller says. “The adjustment may be slight, but the mower is always cutting at its peak efficiency. When David thinks a reel is a little tight, it gets backlapped. After that, they’re put on the grinder, and with our equipment, it’s easy to do.”
4. Be tough on operators.“If I see anyone abusing equipment, they won’t run it anymore,” Miller says. “I recently told someone that if I saw him driving a utility vehicle too fast again, he’d walk to cut cups.”
5. Keep it clean. Blackhawk has a pressure washer and a large hot-water heater to use for cleaning equipment. The staff also uses high-grade automotive wax and large buffers, making every piece of equipment look like new.
“If an operator thinks a machine looks new, he treats it differently,” Miller says. “If it looks bad, he beats it up.”
The equipment is so well taken care of, people often think it’s new. An equipment-dealer representative visited the shop this summer and noticed the Ford tractors.
“He said things must be good at Blackhawk because we’ve got new tractors,” Miller says.
One of the club’s best mechanics and operators, Omar Zaldivar, could have a career detailing cars, according to Miller.
“When our mowers come out in spring, we hate to get them dirty because they look so good,” he says. “And one time, this actually worked to our disadvantage. A new green committee member made the comment that we’re spending way too much money on equipment because we have so much new machinery. These stories may be amusing, but the simple fact is that properly maintained equipment works better and lasts longer.”
6. Productive off-season. By Nov. 1, the five year-round members of the maintenance staff are pushing to get equipment ready for spring, and part of that preparation is visual inspections, which are thorough.
“We look at fittings, fasteners and other components that we can’t see if we don’t take off the sheet metal,” Miller says.
7. Talk to distributors. Miller and Noltner talk to distributors regularly and seek advice from their service departments.
“They tell us what we should be doing or give us a heads up about parts that may need to be replaced,” Miller says.
8. Budget correctly. And Blackhawk doesn’t fall behind on equipment acquisition either.
“We have the traditional five-year capital acquisition plan, but it has to be flexible,” Miller says.
|
Think like superintendents
Quality maintenance programs are improved even more when technicians understand – from a superintendent’s point of view – what it takes to deliver top-quality course conditions. Steve Jordan, equipment manager at Winged Foot Golf Club in Mamaroneck, N.Y., is serious about his responsibility to know the daily and long-term course expectations of superintendent Eric Greytok.
“I see a lot of technicians who don’t make the time to go out on the golf course and really look at it,” Jordan says. “I sometimes consult for other courses, and walking one hole from the tee box to the green reveals a lot about the facility’s maintenance program. If the tee box is shaggy, I know that tee and approach mower maintenance isn’t a priority. If I walk up to a green surround and it’s fuzzy-white and hazy and the grass is ripped, obviously rotary mowers aren’t a priority either. The same is true for roughs. If the height of cut is uneven, those mowers don’t receive a lot of attention. I’ll even go up to the base of trees. If the grass is ripped, that course probably isn’t using the right trimmer string.”
Jordan also gets involved helping manage cultural practices. For example, Greytok wasn’t satisfied with the results of greens aerification, and the two brainstormed about an equipment solution.
“Three years ago, we were using 3/8-inch quad tines, but Eric still wanted to eliminate more thatch,” Jordan says. “We went into the shop, drilled out the blocks in the aerators and put in 1/2-inch tines. The affected surface area increased from 7 percent to 13 percent.”
Lou Bueti, head technician at The Golf Club of Purchase (N.Y.), makes sure he anticipates his superintendent’s needs as well.
“Many things on a golf course happen repetitively,” Bueti says. “For example, we all know the aeration schedule, so it’s my job to make sure we have bedknives in stock and the tines and machines are ready. If it’s rained for three days, I know we’re going to raise mowing heights. I try to be a day ahead of what he’s thinking, and that means I have to be knowledgeable about what it takes to maintain the course conditions we want. A superintendent shouldn’t have to worry about whether or not the technician knows what to do.”
Identify equipment
Identifying equipment is another aspect of a quality maintenance program. A system that has worked well for Jordan and Bueti is marking equipment. Walk-behind greens mowers used on tees receive a different color-coded tag than walk-behind mowers used on greens. In some cases, mowers are marked for individual operators.
|
“To some operators, all mowers look the same, so it’s important that we have a system where everyone knows where each piece of equipment is going,” Bueti says. “And, if an operator is on a particular mower all the time, he’s more likely to notice when something isn’t performing right.”
“If I go to a golf course and see a big hack on a tee box, I know someone grabbed a greens mower by mistake,” Jordan adds. “This happens more frequently than superintendents would like to think, and tagging equipment is an easy way to solve the problem.”
Quality of cut
With all that goes into a quality maintenance program, the quality of cut, which is the end result, is the main driver behind any program, whether it’s at Blackhawk, Winged Foot or The Golf Club at Purchase.
Jordan started repairing bikes when he was 14 years old and then moved on to cars. In 1995, he took a job on the maintenance staff at a golf course in the Pocono Mountains in upstate New York. When the mechanic there left, the superintendent told Jordan he worked well with his hands, and offered him the job.
“I learned immediately the impact a good technician can have on a golf course,” Jordan says. “Within one season, we went from pretty good to awesome. There’s no excuse not to check equipment daily and keep mowers sharp.”
This philosophy applies to any course, regardless of the size of the maintenance budget, because reels, blades and bedknives must be sharp, according to Jordan.
“There’s no set standard in the industry for how to do this, but if it doesn’t cut, pull it out and grind it,” he says. “If you don’t have grinders, backlap. Just find a way to do it – no excuses.
When I came to Winged Foot, Paul Latshaw Sr. told me that we’re in the business to mow, and that’s where our priorities must be,” he adds. “If we’ve got a good daily maintenance program, it will show on the golf course.” GCN
David Wolff is a freelance writer based in Watertown, Wis. He can be reached at dgwolff@charter.net.
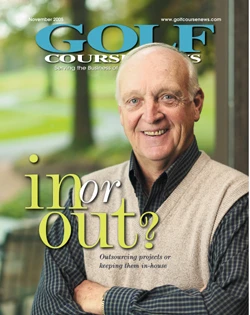
Explore the November 2004 Issue
Check out more from this issue and find your next story to read.
Latest from Golf Course Industry
- Talking Turf Weeds 13: Talking seasonal change with Heidi Burgess and Paul Marquardt
- Beyond the Page 65: New faces on the back page
- From the publisher’s pen: New? No way!
- Indiana course upgrades range with synthetic ‘bunkers’
- Monterey Peninsula CC Shore Course renovation almost finished
- KemperSports and Touchstone Golf announce partnership
- PBI-Gordon Company hires marketing manager Jared Hoyle
- Mountain Sky Guest Ranch announces bunker enhancement project