Project scope and expertise help determine whether course renovations are done in-house or by an outside contractor.
When deciding between calling a contractor to undertake a construction or renovation project or taking on the project in-house, golf course superintendents must weigh the pros and cons of each. Whether it’s planting shrubs, adding onto the clubhouse or completely rebuilding greens, myriad factors must be taken into account before making the decision.
|
Frank Dobie, superintendent at The Sharon Golf Club in Sharon Center, Ohio, says he doesn’t think he could take a stand for or against doing work in-house. According to him, it depends on the superintendent and whether he or she has the time and money it takes to do the work.
Dobie started working at The Sharon Golf Club in the mid-1960s when course was being built. He was involved in every aspect of construction – from building greens to installing the irrigation system.
“We’ve done just about everything there is to do in-house,” he says.
Gary Grigg, CGCS, MG, spent 32 years as a superintendent and now owns Grigg Brothers Specialty Fertilizers in Albion, Idaho. As a long-time member of the Golf Course Superintendents Association of America and past president (1995-96), he’s seen most situations that can arise before and during construction or renovation.
Grigg says superintendents should look at the work that needs to be done. If it’s rebuilding a tee or regrassing a green, an experienced superintendent shouldn’t find those tasks too difficult. If it’s something like rebuilding a green, however, one should consider calling a professional.
“Superintendents are doing minor projects all the time,” he says. “It’s an ongoing deal … part of the job. For major renovation though, they should bring in a qualified crew. It puts the responsibility on a licensed contractor.
“Unless I thought it was going to save a lot of money, I’d call a contractor,” he adds.
Dobie suggests taking a good, hard look at a project before beginning. Following that evaluation, he suggests hiring the best professional available, whether that be someone in-house or a contractor. However, if the project fits within a superintendent’s capabilities, he might want to do the work in-house.
“Cost savings is a reason, but not the No. 1 reason,” he says. “We want it done exactly how we want it done. When you turn it over to a contractor, you’re going to get their best efforts … or maybe not.”
Two aspects that drive the decision to perform work in-house are money and experience, according to Bud White, senior agronomist with the U.S. Golf Association, mid-continent region.
“In my experience throughout the years, in-house construction is driven by two things: The club makes the superintendent do it in-house to save money, and the construction or renovation experience of the superintendent,” he says. “The experience of the superintendent is a big thing.”
When making a choice, White says management might overlook whether there is anyone on the crew who knows how to operate the equipment. Someone with experience might do a better job in an hour than an inexperienced worker can do in five hours with rented equipment.
“Which is more expensive?” he asks.
Dobie epitomizes the superintendent who is abundantly qualified and experienced to do the work in-house. When building The Sharon Golf Club, his team didn’t install bunkers along with initial construction – they built only the cavities and grassed them in with the rest of the course. Dobie wanted to keep the sand clean and not contaminate it with soil. When the time came to add sand, the course bought a backhoe and trained an operator – who still works at the club. With construction in his hands, Dobie used plastic liner instead of fabric, which is the industry norm. This had never been done before, according to Dobie.
|
“We had control over how much we did and when we did it,” he says.
In addition to the bunkers, Dobie and his crew rebuilt the green on the first hole to repair a drainage problem. However, they went one big step further by designing and building an extra hole to be used while other holes on the course were being worked on and taken out of play. The X hole fits into the routing between the 10th and 11th holes. All the work was done in-house, with the exception of using an excavator to dig a large pond. Fill material from the pond was used to build up the green and tee.
So, would Dobie suggest other superintendents do this type of work in-house?
“Yes, I would,” he says. “But I recommend doing it slowly.”
Dobie recommends starting on smaller projects before tackling anything larger. And before beginning a project – large or small – he recommends superintendents establish the kind of job they want to do and then train workers so they are prepared when the project is ready to be started. Dobie trained his crew on smaller projects.
“We didn’t bite off more than we could chew,” he says.
Like the bunker construction, the X hole project took a number of years to complete. Dobie designed the bunkers, tees and the X hole himself. He says he takes many ideas he sees from golf course architects such as Michael Hurdzan, Ph.D., or Arthur Hills and implements them on his course.
“It wasn’t foreign to me, and it didn’t scare me,” he says.
Because of ongoing construction, renovation or normal upkeep, the X hole was Dobie’s way of keeping the membership happy.
“There’s a political angle to consider,” he says. “How long are we going to have things torn up? That’s why we built the X hole. It’s like a spare tire.”
Also with the membership in mind, Dobie began building forward tees 20 years ago. The course had white tees for general play as well as championship tees, but Dobie realized some of the senior players were having difficulty playing from some of the tees. He asked the members for their input before determining which forward tees were needed and is still adding them to this day.
In-house construction |
Pros |
“The biggest thing, if you use your own crew to do the work, is that whatever the crew was supposed to be doing will suffer,” he says.
In addition to taking away from other areas of the course, Grigg says many crew members aren’t qualified to do the work needed when construction is handled in-house. Beyond that, superintendents and management should take into consideration the superintendent’s qualifications.
Lastly, Grigg asks, “What if the members don’t like it?”
He says he’s seen many superintendents get fired because of failed projects.
“I was never afraid to take responsibility for that kind of stuff,” he says. “But I’ve seen more jobs lost because of reconstruction than anything.”
Grigg says getting fired isn’t the worst thing that can happen if a superintendent decides to do the work in-house. The best-case scenario is getting the job done the way a superintendent wants it – on time and on budget. The worst-case scenario is death, according to Grigg. In one such case, he knows of a crew member who was killed when a backhoe ran him over. The club was held responsible.
Before making a decision between a contractor and in-house work, White suggests weighing all aspects of the project and making sure all aspects are conveyed when presenting the project to management.
“I encourage them to push for a contractor,” he says. “It relieves them of responsibility.”
White says the superintendent can still manage the job without being solely responsible for the outcome.
“Hire somebody who has good golf course renovation experience,” he says. “In the long run, the difference in cost isn’t as dramatic when you weigh everything – the quality of work and the time frame to do it in.”
Dobie says time should be a main concern when evaluating projects. Aside from building an entire course, no project is too large for Dobie and his crew.
“If time is a constraint and there’s a lot to be done, then an outside contractor is best,” he says.
It all comes down to talking everything through with management, according to Grigg. If all the information is presented, then hiring a contractor or keeping work in-house will be a team effort.
“Sit down with the immediate supervisor and thoroughly go through all the pros and cons,” he says. “Do not make the decision by yourself. Make sure to communicate.” GCN
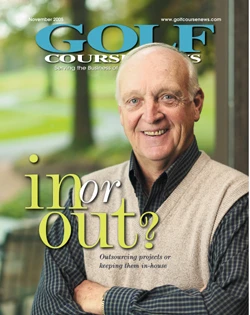
Explore the November 2005 Issue
Check out more from this issue and find your next story to read.
Latest from Golf Course Industry
- Editor’s notebook: Green Start Academy 2024
- USGA focuses on inclusion, sustainability in 2024
- Greens with Envy 65: Carolina on our mind
- Five Iron Golf expands into Minnesota
- Global sports group 54 invests in Turfgrass
- Hawaii's Mauna Kea Golf Course announces reopening
- Georgia GCSA honors superintendent of the year
- Reel Turf Techs: Alex Tessman