Computerized equipment maintenance is an investment that pays dividends in the future.
During the past decade, the increased demand for optimum course conditions has put added pressure on all aspects of course management. That pressure to take the golf course to the next level filters down to every member of the maintenance staff. The mechanic in the shop is no exception.
It’s a shop manager’s job to keep the various pieces of equipment used to condition a golf course working instead of idling in the shop. This requires the ability to set a regular maintenance schedule, keep machinery sharp, keep detailed records of repairs and operating costs, and keep a running inventory of parts.
Each shop manager has developed his own way to juggle these aspects, from using index cards to saving old receipts to keeping stacks of legal pads with notes crammed in the top drawer of an office desk. Each system has been developed through trial and error and has served a purpose for each facility in its own way. However, with current technology, isn’t there a better way?
Past ways of keeping track of equipment maintenance have inspired the development of computerized maintenance management software. These programs allow any maintenance facility to track the many facets of machine maintenance easily to become more efficient. During the past 20 years, many such programs have been developed for many industries, but their widespread acceptance by golf course mechanics has been slow.
Golf course superintendents were faced with making the transition to becoming computer savvy first when sophisticated irrigation systems demanded a more technical way to operate them to their fullest potential. The repair shop is probably the last area of a golf operation that hasn’t made a full-scale swing toward computerization, but it’s a trend that’s becoming more popular. A computer program that tracks all pieces of machinery at a facility, as well as maintenance schedules, parts requirements and labor costs, is a tool that could only help make the shop manager’s job easier and his operation more efficient.
Jay Rehr was the head mechanic at Augusta National Golf Club for 16 years and now is a consultant to shop managers in the Southeastern United States. Rehr has seen how the position has changed first hand and is a strong proponent of using computer programs.
“The position of the shop mechanic has changed dramatically,” he says. “The demand on the machinery has changed. Mowing heights are lower; the time allowed for completing tasks has shrunk, which puts more demand on keeping machinery on the course working; and the machinery itself has become more complex.”
With more demands, it’s advisable to find new ways to coordinate the tasks to create a more efficient operation, and the use of CMMS programs is an important tool, Rehr says.
“For many years, a mechanic would just deal with things as they came, and the concept of records was usually confined to a series of notes,” he says. “While this method could be functional in the past, the drive to take golf course management into a more business-like approach demands the need for better ways to manage the shop.”
A better way to manage
The Broadmoor Resort – which will host the 2008 U.S. Senior Open – in Colorado Springs, Colo., includes three golf courses that are maintained with a staff of 70 employees during the summer. Don Steele, the head mechanic, is responsible for maintaining a $2-million fleet that comprises 250 pieces of equipment. Steele has been working in the shop for 28 years and has made the transition to a computerized management program.
“I’ve worked here for many years but really didn’t comprehend all of the complexities until I took the top spot in 1998,” he says. “When I began to inventory our parts room, I found shelves of parts that were obsolete because we didn’t have those types of machines on the property anymore. We had a computer program, but it wasn’t being utilized completely. It was then I figured there had to be a better way to manage things,” Steele says.
First, Steele assigns a number to each piece of equipment and then builds a file that includes make, model, serial number, maintenance schedule and parts requirements. He also has an inventory catalog so he can tell what parts he has in stock at any time, what parts he needs for future maintenance schedules and what he needs to order.
“The program prompts me about regular maintenance schedules, so it helps set up the work schedule for my three mechanics,” he says. “I can determine what parts are needed much faster than if I just had old notes. And at the end of the year, it’s beneficial for taking inventory of my parts supply and developing a restocking order.”
Another important advantage to Steele’s computer files is he can keep track of all costs associated with each piece of machinery, be it regular maintenance or how often the machine is being repaired. This helps determine when a machine isn’t being cost effective enough to use.
“For example, you might have two greens mowers and one runs just great, while another always seems to be needing some type of repair,” Steele says.
“With a click of a button, I can tell the entire life history of the machine. This is helpful when it comes time to decide which pieces of equipment are still serving their purpose and which ones are becoming a financial burden. Having a firm tracking of these true costs makes it easy to explain my needs when it comes to budget time.”
With a large operation such as Steele’s, it’s an advantage to have a budget that can support the cost of developing a computer management system. But the challenge is more daunting for a smaller operation. During the past three years, most maintenance budgets have been stretched to the limit partly because of cost increases for line items such as fertilizers and fuel. However, even a smaller operation can benefit from letting computers handle the necessary task of record-keeping, which is still an essential part of any shop operation.
Overcoming fear
The two issues that must be addressed are the time and money needed to incorporate a program for the shop and overcoming any fear of computers. A mechanic must view the computer as a useful tool that he’ll be in control of instead of something that will take over. And, just as superintendents have had to make the adjustments to the sophisticated irrigations systems and spread sheets that now are a regular part of their job, machine shop managers also will need to operate in the same efficient manner.
“The older mechanics and technicians have learned to do so much of their job by just storing information in their head, but as these men retire, it will be difficult for new employees pick up where the others left off without some information trail,” Rehr says. “I tell mechanics that it’s just smart to become computerized, but if not, they at least need to develop a paper trail of information for the people who takes their spots.”
Harold George, the head mechanic at the DuPont Country Club in Wilmington, Del., also has seen how the transformation to computers can be beneficial. George, who has worked at the facility for 36 years, is responsible for the equipment that maintains three championship courses.
“To be honest, in the old days, equipment maintenance was held together with bailing wire and chewing gum,” he says. “One of the big differences today is the improvement in the engineering of the equipment, which has made them more reliable but also more expensive. This means the mechanic must also be more sophisticated. Using a computer to help you makes sense. Mechanics need to look at the computer like it’s a box of Snap-on tools. If you start to use them, you’ll find out which parts will work for you.”
There’s an array of programs for shop managers that have been on the market for many years, such as Qqest and TRIMS. CMMS programs range in price from $500 to $4,000, depending on the program’s sophistication. Although CMMS are used mostly at larger facilities, many in the industry feel that, in the near future, computer-tool use will be the norm in the shop, rather than the exception.
For example, The Toro Co. has been developing a program for several years called MyTurf. It’s a Web-based program that’s been designed to be as user-friendly as possible to help mechanics overcome the fear associated with using a new program.
The decision to invest in CMMS ultimately is driven by economics. With budgets being tightened, the desire of green committees and general managers has been to keep machinery running as long as possible. Regular equipment maintenance can lead to a longer life span for these expensive machines, and investing in technology to reduce maintenance costs and increase efficiency within the shop can help achieve that goal. GCN
Doug Saunders is a freelance writer based in Truckee, Calif. He can be reached at dougs@sierra.net.
Electric diagnosis
Advances in maintenance shops are found not only in office computers but in the machinery as well. During the past decade, manufacturers have developed several advances in the diagnostic capabilities on equipment. The purpose of these smart machines, which have improved with added features, is too give mechanics a helping hand diagnosing electrical problems.
John Deere introduced a diagnostic feature on its 2500 series of greens mowers in 1998, according to product manager Tracy Lanier. A series of LED lights on the console informed the mechanic which circuit might be having a problem. Then, the next generation of the technology was introduced through the company’s White Box system, which can determine the exact point where power is flowing and where an interruption occurs. This saves the mechanic valuable time to make the necessary repairs. Currently, the White Box system is available on John Deere’s greens and fairway mowers.
Jacobsen equipment also is beginning to feature imbedded technology. Onboard software keeps track of the hours of operation, internal temperatures and other data that helps diagnose trouble. The ability to take important data out of the equipment is similar to what has been happening in the auto industry, says Peter Whurr, vice president for product support for Jacobsen.
The information stored in the equipment can be downloaded via a laptop computer by a Jacobsen dealer in a matter of minutes, saving time.
“We have been developing the onboard technology for several years,” Whurr says. “We have perfected the ability of our representatives to do instant diagnostics in just the last 12 months.”
A property with a large equipment fleet can purchase the software to diagnose equipment itself.
The technology is available in the Jacobsen fairway, rotary and greens mowers. GCN
Get curated news on YOUR industry.
Enter your email to receive our newsletters.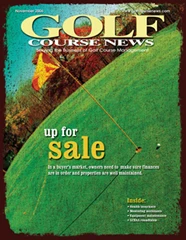
Explore the November 2006 Issue
Check out more from this issue and find your next story to read.
Latest from Golf Course Industry
- Carolinas GCSA raises nearly $300,000 for research
- Advanced Turf Solutions’ Scott Lund expands role
- South Carolina’s Tidewater Golf Club completes renovation project
- SePRO to host webinar on plant growth regulators
- Turfco introduces riding applicator
- From the publisher’s pen: The golf guilt trip
- Bob Farren lands Carolinas GCSA highest honor
- Architect Brian Curley breaks ground on new First Tee venue