
I talk to a lot of superintendents about safety programs and safety training, and they all say their crew’s safety is important to them, they genuinely care about their staff, and they don’t want anyone to get hurt on the job. But sometimes there is a disconnect between what you believe and how you act. Even if you know it’s the right thing to do and you’ve decided you want to start or improve your safety training program, if the person controlling the funding in your organization won’t approve the cost of getting started, what can you do?
When many golf courses are struggling to keep the doors open, it can be very tough to justify any expenditure that is not already “in the budget.” So how do you convince your general manager — or whoever is making the financial decisions — that investing in a safety program is worth the cost?
“When improving safety for the merit of just having a safer workplace is not enough, it’s often a very powerful argument with leadership to help explain the cost of safety by showing the economic benefits of safety,” says Ken Kolosh, manager of statistics at the National Safety Council. In other words, you’ve got to speak their language — the language of money management.
Return on investment (ROI) and cost benefit analysis (CBA) are common tools businesses use when making decisions about resource allocation. There are many theories and formulas for determining ROI or running a CBA, but you don’t have to have an MBA to put these numbers together. Knowledge of the costs to start and run the program and the costs associated with injuries are all you need to be able to make a convincing case.
Here are some approximate costs to start a safety program, based on an average crew size of 10:
Safety training materials: Most of the information you need to put together an effective safety training program is publicly available on the internet and in print media. If you are starting a new program, you might decide it makes more sense to buy training materials rather than spending your time sifting through a lot of published materials, including federal and state policies and industry or association guidelines and recommendations. Streaming safety videos offers convenient, on-demand access. We recommend investing in a flat-screen TV, signage and possibly hiring a consultant to help with your training. Most insurance companies have resources to help you implement a safety program, so be sure to confer with your club management about how your costs can be deferred. This approach ranges in cost from about$1,000 to more than $5,000.
Lost labor: There is a cost in lost labor dollars if your crew is sitting in a safety training session rather than mowing, setting up the golf course, raking bunkers or any of the other jobs you’ve budgeted labor hours for. Assuming a 10-person crew, average pay of $15 per hour, and about 45 minutes per month on safety training, your annual cost can be calculated at about $1,350 per year.
$15/hour x .75 hours/month = $11.25 per crew member/month, 10 crew members = $112.50/month, $112.50/month x 12 months = $1,350/year
Personal protective equipment (PPE): You are probably already spending money on PPE and may have it in your budget. Assuming a crew size of 10, your annual costs may look something like this:
Hearing protection: 2 cases (1,100 ear plugs) $200
Safety glasses: 25 @ $15 $375
Respirators: 2 @ $35 $70
Gloves: 25 pairs @ $8 $200
Spray suits: 2 cases of 20 $200
Work boots: 14 @ $100 $1,400
Total $2,445
Combining the safety training materials cost, lost labor cost and PPE cost, your total cost is approximately $3,795 to $7,795.
Once you have established the cost of your safety program, you need to determine the benefits of the program to complete the comparison.
The benefits of implementing an employee health and safety program include increased employee morale and retention, higher productivity, and reduced accidents and possible litigation associated with employee injuries. You may be stuck wondering how to assign a value to these benefits. One way is to look at the potential cost of an accident and recognize any reduction in those costs as a financial gain – or income – attributed to the safety program.
Costs of a workplace accident: The National Council on Compensation Insurance (NCCI) manages the nation’s largest database of workers compensation insurance information. Using data, including direct and indirect costs, they have determined the average cost of lost time and workers compensation insurance claims, for the following common injuries:
- Amputation: $186,881
- Contusion: $58,071
- Concussion: $109,452
- Heat prostration: $53,589
- Sprain: $64,675
If we use these as representative of the types of injuries commonly suffered by golf course maintenance workers, the average cost of a typical injury can be estimated at $94,533.
One last piece of information is necessary to make our comparison: How does the investment in safety training affect workplace accidents?
Many studies show a significant decrease in workplace accidents when a company implements a safety program. Here are a few examples:
- Insurance Offices of America clients reduced the number of workplace accidents by 28 percent, after using an online safety training program for just one year. (1)
- A study of smaller employers in Ohio who worked with OSHA’s SHARP program to adopt safety management principles found: (2)
- 52 percent decrease in workers’ compensation claims
- 80 percent decrease in cost per claim
- 87 percent decrease in average lost time per claim
- An OSHA review of the literature on the effectiveness of safety programs found companies can reduce injuries by 15 to 35 percent, compared to employers without these programs. (3)
Based on these and other studies, it is reasonable to expect your safety program to result in a 25 percent reduction in workplace accidents and injuries. If a typical workplace injury costs $94,533, the resulting savings or benefit would be $23,633.
Now you have the information you need to complete your ROI equation: ROI = (net benefits/total costs).
Cost to implement a safety program = about $3,800 to $7,800. Let’s use $6,000 as an average.
Benefit/Savings from safety program = $23,633
($23,633 - $6,000) ÷ $6,000 = +2.9, or an almost 300 percent return on the investment.
Including an ROI like this with your request to start a safety program provides a compelling argument that it’s not only the right thing to do, but also a smart business decision.
If your manager is still not convinced, do a Google search for “workplace accident jury settlements.” You will find pages of cases with multimillion-dollar awards for injured employees. After a thorough analysis of the numbers, the real question isn’t “can we afford to implement a safety program?” but “can we afford NOT to?”
(1) https://www.ioausa.com/risk-management-solutions/
(2) https://www.bmwe.org/cms/file/02152016_160833_SHPM.pdf
(3) https://www.osha.gov/dsg/topics/safetyhealth/OSHAwhite-paper-january2012sm.pdf
Get curated news on YOUR industry.
Enter your email to receive our newsletters.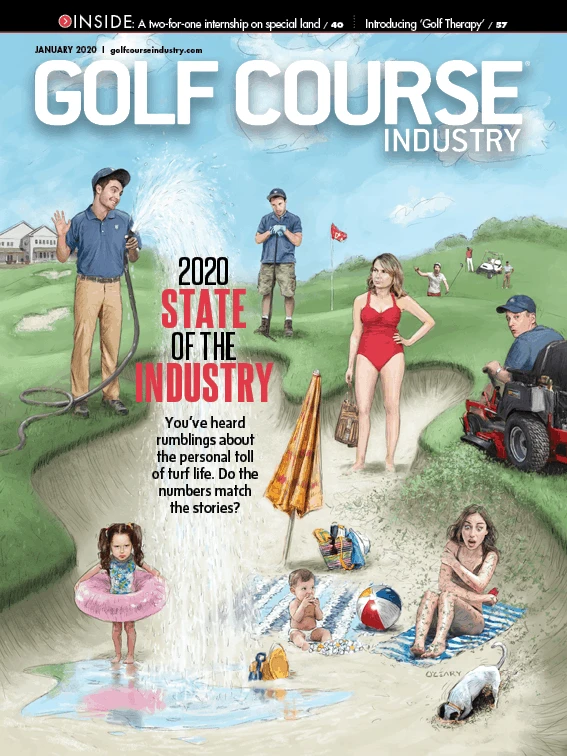
Explore the January 2020 Issue
Check out more from this issue and find your next story to read.
Latest from Golf Course Industry
- SiteOne releases new herbicide
- Bernhard Academy launches new online leadership, management courses
- Nufarm opens 2025 early order program
- Atlanta Athletic Club’s equipment ace
- PBI-Gordon announces 2025 Ryder Cup grounds crew sponsorship
- RISE convenes for 35th annual meeting
- Trust the process
- Envu’s Durentis Insecticide now on fertilizer