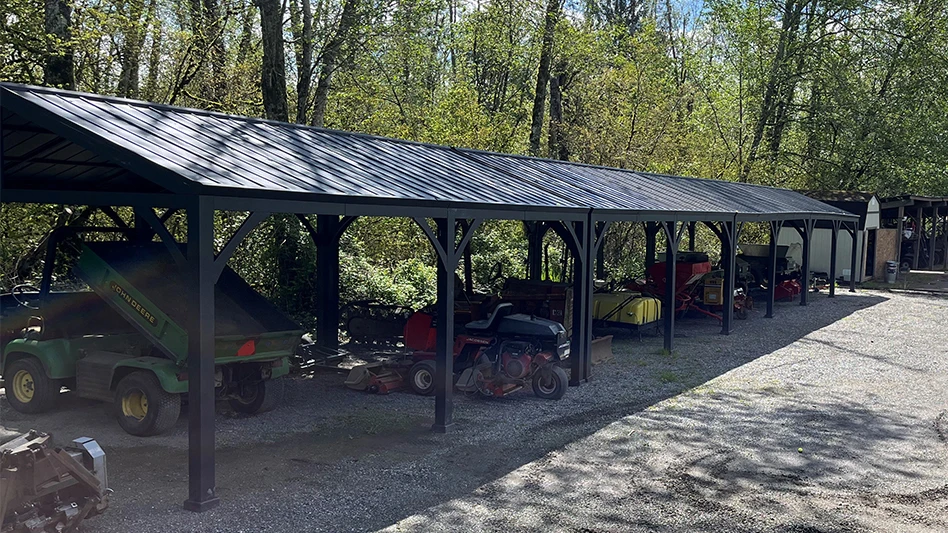

Although upgrades and new purchases can occasionally be a bit difficult for superintendents to get approved, they do occur each year. New pieces of equipment, new flagsticks, cups, benches, ball washers, sprinklers or even a new irrigation system. Difficult to obtain? Yes. But nothing lasts forever, and all things eventually need to be replaced or renovated.
The one area of the operation that seems the most difficult to get improvements on is the maintenance shop. Which, I suppose, makes sense. If golfers aren’t seeing the improvement, it can be hard to justify the expenditure for those spending the money.
For this reason, the shop and the maintenance yard around the shop often get neglected. Everything ages, but improvements, renovations or replacements are not commonplace. The maintenance shop and yard are almost always last in line for seeing any money for improvements. Generally speaking, they are the sore spot of a property.
Creativity is frequently needed on the part of those who work out of these areas. Not only do our facilities often need a renovation, but as we acquire more things each year, space itself becomes a huge issue. And for most of us, that space is not going to suddenly get larger any time soon.

Last winter, at our course, Avalon Golf Club in Burlington, Washington, we purchased some used equipment from a golf course that had gone out of business a few years earlier. It was nice to add some depth to our inventory, even if most of the pieces we purchased needed some basic upgrades to get them up and running. The presence of the equipment created a new problem: Where were we going to store everything?
We were already tight on space before we got the dozen or so new pieces of equipment. Once the purchased equipment arrived at our course, our shop yard instantly resembled a junk yard — which is never a good look. We quickly realized we were going to have to devise ways to store our equipment in a tidy, organized manner, while also achieving the ability to have every piece of equipment at least covered.
Some of our equipment gets parked inside our shop nightly. Pieces of equipment like carts, walk mowers, triplexes, trap rakes, rollers, sprayer, blowers, string trims and hand tools all have a home inside the shop. While this sounds like a lot, it also means a heck of a lot doesn’t get parked inside. Four tractors, rough mowers, fairway mowers, topdressers, trencher, excavator, aerifiers, sod cutters, electric brushes and a few other items must be parked outside.
Not being able to spend too much money on this, we concocted the solution of purchasing four 20-foot by 14-foot car ports. Considerably less expensive than having buildings or lean-tos built, the car ports, although not cheap at about $3,500 apiece, did provide a manageable way for us to get everything at the very least covered and also give the shop yard an organized appearance.
Because of limited space inside our shop, we’ve also purchased a couple fairly large sheds we put up next to our shop. One of the sheds is used for woodworking and paint supplies (we make our own tee markers), and the other shed is utilized by the equipment technician to store extra parts taking over his space. We also built a loft for storage above one of the bays in our long existing lean-tos. Lofts are a great way to create usable space without sacrificing anything else.
Another thing most golf courses accumulate each year is a significant amount of compost. I don’t know of a single golf course that doesn’t generate and maintain their own compost. Being able to reuse this “waste” on new projects is a pretty nice perk if you do take the time to maintain your compost.
But having space for compost can be a huge issue, especially depending on how much you actually generate. If you don’t end up composting and then reusing the material on the course, you could be stuck with yards and yards of soil that eventually will consume more space than you have. Some of the projects we use our compost on include filling in stump holes after we take down trees and grind the stumps and filling in bunkers that we have shrunk or actually eliminated during the winter. This is an ongoing project for us. We also use a fair amount of our compost each year at the clubhouse for flower and vegetable gardens.

We usually have three compost piles accumulating at any one time in different stages of composition. One pile is new compost we add to daily material such as grass clippings and sod. Another pile is in the “aging” stage that we turn with the loader from time to time. A third pile has composted fully and we use it on the course for projects any time we need soil. Having the space for these three piles is a constant challenge for us.
In addition to compost, many golf courses need a significant space set aside for wood debris. At Avalon, we cut down 20 to 30 dying or dead alders each winter. Before it was a golf course, the property was mostly alder and cottonwood forest, and the alders that were left between the golf holes have slowly been dying over the years. Alder is a very quick growing, weedy tree with a short life span. When they die, they die rather quickly from the tip down. It doesn’t take them long to become pretty unsightly. And the wood from these dying trees does not even include all the debris generated from windstorms throughout the year.
One way we deal with all this wood is to cut up and sell some of the alder each winter. We also end up having burn piles we throw a match to in the early spring each year. The wood we sell we put into a kitty for the maintenance crew that we use each year to have pools for the major golf tournaments or fun stuff for crew golf tournaments in the summer. Being able to sell some of the wood and burn the rest is the best solution we have devised to not have this impede on the limited space we have set aside.
Another space issue for golf course maintenance is the inevitable question of where to store the large amounts of sand and gravel most of us disperse each year. At Avalon, we have four different sand piles, each one almost always with some inventory: 1 millimeter, 2 millimeter, divot mix and bunker sand. Add to that a pile of crushed rock and a pile of pea gravel for drainage and a pile of landscape bark, and this can very quickly also become a space issue.
Keeping enough material available, but not too much, is usually the only solution here. Landscape blocks or railroad ties can make a good border to keep the sand contained and not contaminated.
Another space issue we recently encountered definitely required creativity to address. The issue involved our customer parking. We have a spacious parking lot, but because of the increase in rounds played the last four years, it simply is not big enough. We are a 27-hole course and occasionally conduct shotgun tournaments on all three nines. This means 220 golfers on the course at once, most of whom most likely drove solo. That’s a lot of cars. We simply don’t have the parking space we need. Vehicles will often park along the side of our entry road, which is problematic in several ways.
We ended up using the excavator this past winter to clear an area next to our main parking lot along the property border and created an extra 15 parking spaces. Still not enough, but better than it was.
Creativity and ingenuity go a long way in making your workspace functional while preventing you from becoming overcrowded and having that unsightly junkyard appearance.
We can all do without that.

Explore the July 2024 Issue
Check out more from this issue and find your next story to read.
Latest from Golf Course Industry
- From the publisher’s pen: Technology diffusion and turf
- Applications open for 2025 Syngenta Business Institute
- Smart Greens Episode 1: Welcome to the digital agronomy era
- PBI-Gordon promotes Jeff Marvin
- USGA investing $1 million into Western Pennsylvania public golf
- KemperSports taps new strategy EVP
- Audubon International marks Earth Day in growth mode
- Editor’s notebook: Do your part