
The condition of your greens will make or break you as a superintendent. So, when it’s time to improve a course’s putting surface, do you renovate or rebuild completely? It’s a crucial issue, one superintendents must vet carefully prior to breaking ground.
The greatest considerations are lost revenue and timing – or when is it ideal to undertake the project, says Steve Hamilton, superintendent at The Dunes Golf & Beach Club in Myrtle Beach, S.C. “Sometimes your business model and agronomic model do not line up,” he says. “It’s typically more expensive to renovate due to cost of material and time needed to rebuild putting greens.”
Hamilton did a no-till conversion from bentgrass to Champion Bermudagrass in 2013. “We did not need or want to change any of the architecture of the putting surfaces, so we sprigged on top of what we already had,” he says. “We also wanted to keep the organic material from the dead bentgrass around to help with the grow-in of the newly sprigged Bermuda. We did make corrections to some collar dams, so new sod was needed there. Obviously, cost is a concern, and not having to buy and distribute new greens mix allowed us to use those dollars towards a soil fumigant to kill all unwanted turf and nematodes.”
Resurfacing is generally less expensive than rebuilding entirely, says Tim Jackson, principal at Jackson Kahn Design. It is important to understand what issues are affecting the quality of putting surfaces when deciding on resurfacing versus rebuilding, rather than simply choosing one over the other based on relative cost, he says.
“Many times, there can be multiple factors that, when combined, have a deleterious effect,” Jackson says. “It is important to spend the time to understand what all of those negative factors may be to ascertain the best course of action.”
Jackson cites Brian Sullivan, a good friend and superintendent at Bel-Air Country Club in Los Angeles, who issued “one of the most simple yet profound” statements when consulting with a club considering a greens redo: “Science will determine the scope of the project, not opinion.”
Sullivan’s statement bears weight because many times a greens resurfacing will not address the root of the issues and a club can spend tremendous time, effort, dollars and impact to the membership, for what essentially is a short-term fix, Jackson says.
There are logistical considerations to account for, as well, says Doug Wright, project manager for Heritage Links. “Quite obviously, a simple resurfacing project will take less resources and time to complete compared to a full renovation project.”
A resurfacing project requires about one half of the labor hours a comparative renovation project would need, Wright says.
“This is based on our historical knowledge of past projects we have completed,” he says. “Completion time is a bit more complex, as the schedule is typically pre-determined by the club.”
In most cases, clubs limit the construction time of a greens project to about six weeks and selects a completion date that places them in an optimal grow-in weather window. The logistical factors are very much the same for each type of project. Both require pre-construction planning of labor forces, travel planning, housing arrangements, equipment mobilization, ordering and delivery of materials, and the execution of the work.
As for any the agronomic differences between a resurfacing versus rebuilding a green, Wright says most of it has to do with the greens’ pre-existing conditions. In a full renovation, the greens are rebuilt from the ground up, affecting not only the playing surface but also the sub-surface. Installing new drainage and greens mix changes the physical properties of the subsurface, including drainage characteristics, water retention capabilities and organic content he says.
With a resurfacing project, these properties remain the same since the work leaves the sub-surface largely intact, Wright says. The primary agronomic impact of a resurfacing project is to the playing surface itself, which is dependent upon grass selection. A new grass variety may play different than an existing one, as well as create new maintenance practices.
A resurface project is likely to last fewer years, but that depends on the original sand in the green, says Jeff Brauer, the principal at GolfScapes in Arlington, Texas. “USGA-standard greens may last forever, at least 20 years,” he says. “Re-surfacing is likely to last only 15 years or so, and some of that is due to turf contamination (also true of USGA greens). If its characteristics were good to start, it often doesn’t change much, unless water quality is poor, the greens frequently flood, etc. Sometimes, greens on a windy site can be clogged up with dust-born silt. It really depends on what is there.”

When resurfacing 1950-80 era greens, which are now usually too steep for typical green speeds, it is hard to soften slopes. However, using the USGA’s maximum deviation allowance for sand depths (2 inches up and down) you can sometimes shave 1 to 2 inches off a rise, and fill a valley by the same, which can effectively reduce the slope by 0.5 to 1 percent, Brauer says.
“That is often enough to make the green putt better,” he says. “It can work well, since deeper sand profiles drain faster (which would occur in valleys) and shallower ones drain slower (now on top of crests), which in theory helps maintain constant moisture. I have seen it work.”
When rebuilding the root zone from the ground up, the base must be reshaped to proper grade and then the various layers added in close to perfect and consistent depth, Brauer says. “Some superintendents have grown accustomed to working with what they have, and others feel much more comfortable rebuilding to higher standards of USGA,” he says. “We always factor their opinions into our recommendations.”
As an example of the difference between resurfacing and rebuilding greens, Jackson says for 100,000 square feet of greens with a 12-inch sand base you can expect to remove between 4,500 to 5,000 tons of old greens mix, and replace it with a like amount of new greens mix. There will be 2,000 tons of pea gravel plus or minus. For reference, that is 4.3 feet of combined material over one acre of land. There also will likely be approximately two miles of 4-inch perforated pipe that will underlay a USGA greens construction at 100,000 square feet.
“Hauling that amount of material through an existing golf course on the cart path system can take a fair bit of time depending on the design and routing of the course, use of relatively small volume hauling equipment so as not to damage the path system, and limited access points,” Jackson says “A resurfacing project typically may only remove the top 2 to 3 inches of sand, or not at all. Certainly, the latter is much simpler from a logistical standpoint and the project can be accomplished in a smaller work window.”
Slope is the prime determinant when considering resurfacing over renovation, says golf course architect Rees Jones. “A lot of greens were constructed for slower speeds, so that must be taken into consideration,” he says. Therefore, if you are going from a push-up green to a USGA green, you will likely have to rebuild.
It is also important to factor in the type of seed intended for the redone greens, as certain varieties will make for slower or faster ball speeds. Jones says a proper “mapping” of a course’s greens to “find out exactly what you have to deal with in terms of slopes and other factors” is essential.
Renovation affords a known, complete ground-up rebuild with drainage, greens mix, with total flexibility to alter green contours/slopes, says golf course architect Bobby Weed. “Through sound design/construction specs, a superior set of consistent greens can be constructed for the long term,” he says. “Resurface is living with past construction standards with the only notable improvement being changing out the turfgrass.”
Some clubs consider a combination of greens resurfacing and renovating. Weed cautions against such a piecemeal approach. “The decision is either one or the other,” he says. “If the short-term decision is cost related and the resurface method is not successful, then a costlier renovation will be inevitable.”

Weed recommends a thorough and exhaustive due diligence process when considering a greens project. He warns an uninformed decision can be costly. For example, a hasty decision to resurface when a renovation would have been the appropriate direction may result in renovating sooner than later.
“Time-wise, a properly constructed green will better allow a resurface at a later date and provide the longest lifespan of the green,” Weed says, adding there is no substitute for a properly constructed set of greens.
Both approaches to a greens redo have been done with great success over the years. “It all depends on the facility, and what they are looking to get out of the project,” Hamilton says. “If there are no changes in architecture needed, greens have good surface drainage and current organic layer is not an issue, a resurface may be the best route to take.” If a facility desires changes to slopes or location, there is poor surface drainage, or high levels of organic matter in the greens, then renovation may be needed. “Again, no matter what is chosen, the project comes down to research, proper planning, and a cohesive team that are all on the same page,” Hamilton says.
As for any trend favoring resurfacing greens over renovation, or vice versa, Brauer says, “Here in Texas, resurfacing is pretty big among mid- and lower-level courses. It’s cheaper, faster and less intrusive, and we grow mostly Bermuda, which is thought to tolerate different soils much better than bent.”
There isn’t a discernible trend in the industry that favors one over the other, Wright says, adding he sees a lot of both types of projects. “The full renovation projects are probably more noticeable in media and the public eye because they are usually completed by larger contracting companies, often as part of other improvement projects,” he says. A lot of the resurfacing projects are completed “in-house” by clubs using their maintenance staff, which results in less exposure.
The only trend Jackson sees is good facilities with good management and good governance tend to make good choices. It takes a strong, well-informed greens chairman (or committee) or club president (or board of directors) to lead a membership down the correct path, he says.
“We have been fortunate to work with a lot of highly intelligent committee members at clubs with whom we consult, who are motivated to understand the science, the options, and the outcomes,” Jackson says. “Cost and time have many times been the secondary consideration. Getting it right has been primary.”
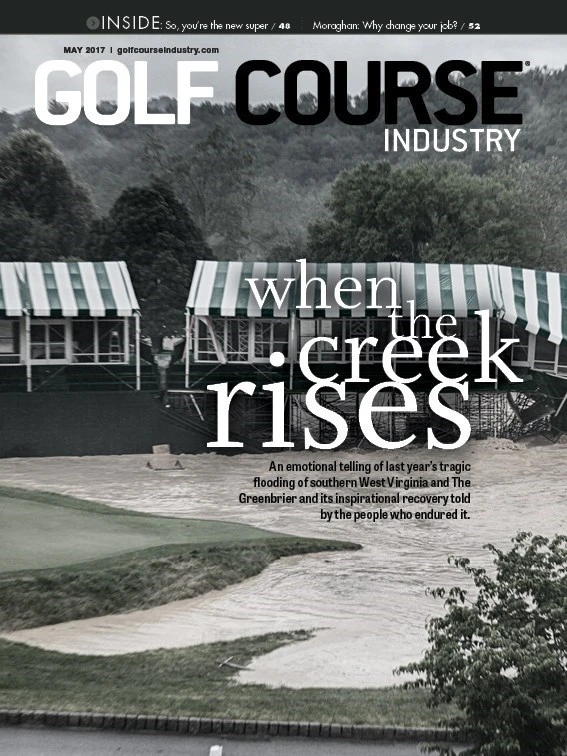
Explore the May 2017 Issue
Check out more from this issue and find your next story to read.
Latest from Golf Course Industry
- From the publisher’s pen: Foggy intrigue
- USGA releases Water Conservation Playbook
- Vilamoura Golf courses awarded GEO Certified status
- GCSAA’s Health in Action 5K/2K reaches fundraising goal
- Landscapes Golf Management to participate in data analyzation initiative
- Reel Turf Techs: Carl Michael
- Atlanta Athletic Club approves funding for master plan
- Maximizing Cultural Practices and Agronomic Benefits with Minimal Surface Disruption