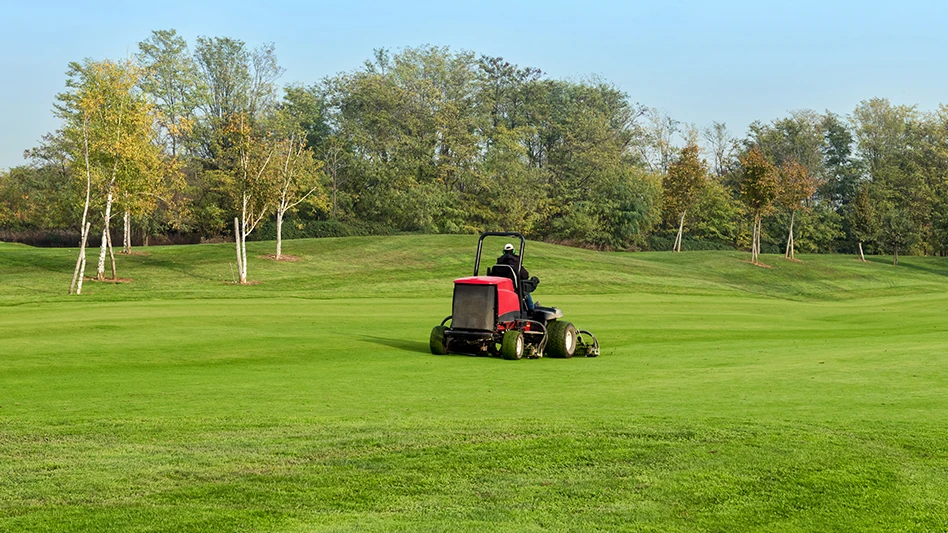
Adobe Stock
How long maintenance equipment lasts before it is replaced depends on many factors, including usage frequency throughout the year, climatic conditions, preventative maintenance programs, employee care when operating equipment, and whether the equipment is stored inside or outside in sunlight and moisture. The accompanying life expectancy chart shows estimated guidelines for equipment replacement in a range of years, knowing that some equipment will last longer than planned and other equipment will need to be replaced sooner than expected. The following are some important items requiring more explanation than what’s listed in the chart.
Equipment managers and assistant mechanics/technicians
The equipment manager is the most important person for successfully operating a preventative equipment maintenance program. The GCSAA’s successful Equipment Management Certificate Program’s (EMCP) Level 1 and Level 2 curriculum must first be completed before the Certified Turf Equipment Manager (CTEM) status can be achieved.
Computer Maintenance Management Software (CMMS) from various companies provides equipment maintenance scheduling, assignments, labor tracking, servicing, documents and history, parts ordering and inventory, proactive maintenance notifications, fleet health monitoring, and equipment location tracking. GCSAA Equipment Management Resources are also a great reference tool.
On an 18-hole facility, it’s extremely important to have not only the equipment manager but an assistant mechanic/technician on staff. That person is typically responsible for performing routine preventative maintenance servicing, along with grinding, lapping and other tasks. The equipment manager executes repairs, orders parts and keeps records, grinds equipment, trains employees, and guides the assistant mechanic/technician.
It’s virtually impossible for the equipment manager to operate at an 18-hole venue without an assistant mechanic/technician because new electric, hybrid, autonomous and robotic technologies, and expanded equipment inventories are too much for one individual to handle. Additional repair parts also should be kept in inventory because of supply-chain issues and concerns. Attending service schools provided by the local distributor or equipment manufacturer during the off-season is vital continuing education for both individuals.
Capital equipment replacement programs/capital reserve budgeting
Superintendents have graduated from a five-year to a 10-year capital equipment replacement program, which is typically updated annually. Capital reserve budgeting is then executed by setting aside funds to help pay for purchased or leased equipment. With the supply-chain issues and concerns still in the “backorder” mode, superintendents must order new replacement equipment or new technology equipment at least 18 to 24 months in advance — and hope it will be delivered when forecasted. Superintendents also like to provide the original and current expected life on their maintenance equipment inventories, updated annually, for additional documentation for the budget process.
Capital equipment replacement budget standards for the golf industry typically include 15 to 20 percent per year of the total equipment inventory replacement value, or 20 to 25 percent of the annual golf maintenance operating budget per year.
Superintendents typically prefer leasing all equipment under a Fair Market Value (FMV) lease arrangement when it is used on a daily, regular high-use basis and then totally replacing the equipment after the three- to six-year term expires. Greens, tees, collars, approach, fairway and rough mowers, riding bunker rakes, sprayers, turf vehicles, and topdressers comprise this group.
A full payout ($1 buyout lease), where the equipment is owned at the expiration of the lease, is typically not preferred because this high-use equipment has reached its life expectancy and should be replaced instead — except for possibly keeping a few select equipment for other purposes, such as mowers used after verticutting and topdressing, and some as a backup contingency plan.
Lease payments should not be placed on the golf maintenance operating budget, as they are obviously capital expense items placed on an operating budget, but it is commonly done for accounting purposes because leased equipment cannot typically be depreciated. This practice noticeably increases the operating budget, making the numbers deceptive to course officials because of the added expense. Lease payments should be placed on a G&A account or separate account because they are capital expense items, not maintenance operational budget expenses.
Equipment used less frequently with a longer life expectancy, such as tractors, trucks, skid-steer loaders, fairway aerifiers and topdressers, trenchers/backhoes, chippers and dump trailers, are typically purchased. This equipment is typically put on a capital equipment replacement budget that can be depreciated.
New tech and additional equipment acquired in an FMV Lease, a full-payout lease or purchased can depend on its frequency of use and the financial arrangements desired by the course. There should be a minimum of two pieces of the same equipment for each maintained area, as a backup is used during repairs while waiting for repair parts or when equipment is being serviced.
AI-powered drone aerial equipment monitors and sprayers, autonomous and robotic mowers, GPS-guided sprayers, hybrid- and lithium-powered mowers and turf vehicles; e-walk behind and e-triplex greens mowers, and e-hovercraft mowers are among the emerging tech available to golf courses, with more exciting developments on the horizon.
Hour meters
There are two “hour-meter standards” to determine their “car miles equivalent” traveled so that course officials can better understand the relevance and true meaning of hour-meter readings.
Turf equipment: One hour equals approximately 80 miles on a car; 3,000 to 4,000 hours equals 240,000 to 320,000 miles on a car.
Turf equipment engines: 500 Hours equals 100,000 car miles; 1,000 hours equals 200,000 car miles; 3,000 hours equals 300,000 car miles equivalent.
Noise ordinances
Noise ordinances, especially those found on housing development-type courses, are becoming stricter and enforced more frequently. Electric- and lithium-powered equipment has made great strides in toning down the decibel level, making for happier homeowners.
Equipment storage
All maintenance equipment should have enclosed and covered storage (if necessary) to keep damaging sunlight and moisture from shortening the life expectancy of equipment in all three climatic zones.
Photo/video journal
Individual photos of each piece of equipment and/or a video journal should be compiled annually to help prove to insurance companies, if necessary, that it was owned/leased by the club and in inventory. They should be secured and stored in a safe, fireproof environment.
Get curated news on YOUR industry.
Enter your email to receive our newsletters.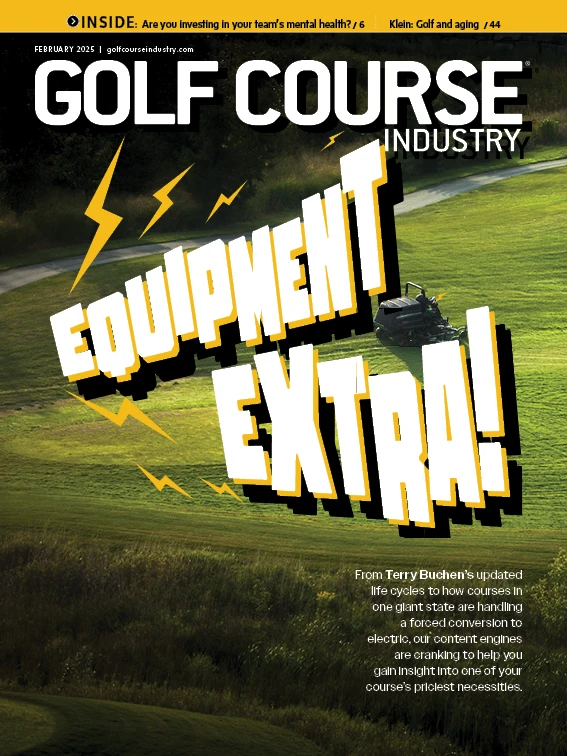
Explore the February 2025 Issue
Check out more from this issue and find your next story to read.
Latest from Golf Course Industry
- SiteOne releases new herbicide
- Bernhard Academy launches new online leadership, management courses
- Nufarm opens 2025 early order program
- Atlanta Athletic Club’s equipment ace
- PBI-Gordon announces 2025 Ryder Cup grounds crew sponsorship
- RISE convenes for 35th annual meeting
- Trust the process
- Envu’s Durentis Insecticide now on fertilizer