

Uncertainty surrounding electronics, robotics, diagnostics, labor and turf equipment costs means the importance of the equipment manager position to a golf operation should accelerate over the next decade.
Consider the career of Joe Moreira. Earlier this year, Moreira switched equipment manager jobs, shifting from Lake Toxaway Country Club to 27-hole Etowah Valley Golf Club & Lodge. Moreira received numerous opportunities to job hop during his six years at Lake Toxaway. Remaining in North Carolina while obtaining more responsibility appealed to him. His new job provides life flexibility and he’s encouraged to grow professionally, as evidenced by his vice president position in the Turf Equipment Technicians Association of the Carolinas.
Educational and networking opportunities matter for Moreira and his peers. Every emerging part or component inserted into turf equipment units — and every piece of equipment with a lifespan that must be extended — will test equipment managers in new ways. Knowing more is a proven way to combat the unknown. Equipment managers must know plenty to successfully navigate their days, weeks, months and years. Plenty of people even inside the industry, according to Moreira, still don’t realize how much a modern equipment manager must know.
“They say, ‘He’s just a mechanic,’” he says. “Well, not really. I have a budget, I do accounting, I do risk management, I’m doing safety classes. I have to make sure everybody is safe using a chainsaw.” Because of the versatility the job requires — and because a glut of unfilled equipment manager positions permeates the industry — Moreira is certain about one part of his future. “I believe there’s a huge demand for our skillset,” he says. “I believe there’s not enough of us. I’m not of the mindset that I’m going to train somebody to do what I do and then they will take my job. If I train somebody and they become better than me, that makes me better.”
Mike Elliott has reached a career juncture where he’s proactively identifying and training the next generation of equipment managers.

After a nearly a 12-year stint as the equipment manager at acclaimed Pine Valley Golf Club in southern New Jersey, Elliott accepted an offer to lead The Union League of Philadelphia’s equipment manager program.
Once exclusively a downtown social club, The Union League now supports three golf courses in three distinct Philadelphia-area locations: 27-hole Union League National in southern New Jersey, Torresdale in northeast Philadelphia and Liberty Hill in suburban Lafayette Hill. Elliott oversees a mechanical team consisting of an equipment manager and an assistant at each location. “We’re always looking for the next 17-year-old kid coming out of high school who wants to turn a wrench for a living, because it’s definitely been changing in the last five years,” he says.
Elliott can relate to a young person seeking a career fit. He started working on a golf course as a 14-year-old. Elliott moved from his native Maryland to Colorado in the late 1990s and transitioned from the grounds crew to an assistant equipment manager role at Boulder Country Club because the position provided year-round employment. Less than three years later, he landed the head equipment manager job at Coal Creek Golf Course.
The biggest differences since the early 2000s, according to Elliott, involve how equipment managers are treated. Salaries and wages are increasing; many work weeks are decreasing. Elliott expects both trends to continue, because “people are starting to realize how important this position really is and how hard it is to fill.” Elliott tries to keep peak-season workdays for his staff in the eight- to 10-hour range.
Competitive wages and manageable hours can only take recruitment efforts so far. Developing a capable equipment manager requires patience. The progression from assistant-in-training to assistant superintendent is common throughout the industry, and thousands of superintendents have sent protégés onto head jobs. Only 29 percent of golf courses employ an assistant equipment manager, according to a November 2023 @GCIMagazine X poll.
“If you get two or three interns or an assistant-in-training who has gone to school for agronomy, you can pop out superintendents every few years,” Elliott says. “But if you take somebody who doesn’t have the background as a mechanic and you’re trying to teach them from scratch, it’s a three-year process before somebody is ready to take that step and set up a shop.”
The equipment managers Elliott is developing are maintaining units that are getting “a little more intricate and advance with computer systems.” The integration of computers, robotics and electronics into equipment maintenance could lure young people to the industry. It also could result in some veterans leaving the industry.

“Going to equipment with all these electronics and computers in them will make the job tougher,” says Tim Thurston, the equipment manager at Ambassador Golf Club in Windsor, Ontario. “You have to get more training on things every time something new comes out. It’s going to be harder to test and find faults. It’s getting to the point where you have to plug it into a computer like the automotive side does to find issues — and the price has increased because of it.”
Trent Manning views the ongoing management adjustments and looming technological changes as an opportunity for the industry.
The equipment manager at Ansley Golf Club, a 27-hole, Atlanta-area facility with two locations, Manning has assumed a leadership position among equipment managers by creating the Reel Turf Techs podcast and WhatsApp group, a pair of beloved digital resources for hundreds of experienced and inexperienced colleagues.
The conversations on the podcast and app indicate that equipment managers will need evolving skillsets to flourish. “We’re going to have to eventually learn how to code,” Manning says. “And we’re going to have to spend more time behind a computer.”
Manning mentions a chainsaw produced by a major manufacturer as an example of where bigger units are headed. The chainsaw features a microprocessor and connects to a laptop.
“I think it will attract more people to the industry, because I do feel like the younger generations are more tech-savvy,” Manning says. “Kids are now getting smartphones at whatever age. They are more familiar with that type of stuff. It even fascinates me to be able to plug a laptop into a chainsaw. That’s cool. In fact, it’s a lot cooler than the old tools that we used.”

Many equipment managers are relishing the expanding ways they can meld a digital mindset into the tactical and organizational parts of the job.
Justin King, the equipment manager at Jamestown Park Golf Course, a municipal facility in North Carolina’s Piedmont region, relies on a digital job board program and Google Sheets to track orders, machine hours and grinding data. At Philadelphia Cricket Club, equipment manager Shawn Bergey’s team spent this past season observing and maintaining more than 30 autonomous units mowing rough and the club’s four acres of tennis courts. Conversations with the three major golf mowing manufacturers suggest to Moreira that future colleagues will possess mechatronics degrees. Mechatronics is a discipline combining engineering, electronics, robotics and computing.
Cool? Intimidating? Or both?
“I don’t think it’s going to necessarily change my job or how I do my job,” says Kenosha (Wisconsin) Country Club equipment manager Justin Prescott. “It’s going to change what I’m doing in my job. It’s a matter of adapting. If I have to use a computer to program a robotic mower, that’s just another tool I’m going to have in my toolbox. I have wrenches, I have sockets, I have computers in my toolbox now.”
Freedom to tinker is frequently cited as a joy of the job, and diagnosing problems via computer will alter work habits. But technology should put equipment managers in a position to tinker smarter.
“You have so many opportunities in this job to find creative solutions,” Elliott says. “It’s not just what’s wrong with an engine. We’re trying to accomplish something on a golf course. We are trying to get something from Point A to Point B. There are so many different levels where you can help people out. And everybody comes to the mechanic.”
Equipment managers are bracing to field more questions and requests, especially given the condition of the current golf market, where soaring equipment and labor costs are challenging facilities despite the play and revenue surges since 2020. Elliott cites the expense of a fairway mower — some units now exceed $100,000 — as one area that will place significant pressure on an equipment manager to extend the lifespan of their employer’s investment.
Long shipping delays on parts and new units will further test the ability of equipment managers to find imaginative solutions. More prominence always comes at a cost.
“Maybe that’s why we are more valuable now, because we’re being asked to repair stuff without being able to get parts on it, so you have to get creative sometimes in how you can make a repair without a part coming from the factory,” Manning says. “Then when you have a set equipment replacement schedule in place, and you’re not replacing that equipment, that leads to more repairs, more downtime and more stress for the equipment manager.”
Get curated news on YOUR industry.
Enter your email to receive our newsletters.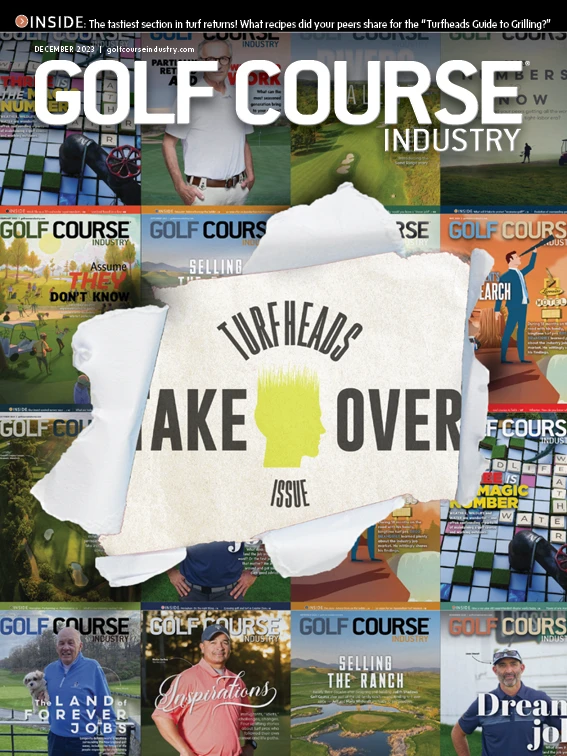
Explore the December 2023 Issue
Check out more from this issue and find your next story to read.