Jim Pavonetti considers himself lucky to have a full-time mechanic on staff. Still, Pavonetti has done his share of time in the garage at previous clubs, including his very first superintendent’s position, and he’s no stranger at Fairview’s when the need arises. In either camp, he’s not alone, as our research found out. During the first quarter of 2011, GCI queried North American golf course superintendents about the equipment maintenance trend they were experiencing at their respective facilities. Of the nearly 370 superintendents who completed the survey, three quarters have a full-time mechanic on staff. Here are the trends between the Have’s and Have Not’s.
“Most supers can do the basics,” he says. “I don’t know anyone who can’t set up or work with a greensmower.” When repairs get more complex, Manfull relies on his experienced mechanic. More than a quarter (28 percent) of supers who have a full-time mechanic on staff indicated an assistant mechanic, part-time mechanic, foreman and other laborers handle repair and maintenance responsibilities, too. For Jim Myers at Seattle’s Plateau Club, that staff is necessary. “We definitely have a need for a full-time guy,” he says. “We could use a full-time and a part-time equipment manager, with all our equipment, all the grinding, the repairs. Our equipment manager is just as important as our assistant superintendent.” Overall, facilities with full-time mechanics budget, on average, around $27,500 annual for equipment maintenance and pay mechanics an average salary of $42,900, with around $70,000 on the high-end of the compensation spectrum and $27,000 on the low-end, the data says. Regarding salary, it should be noted that GCI’s research did not break down facility or fleet size when analyzing compensation. An on-staff mechanic likely contributes to the quick turn-around rate for broken equipment, with 82 percent of superintendents indicating idle equipment remains out of commission for only 24 hours, and very rarely longer than one week. Having a full-time mechanic gives Myers the flexibility to have someone working on equipment the moment it goes down, and sometimes well beyond regular hours to keep the staff moving the next day. “It’s necessary, especially during the season, and you’re out trying to mow and do aerification and something breaks down, and you’ve got to have it back up and running within a very limited window,” Myers says. “Sometimes he’s been in the shop until 11 p.m. getting equipment ready and is back getting it onto the field at 5:30 the next morning.” “He really does it all for us,” says Pavonetti of his mechanic. “He comes in an hour before the crew and leaves after them, and has everything set for us. It’s a pretty good system. With $2.5 million in equipment here, to have a guy watching over it full time would be prudent.” Regarding their equipment, facilities with a full-time mechanic purchased the majority of their mowing and cultivation equipment (80 percent) rather than leased it (20 percent). Likewise, they tended to purchase this equipment new (83 percent) rather than used (17 percent). As the equipment ages, Manfull’s mechanic proves useful time and again. “It allows us to be so much more efficient with what we have,” says Manfull. “We don’t have to worry about breakdowns and relying on someone else to fix it. If we didn’t have a mechanic we wouldn’t be able to give as much attention to the course with our equipment.” Even in terms of repair cost, a full-time mechanic makes the process easier for Pavonetti. “He does all the pricing and the work involved in finding what parts are needed and will come in to tell me where it’s at,” he says. “I’d rather go without an assistant than without a mechanic.” Lastly, an in-house mechanic encourages equipment innovation. Nearly half (47 percent) of superintendents fabricate materials and tools in house. “It’s about having the time for troubleshooting or solving problems. It’s nice to have an equipment manager that can weld and fabricate things,” says Myers. “We do so much fabrication, it’s unreal. Recently we basically fabricated a whole trailer to our specs, from tires to hitch to whatever.” 75% of superintendents surveyed have a full-time mechanic on staff.
“To the best of my skills, I’m the mechanic,” says Dan Mulder, superintendent of Landsmeer Golf Club in Orange City, Iowa, who is one of the 60 percent of superintendents who indicated they handle all maintenance and repair issues. “Our budget just doesn’t allow us to hire a mechanic.” Another 30 percent had an assistant superintendent handle various repair and maintenance duties. And according to the data, less than 20 percent employ a part-time or seasonal maintenance person. Only a small percentage – around 10 percent – contracted with a local equipment dealer to assist in troubleshooting equipment issues. Though his own history as a mechanic comes from working on vehicles or time spent in the course’s garage, Mulder is working with an assistant to train him in the basics he can already cover. He also has a good relationship with a local distributor, who he calls on for quick advice when he’s unable to work a repair out himself. “What I find myself doing is I’ll do everything I possibly can. If it gets to the point that I can’t do anything with it, it goes to the dealer,” says Mulder. “About 80 to 90 percent of the time, it’s something I can handle myself.” Fifteen percent of respondents indicated their equipment doesn’t receive regular maintenance, less than 2 percent grimly responded that broken equipment just doesn’t get fixed. “I feel confident we have our equipment in pretty good shape,” says Mulder. “Sometimes it’s just the preventative eye care you can give it just checking it over every day.” Similar to their colleagues with full-time mechanics, these superintendents are rather proficient with repair duties when equipment does go down, with 66 percent indicating broken equipment remains down for only about 24 hours, and another 29 percent say equipment is typically back in action within a week. “It’s a really hard time when you’re trying to work on the turf, like spraying or fertilizer, and something goes down, you have to start asking yourself, ‘Should I be working on this or on the golf course?’ Where do I spend my time?” asks Mulder. However, unlike maintenance departments with on-staff mechanics, these crews are not as resourceful cobbling together unique equipment solutions on site. According to the data, only 25 percent of superintendents indicated they fabricate their own materials and tools. “During the season, it’s very stressful,” says Mulder. “But during the winter, I actually consider it fun. You have time to work on it and solve your own problems.” 25% of superintendents surveyed do not have a full-time mechanic on staff.
“It’s important for supers to be their own mechanic at times,” says Pavonetti. “The crew doesn’t look at you as much as a suit-and-tie guy. I think I get a little respect from them for it, when they can see I came from where they are.” Besides building rapport with his team, knowing his way around the garage pays off in his being able to check on work being done or train a new crew member himself. Now, whenever he has an intern, he makes him spend a week just working with the mechanic. “It’s part of the intern’s requirements to work in the garage,” he says, “and the mechanic purposefully sets up machines that need to be worked on.” It’s possible for the intern to find a club in the recovering industry that won’t require him to be hands-on with the equipment, but not likely, he says. “Some of the younger guys think their first job is just going to jump right into a position with a mechanic and two assistants. But you have to be able to know all those things so you can take care of them yourself if you have to, and can train your own crew.”
My advice: Let’s get back to basics. Let’s polish our collective A-games. This can be your day to shine and the day your employers are glad they have you on their payrolls. So I want to encourage you to leave your warm and fuzzy comfort zone behind and follow “Weidler’s Top 5 Equipment Maintenance Tips.” No. 5 Tools for the job
This creates a mess, but what you may find will make it all worthwhile. Check hydraulic hoses for shiny spots – the old residual of hardened water has the tendency to turn the hoses white where they were rubbing. Check all hydraulic lines (metal) for rub points -- these can be shiny or rusty. If you have light contact, check your mounts. If they’re OK, just slice a small section of rubber hose and place between the affected area. If you find major contact, record this for your winter maintenance. Check the frame for rusty areas – this is where a crack has developed. Record this for your winter maintenance. You can also mark the crack with a paint marker. Check for electrical corrosion at contact points. This will be a green-blue color for brass and copper connection, or white for aluminum connections. Record all of your findings for later maintenance.
John Weidler is equipment manager at Ironbridge Golf Club in Glenwood Springs, Colo., and a contributor to GCI.
|
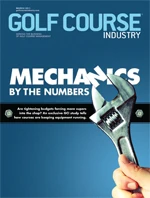
Explore the March 2011 Issue
Check out more from this issue and find your next story to read.
Latest from Golf Course Industry
- Advanced Turf Solutions and The Aquatrols Company release soil surfactant
- Heritage Golf Group acquires North Carolina courses
- Editor’s notebook: Green Start Academy 2024
- USGA focuses on inclusion, sustainability in 2024
- Greens with Envy 65: Carolina on our mind
- Five Iron Golf expands into Minnesota
- Global sports group 54 invests in Turfgrass
- Hawaii's Mauna Kea Golf Course announces reopening