While many golf course projects are the result of hours spent on computer screens and drafting tables, a more field-design-oriented approach can yield high-quality layouts and substantial cost savings for developers. An example is the nine-hole addition at the Golf Club at Devils Tower, which is scheduled to open this month in Hulett, Wyo.
Working with developers James and Jim Neiman and project manager Darren Flanagan of The Golf Course Co., Kevin Atkinson of Phelps-Atkinson Golf Design crafted nine holes and renovated the existing nine into an 18-hole layout.
“The organization of the construction contract at Devils Tower was created with the understanding that many of the greatest golf holes weren’t necessarily designed in detail on a plan but discovered in the field during construction,” Atkinson says
The construction contract was structured so shapers Greg Martin and Ben Chambers, along with Flanagan, were paid a fair monthly fee, while the owner supplied most of the equipment, materials, fuel and some local labor, according to Atkinson, who estimates the owners saved as much as 35 percent on earth-work costs.
“This unique structure allowed all the people involved to concentrate on creating the best golf holes possible within a reasonable budget, without the worry or hassle of change orders and the heartburn typically associated with them,” Atkinson says. “The arrangement also allowed the owner to use his own heavy-construction equipment and local operators to clear trees and complete the heavy earth work.”
Flanagan, who has built golf courses throughout the world, says this concept was something he wanted to try in the United States.
“The joy is that it minimized the cost to complete the project,” he says. “We could make changes and field adjustments without the ownership absorbing additional costs through change orders. Given a choice, I would build 90 percent of my courses this way.”
Preserving natural beauty
During the development the course, the Neimans wanted to maintain the area’s cultural and natural history as much as possible. For example, the family requested Atkinson and Flanagan preserve a stand of trees that grew from seeds that sprung roots in tracks along a high bluff used by wagons making their way West in the late 1800s. The family also restored the 1800-era Charlie Maze cabin located between the 16th green and 17th tee.
The Neimans encouraged Atkinson to use as many native plant species as possible.
“Doing this the way we did gave us the ability to protect certain areas and enhance their natural beauty,” Jim Neiman says. “To capture the natural beauty of an area is difficult to do from a map and blueprints. You need some flexibility to work with the trees and the landscape.”
The Neiman family – who operates Devils Tower Forest Products, the area’s largest employer – was focused on helping the community grow. Their idea was to draw visitors and second-home buyers to the area. So, they hired Dick Phelps to build the first nine holes, which opened in 1998.
The family’s plan was to tie the golf course in with a recently built neighboring airport that has a 5,500-foot airstrip, allowing it to accommodate small- and medium-sized jets. Those flying into Hulett can land, be picked up in a golf cart and be standing on the first tee within five minutes.
“When I started looking at the best group of visitors to attract to our community, pilots, golfers and hunters seemed an ideal mix,” Jim Neiman says.
The original nine ran over fairly open, high-prairie land. The new nine was slated for a more challenging piece of ground incorporating large red-rock canyons and cliffs, along with dramatic views of the surrounding Black Hills and Devils Tower – a monolith that rises 1,267 feet above the meandering Belle Fourche River that was dedicated 100 years ago as the nation’s first national monument by President Theodore Roosevelt.
Local help
When Atkinson started the project, he didn’t have much time to develop construction documents for the new nine holes. The only drawing he did was a basic routing plan.
Atkinson also planned renovation work to the existing nine: rebuilding bunkers; adding a few tees; upgrading the irrigation system; widening fairways; incorporating native grasses; and transplanting and removing trees that yielded a more open, high-prairie feel to the existing front nine. Flanagan figured out how to implement these plans cost effectively.
“When we first looked at the site, we started thinking about the high mobilization costs of getting equipment into the area,” Flanagan says. “We noticed the Neiman family had a lot of equipment, scrapers and track hoes. We convinced them they could use the equipment and local operators under our direct supervision, which would allow us to create the new nine and the renovations more economically without the need for the administration of work orders and projects that were not specified in the contract.”
The owners liked the idea because it allowed them to participate directly in the project development. James Neiman built all the stone walls with large boulders he’d been collecting for 10 years from various construction projects in the area and during construction of the golf course. He used one of his logging trucks with a claw-like loader to place each stone.
Using scrapers, bulldozers, lumbering and specialized golf-construction equipment, local labor and six golf-construction specialists assembled by Atkinson and Flanagan, the pair basically designed and built the course in the field. Flanagan characterized the golf-construction veterans as a group of experienced shapers and drainage experts who were good at what they did and adaptable to changes in daily equipment and labor conditions.
“We brought in the experienced personnel we needed, and using local labor minimized the overhead,” Flanagan says. “We saved them 20 to 25 percent on the total job cost.”
From a design and construction standpoint, Atkinson says he couldn’t have been happier with the project.
“There was something great about just starting a golf hole without a piece of paper and figuring out what you wanted and needed to do on the fly,” he says. “I hope to do more projects like this because of the quality that resulted from field design. Sometimes we moved a little bit of dirt, decided after a couple of hours the hole wasn’t right, and then made a change in a different direction.”
Golf course superintendent Jeremy Christensen joined the construction crew in July 2005. Christensen came from Rochelle Ranch in Rawlings, Wyo., where he grew in the new 18-hole course.
“They had just seeded three holes and were getting started on the renovation when I arrived,” he says. “The big difference [between this project and the last one] was the design philosophy and amount of owner participation. Kevin would design the hole, look at it, make a few changes, and he and Darren would just work together on the final product. Jim Neiman did a lot of the dirt work, moving gravel and sand.”
A course blend
Although the two courses were built eight years apart, the renovations to the older nine helped reduce the number of differences between the older and newer holes.
“We changed some bunkers and added some additional bunkers on the front nine to match the back nine,” Christensen says. “The soil types are pretty similar. The new nine uses some of the newer bluegrass blends, which are a little darker, but most people will never notice the difference. The old nine has Penncross bentgrass greens, and the new nine has Pennlinks 2, so they’re slightly different texture. The older greens have a little more organic texture simply because they’re older. Otherwise, the two nines present little difference.”
Additionally, retrofitting the greens and tees on the old nine holes with dual-irrigation heads to match the new nine holes will help save water, a scarce resource in the arid West.
Pros and cons
Everyone involved with the project agrees the advantages of field design and combining the owner’s equipment and labor resources with specialized equipment and personnel far outweighed the disadvantages.
The only disadvantage of using inexperienced golf-course workers and construction equipment not specifically designed for golf course construction was the operators’ lack of knowledge concerning the importance of grade and how it ties into other areas, such as surface drainage, according to Flanagan.
But even course-construction companies working with only their own personnel will have newer workers with little specific golf-construction experience.
Another minor inconvenience was that a few operators could only work limited hours.
The most obvious advantages were design flexibility, cost savings and avoidance of administrative headaches associated with change orders.
Another advantage was having access to equipment that could be used for golf and road and residential projects that are an important part of the Golf Club at Devils Tower.
Goodwill generated within the community by using local labor and resources was another positive. An example of the goodwill that continued throughout the project was The Golf Course Co.’s decision to donate the construction of a running path along the main road for local high school and community use.
Future growth
The grand opening of the course was scheduled for July 15, which is when a conversion from a public to a private course with limited public play will begin.
Additional plans call for a nine-hole, daily-fee course designed by Phelps-Atkinson Golf Design. The start of construction on the third nine depends on future market conditions and sales of private memberships. Initiation fees will start at about $25,000.
Potential members and homebuyers generally are in awe of the new back nine and the renovations to the old nine, according to club general manager Mike Saye.
“We explain what we have done in terms of design and construction, and they really like the way things turned out,” he says.
So, too, do those who were directly involved with the project.
“This design and construction philosophy might not work perfectly on all projects, but it will work more often than most people think,” Atkinson says. GCN
Peter Blais is a freelancer writer based in North Yarmouth, Maine. He can be reached at pblais@maine.rr.com.
At a glance
Golf Club at Devils Tower
Web site: www.devilstowergolf.com
Location: Hulett, Wyo.
Course type: Semiprivate
Cost: $2.6 million for the new nine, $600,000 in renovations to the existing nine
Construction began: September 2004
Course completion: July 2006
Yardage: 7,020 from the back tees
Par: 72
Number of bunkers: 76
Average green size: 6,100 square feet
Greens: Penncross (front nine) Pennlinks 2 (back nine)
Tees: Bluegrass
Fairways: Bluegrass
Superintendent: Jeremy Christensen
Architects: Kevin Atkinson, Dick Phelps
Design firm: Phelps-Atkinson Golf Design
Builder: The Golf Course Co.
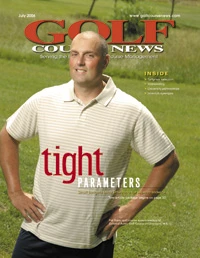
Explore the July 2006 Issue
Check out more from this issue and find your next story to read.
Latest from Golf Course Industry
- Advanced Turf Solutions and The Aquatrols Company release soil surfactant
- Heritage Golf Group acquires North Carolina courses
- Editor’s notebook: Green Start Academy 2024
- USGA focuses on inclusion, sustainability in 2024
- Greens with Envy 65: Carolina on our mind
- Five Iron Golf expands into Minnesota
- Global sports group 54 invests in Turfgrass
- Hawaii's Mauna Kea Golf Course announces reopening