No question about it. Doug Norwell will remember Summer 2010 as one of the hottest and driest on record. Throw in an unrelenting desert-style wind and it had the makings of a stressful season for the superintendent at The Camargo Club in Cincinnati.
Yet, because of a major retrofit in Spring 2009, Camargo, ranked one of the Top 100 Courses in the U.S., breezed through the heat wave with firm and fast turf that was green and playable until winter blow-out.
Across the country in Idaho, Adam Bagwell, CGCS, was confronted with a similar Sahara-like summer at the Crane Creek Country Club, a Certified Audubon Cooperative Sanctuary Course in Boise.
But in his high desert environment, Bagwell expects blistering summers with temps in the 80s and 90s and humidity less than 10 percent. That’s why he took action two years ago to update his irrigation system – and kept his fairways in picture-perfect condition, even with the summer heat, sandy soil and a pumping system that brings up well water with sediment.
So, what’s the magic wand that’s working for these guys?
Think nozzles. Solid metal sprinkler nozzles specifically designed to retrofit and upgrade Toro and Rain Bird golf heads.
Two years ago, Crane Creek was plagued with dry patches. Admittedly, the system was getting old. More than 1,200 heads were installed in 1996, chiefly Toro 734s and 760s. The heads were not performing well when Bagwell arrived at the course in 2007 and nothing seemed to solve the donuts and brown patches.
Bagwell checked the head spacing and ran pressure tests. He then started taking the sprinklers apart and discovered that the tail rotor sprays were plugged with sand and other small particles. He had a choice: rework the three-pump house system to include filtration, a major expense, or try a set of solid metal nozzles, which he had read about.
Improved Distribution Uniformity
“We initially ordered 100 Profile nozzles, based on recommendations from other superintendents. We installed them on our worst fairways and the results were apparent within a week. The Distribution Uniformity improved dramatically – the turf greened up and the dry spots disappeared,” he says.
Bagwell convinced his Greens Committee to invest $13,000 from his operating budget to gradually replace the sand-packed nozzles over the next two years. By the end of 2009, his crew had converted 950 full-circle and 45 part-circle heads to Profile nozzles and his Distribution Uniformity went from 67 to 74. Plus he saw water and energy savings.
“Once we eliminated the problem areas on the turf, we could optimize our programming schedule and make the system perform more efficiently. We were previously running the sprinklers 40 minutes at a time, irrigating greens and fairways on alternate days.
“We cut that back to 18-minute run times on alternate days at .79 inches per hour precipitation rate. Water consumption has been reduced by 40 percent, which I attribute to the Profile nozzles and better soil chemistry,” he says.
Also on the plus side, he lowered energy usage by approximately 25 percent.
“Our annual utility budget was approximately $43,000 a year. We trimmed that by nearly $8,000 because both our coverage and scheduling underwent major improvements,” says Bagwell.
A Real Cautious Guy
Meanwhile in Ohio, the historic Camargo Club, designed by Seth Raynor in the 1920s, is recognized as one of the prestige courses in the Midwest. In 1995, the entire irrigation system was replaced with Toro 730s, plus the course has the benefits of a filtered municipal water supply.
But that didn’t stop the donuts.
“The crew was constantly hand-watering to compensate for dry spots,” says Norwell. “It was very labor intensive and taking time away from other projects.”
He heard about Profile nozzles and gave them a try. “Initially, I ordered just eight,” Norwell says. “I’m a real cautious guy when it comes to spending money and making changes on the course.”
The new nozzles were switched into the Toro heads on just one hole, yet within a week the crew noticed a visible difference.
“After conducting a site evaluation and determining that the nozzles really did enhance distribution uniformity and overall conditions, we went ahead and ordered replacements for all 1,100 heads.
“Through Spring 2009, we retrofitted every sprinkler on the course….took us about four weeks.”
That same spring, however, turned out to be one of the wettest in a decade
But when Summer 2010 rolled around, the retrofit made all the difference between a reliably performing system and hand-watering hell.
“At Camargo we were able to stay on top of the situation with both the retrofitted sprinklers and wetting agents. There was no major loss of turf this entire summer,” he says.
Although Camargo has no water restrictions, Norwell’s team is very resource conscious.
“We try to stay in the forefront on water management and keep the course as dry as possible. It’s good for the turf and for the community.”
Back at Crane Creek in Idaho, the membership and Board of Directors took notice of the improved conditions and as the utility bills went down, they were pleased to give Bagwell the credit for initiating the nozzle switch-over.
“The board saw a real return on our investment,” he says. “The Profile nozzles paid for themselves within two years and the course has never looked better.”
Taking the “Leap of Faith”
Former USGA staff agronomist, Mike Huck, who currently heads up a golf course water management consulting firm, Irrigation & Turfgrass Services, had his own first-hand experiences with retrofitting a course with metal nozzles.
Before joining the USGA, Huck worked as golf superintendent at the Southern California Golf Association members’ club in Temecula, Calif., where Rain Bird 91 heads were in place.
He had a nightmare hole, Fairway No. 4, which challenged players with bayou-like conditions in the low spots and arid desert play in the high areas. The problem was so bad it affected germination of overseeded perennial ryegrass each season. Donuts only disappeared after substantial rainfall.
By chance, at a GCSAA Golf Show, he met David Malcolm, the engineer who invented the Profile nozzles. Malcolm decided to send Huck a trial set for Fairway No. 4.
“It was like putting in a new irrigation system,” Huck says of the retrofit project. “I became a believer overnight.”
During his travels with the USGA, Huck visited courses around the southwest, working closely with superintendents on coverage and pressure issues.
Among his toolbox of suggestions to improve DU and turf conditions were retrofits with metal nozzles. In fact, in one of his first USGA Turf Tips, Huck prepared a report that demonstrated how solid metal nozzles improved course conditions and contributed to turf health.
“For many years, superintendents were taught that head to head coverage was the only way to irrigate a course,” Huck says. “With more accurate data analysis and improve products, that’s not true any longer.”
Manufacturers previously did not mention much about Distribution Uniformity testing, Huck says, and did very little to promote the concept. Today, under pressure from water agencies and local communities, courses have become more aware of their resources and are focused on maximizing coverage.
“Consultants are looking very closely at the distribution patterns of individual sprinklers and use computers to analyze the data,” he says. “Irrigation is being fine tuned so that each head now produces a more efficient and consistent DU pattern, which is an excellent barometer of turf health.
“Donuts, brown spots, oversaturated areas disappear on courses that closely monitor their DU,” he adds.
Huck admits most superintendents are initially very skeptical about retrofitting every head on their course.
The question they always ask Huck is: “If they’re so great, why aren’t they factory installed?”
There’s a range of reasons why plastic nozzles are still the industry standard, he says.
“First, it costs much less to produce injection-molded plastic nozzles,” Huck says. “Solid metal nozzles would add another 10 to 15 percent to the cost of the heads, a difficult sell in these economically-challenged times.”
Many irrigation systems in the Midwest and East Coast can run seven to 10 years with plastic nozzles that perform reliably, Huck says.
“When the nozzles finally start failing, manufacturers would prefer to sell these courses new heads or an updated system, rather than suggesting nozzle retrofits,” he says.
Another reason why superintendents are reluctant to change out plastic nozzles is brand loyalty to the sprinkler manufacturer.
“However, it’s interesting to watch the conversion when a superintendent takes the ‘Leap of Faith’ and moves ahead with retrofitting the worst fairway on the course,” Huck says.
“Like true converts, they become the product’s best advocates and are often delighted to discuss their success with other professionals,” he adds.
The word-of-mouth about metal nozzles has spread over the last five years as golf course superintendents move to new courses and bring retrofit technology with them.
“A new superintendent is typically brought in as a problem-solver,” Huck says.”Since the board wants to see results right away, the superintendent has a good chance of convincing them at the start that retrofits are a viable option.”
Courses often work a retrofit program into their operating budgets for two or three years. This spreads out the cost and the nozzles can be installed in bite-sized chunks over the winters and early spring.
The price tag for a complete retrofit generally adds up to $13,000 to $15,000 for the Profile nozzles on a course with 1,000 heads, but the costs are typically recouped in water, labor and energy savings within two years, particularly in the southwest.
“When you figure that most golf sprinklers cost at least $125.00, it’s just 10 percent of the cost of the sprinkler to make it run like a well-tuned machine again,” Huck says. GCI
Nancy Hardwick is head of Hardwick Creative Services in Encinitas, Calif.
Solid Metal Nozzles: How They Work
Profile nozzles were introduced more than a dozen years ago by inventor David Malcolm and are manufactured by Underhill International, based in southern California.
The Profile nozzle line has been expanded to retrofit all popular Toro and Rain Bird golf heads. They provide both long-range and close-in coverage and are color-coded for easy field ID.
The Profile housings are constructed from solid brass and feature stainless steel orifices engineered to provide uniform distribution and reduce wind drift. Along with producing a main stream of water, the stainless steel insert has tiny notches pressed into the nozzle face, which strip away a small amount of water from the main stream, depositing it in close proximity to the sprinkler head. This produces the most uniform distribution of water possible, next to rainfall.
Primarily designed for golf courses, the metal nozzles operate reliably in sandy or rocky soil, as well as in clay or loam, and are designed to resist clogging from dirty water. The nozzles have undergone extensive laboratory testing at the Center for Irrigation Technology at California State University, Fresno, CA, along with field testing by superintendents at various sites. In all cases they demonstrated improved Distribution Uniformity and overall water and energy savings.
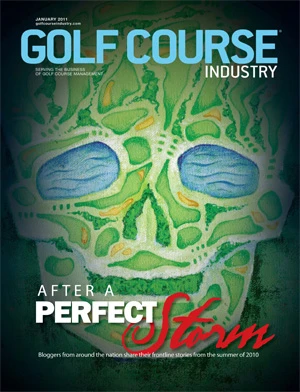
Explore the January 2011 Issue
Check out more from this issue and find your next story to read.
Latest from Golf Course Industry
- From the publisher’s pen: Technology diffusion and turf
- Applications open for 2025 Syngenta Business Institute
- Smart Greens Episode 1: Welcome to the digital agronomy era
- PBI-Gordon promotes Jeff Marvin
- USGA investing $1 million into Western Pennsylvania public golf
- KemperSports taps new strategy EVP
- Audubon International marks Earth Day in growth mode
- Editor’s notebook: Do your part