Erik Sides sees it time and time again.
Golf crews think they’re doing something good when they meticulously wash off a mower after use, sometimes every day. But they don’t realize the harm they could be doing to the mower’s electrical components.
“Washing the mowers is great, but a lot of times they’re using an irrigation line with irrigation water pressure which is really high with a huge amount of water,” says Sides, executive director of the Equipment & Engine Training Council. “If they spray the instrument panel area where the key and PTO switches are, water intrusion into those switches could cause a ‘no-start’ condition down the road.”
Another issue, Sides adds, occurs when the source for water typically used for washing is reclaimed water high in sulfides and salt, which can wreak havoc on metal and cause corrosion.
“It may not happen right away, but a week or a month down the road, you have a no-start condition because the contacts in the key or PTO switch have been corroded,” says Sides.
Keeping washing to a minimum allow golf crews to avoid having to troubleshoot no-starts down the road, says Ron Laurita, product and technical manager for Jacobsen.
“We recommend washing only once a week and blowing them off with air the rest of the time,” Laurita says. “Limit the water to the cutting units and air blow the actual machine. If you want to hand wash, fine, but we don’t recommend pressure washing because it promotes more problems.”
Washing aside, the No. 1 problem Laurita hears about at his call center is that the unit won’t “start” or “crank.” The cause is usually related to battery cables that have molded terminals, which can corrode over time. However, since these terminals are molded, you can’t see the corrosion.
“Probably the easiest thing you can do to eliminate that is to take a pair of cutters and cut that molded terminal off, strip the wires slightly and put one of those clamp-on style replacement battery terminals on the wire, which will give you a new area to which you can connect the cable,” Laurita says. “And the average guy can do that.”
The good book
“A lot of times, the operator book will have plenty of information even for a novice to go through and read and troubleshoot some things,” says Eric Sides, executive director of the Equipment & Engine Training Council. One of the best ways to head off improper operation issues, says Tracy Lanier, product manager, John Deere Golf, is to have a good understanding of how, for example, a greens mower is supposed to operate. She calls this understanding “what’s normal” with the operation, and reading the operator manual is key. “You can prepare ahead of time by spending time reading the operators manuals and becoming familiar with the machine,” Lanier says. “Knowing where the operator manuals are stored is also very helpful when the technician is not around to help answer the question.” Reading the operator manual, for instance, would help avoid the tendency to leave marks on the green, tear up the hill or slip while going up a hill. How? By understanding what the proper tire pressure is. “You ask, ‘Why is there 26 lbs. of air in this tire?’” says Ron Laurita, product and technical manager for Jacobsen.. “And they say, ‘Well, it didn’t look right.’ It’s only supposed to have 10 lbs. of air, but they overinflate it because they only gave it the eye test. It’s always good to verify with a tire gauge.” |
Another common problem has to do with hydraulics. Following proper filter change procedures, Laurita supports the old adage: “An ounce of prevention is worth a pound of cure.”
“Your most important hydraulic filter change is in the first 50 hours of use,” he says. “The reason is because every single component on that machine is tight and has to break itself in, and you’re going to get the most metal contamination in a hydraulic system within the first 50 hours.”
Sides sees hydraulic leaks all the time, typically from golf crews not having a routine preventative maintenance schedule in place to make sure there is no hose damage.
“I’m out mowing and all of a sudden a hose bursts and I have oil all over a green or tee box,” says Sides. “A lot of that is preventable through either a daily or weekly inspection of hoses.”
The main hoses to watch are the ones responsible for moving reels and decks up and down, Sides says. For four-wheel drive machines, it can be hoses for the rear wheels because those wheels are always moving left-right-left-right.
Hose issues are fixes that are typically done in the field, Sides says. “Before you get it back to the shop, you’ll either a) have to go out and tow the piece of equipment back in slowly, or b) fix it in the field. But a lot of times, it’s, ‘The mower shut off while I was mowing.’ A seat switch or a wire has fallen off because it got grabbed by something. I typically don’t like operators trying to diagnose an issue – it’s best to leave it up to someone who knows the machine in and out, knows the safety circuits and has the skills to do the repair.”
Another thing best left to a trained technician is anything that requires opening into or removing a fitting from a hydraulic circuit. “That’s something someone who doesn’t know what they’re doing doesn’t want to get involved with,” Laurita says. “You can introduce contamination into the system without realizing it. Also, let’s say you want to work on the cutting units and they’re up in the air and have a leaky cylinder. The first thing the guy does is crack a fitting loose. Well guess what? All that pressure is up against that fitting, and now he shoots oil on himself.”
A “hole” other machine
“Whether it’s a supervisor, mechanic or superintendent, they should be informed that something is wrong – because they could tear up where they’re aerating or, mechanically speaking, they could further damage the machine,” Sides says. “If it comes out of time, you have pieces that could hit together and break and cause some severe damage.” One might think that, because aerators are simpler than mowers, they can be fixed by nearly anyone. But Ron Laurita, product and technical manager for Jacobsen, disagrees. “Even though aerators are slightly simpler without sophisticated electronics, there are a lot of moving parts – chains, sprockets and belts – to get all that reciprocating motion,” he says. “It’s important to keep the contamination out of that, too. If you take care of the little things, the big things will take care of themselves.” |
When it comes to electronics, Laurita sees a tendency for operators to blame the electric controllers or computer system on the machine because it’s a “big black mystery box they don’t understand.” Very rarely, though, is that the cause of the problem.
“It’s usually something simple, so I always recommend starting with the simple things first because nine times out of 10, it will be something simple: batteries, filters, cables, connections, etc.” he says.
Even so, sometimes there are electrical issues, most commonly with safety circuits, says Tracy Lanier, product manager, John Deere Golf.
“This can be easily diagnosed on our 2500B PrecisionCut and 2500E E-Cut riding greens mowers with our ‘Sit on Seat’ on-board diagnostics system,” Lanier says. “This system, along with our white-box controller, can be quickly checked to solve these issues. The information to help with the troubleshooting is located in the operator’s manual.”
The Toro Company stresses that customers should not try to “wing it” when addressing and remedying equipment issues in the field.
“With any mower problem, large or small, if the on-site mechanic is unavailable, it’s very important for the superintendent to contact the distributor as the next course of action,” says Greg Hollahan, technical service systems manager at Toro. “We recommend using caution in allowing just anyone except for authorized mechanics to service the equipment. They may not be familiar with a product’s safety systems and could inadvertently disable it; that could lead to dreadful results.”
But when it comes to preventative maintenance, a key to avoiding potential equipment malfunctions in the field, Hollahan believes those responsibilities can be handled by other staffers as well.
“The first step would be to locate the golf course’s preventative maintenance procedures manual,” he says. “It’s crucial to continue to perform preventative maintenance in the absence of a mechanic. The manuals are typically centrally located and easily accessible to all golf course personnel so that anyone can see what machines need maintenance on any given day. The mechanic would look at that and evaluate what needs to be done that day. However, this process can be managed by other course staff members as well.”
Playing the sleuth
“You must ask the right questions, because a lot of times you don’t want just yes or no answers,” says Sides. “You have to have some questions you’re asking specifically to get answers to find out what happened. For example, if the operators just says, ‘It doesn’t work,’ I don’t know anything and I go out there blind. But, to get to the root of the problem, I can ask, ‘Did it shut off on you?’ ‘Where were you when it happened?’ ‘How long have you been out mowing?’ ‘Does it happen when it’s hot or is it happening when it first starts up?’” John Deere’s Tracy Lanier agrees some issues may require the operator to explain what they were doing or attempting to do when the problem occurred. “This, along with your understanding of what’s normal with the operation, can help you quickly determine the issue,” she says. Adds Toro’s Greg Hollahan, technical service systems manager, interviewing the operator is “absolutely vital to the troubleshooting process. The operator should be able to describe sounds, smells and even the mowing environment like hillsides or obstacles at the time of the issue. A step-by-step narrative of the incident can help piece together what might have been the contributing factors to the breakdown.” |
Jason Stahl is a Cleveland-based writer and frequent GCI contributor.
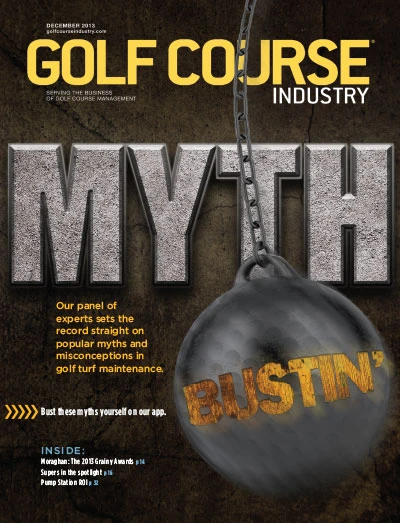
Explore the December 2013 Issue
Check out more from this issue and find your next story to read.
Latest from Golf Course Industry
- The Aquatrols Company hires marketing manager
- Renovating Bredemus in West Texas
- Renovation starts at Okatie Creek GC at Sun City Hilton Head
- The Fittest Podcast in Turf: Episode 1
- New 6-hole course debuts in Oklahoma
- GCSAA announces Grassroots Ambassador Leadership Award recipients
- Reel Turf Techs: David Gummo
- PBI-Gordon promotes two to executive level