![]() |
Since the beginning of the “Great Recession” architects and manufacturers have been touting reduced cost as a benefit of renovation programs. Just last year, both Bob Lohmann and I wrote about the emphasis on “cost benefits analysis” of proposed course renovations. Since then, I have been monitoring renovation “payback” results of my and other projects. The result is a mixed bag. Perhaps not surprisingly, the actual results aren’t always quite as stunning as the promise of savings and it turns out to be harder to save money than we originally thought. I cited a California resort that sought to reduce turf and irrigation, because of a $1 million water budget. They reduced turf by 30 percent, but have had less than expected water savings. Given that most of the 30 percent turf reduction was in less intensively irrigated rough areas, rather than fairways, tees or greens, potential savings were less than a direct ratio of turf reduction. In addition, they simultaneously sand capped fairways to improve their quality, but that required more water. As a result, there were nominal water cost savings. Another superintendent has been slowly converting his old 80-foot spacing double-row system to a triple-row spacing at 65 feet. By conventional wisdom, the tighter spacing should have allowed drier, more consistent conditions using less water, but his eyes tell him the results are no different, and his water logs suggest he isn’t saving very much water. Similarly, modern, 25 percent more electrically efficient pump stations haven’t always translated to lower electric bills. While it’s true they use less electricity on an apples-to-apples basis, the reality is electrical consumption is often determined by “use charges” that kick in with every pump start, negating the tactic of starting pumps only when necessary. These vary among utility companies, so your situation might vary, but every superintendent needs to become familiar with how their power providers calculate rates and charges. Moreover, irrigation designers now specify significantly larger pumps, to reduce the “industry standard” irrigation water window to six hours, rather than 8-9 hours. Doubling the traditional pump size often offsets the 25 percent increase in electrical efficiency. One superintendent lengthened his watering schedules and found that used less electricity. Even then, with annual rate increases, it was discouraging that the bills merely held steady for a few years. Nonetheless, many courses feel as if new irrigation does provide payback. As the old saying goes, if the superintendent spends more time fixing the system than using it, it is usually time for a change. In some cases, the lack of savings comes from using the watering efficiencies gained from replacing old systems to water more area, which is a goal in many cases. There can be solid payback from drainage improvements where regular rains close the course frequently. One course experienced 4-5 day closures 7-8 times a year, losing 15-20 percent of available tee times. At 30 days, 200 rounds per day, and average fees of $25 per golfer, poor drainage demonstrably reduced revenues $150,000 annually. At current municipal bond rates, those reasonably projected revenues would fund millions in drainage. Related improvements, like cart path expansion from partial to full loops, which helps play get out even faster after rains, and to a lesser degree, curbs, which save the labor of roping off areas regularly also added to the bottom line. Generally, great drainage provides nothing but improvement all around, although some will claim it leads to newer, higher maintenance turf varieties, which can increase costs. In fact, we usually do find courses that are remodeling to make up for years of deferred maintenance also need expanded equipment lists and newer maintenance methods. While my examples are not a comprehensive state of the industry survey, or intended as any indictment of current practice, it is a reminder that even all the new weapons in our cost savings arsenal, without thoughtful design, we may “cancel out” good intentions, and those will only shoot us in the foot. Making the best of new technology requires more catchy names and marketing slogans. I don’t sense golf course architects and irrigation designers are truly walking the “cost-savings walk” because most clubs and courses don’t demand it, and still focus on matching the high maintenance standards seen on TV. Until that attitude changes, superintendents will have to rely on their skill, imaginative work arounds, and hard work to stay within ever tightening maintenance budgets. Then again, what else is new? |
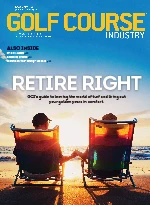
Explore the December 2012 Issue
Check out more from this issue and find your next story to read.
Latest from Golf Course Industry
- Heritage Golf Group acquires North Carolina courses
- Editor’s notebook: Green Start Academy 2024
- USGA focuses on inclusion, sustainability in 2024
- Greens with Envy 65: Carolina on our mind
- Five Iron Golf expands into Minnesota
- Global sports group 54 invests in Turfgrass
- Hawaii's Mauna Kea Golf Course announces reopening
- Georgia GCSA honors superintendent of the year