![]() |
Commercial-grade or consumer-grade?
This is the most basic choice when deciding to purchase handheld power equipment for golf course maintenance. As every maintenance property is different, it is important to first evaluate which type of equipment will better fit your operation to determine the best buy.
At Kansas City Country Club, spending the extra money upfront to buy commercial-grade power equipment is the best choice since we are a park-style golf course that has approximately 2,500 trees on the property. As a result, a large amount of time is spent on leaf clean up, trimming and maintenance of our tree inventory. Having a reliable and durable fleet of handheld power equipment is vital to completing the day-to-day maintenance at our club.
Our fleet of power equipment consists of approximately 10 backpack blowers, 10 string trimmers and seven chainsaws. We try to stay consistent with the same brand. Generally speaking, we try to get three to five years of use out of each piece of equipment and replacement is determined by when the repair cost exceeds 40 percent of the equipment cost.
A big key is to have a fixed budget line to replace equipment to ensure reliability of the fleet of power equipment.
Keys to handheld equipment Evaluate what equipment best fits the requirements of your course. Will a qualified mechanic be on hand to maintain the equipment? Are parts readily available? If no to either of these questions, then perhaps a one-season, "disposable" unit is more appropriate. Replace a unit when the repair cost exceeds 40 percent of the equipment cost. Before disposing a worn out unit, evaluate any parts that can be recycled for future use. |
A qualified mechanic on staff at your course is essential when dealing with the preventative maintenance that is involved with keeping commercial grade power equipment working as long as possible. Our mechanic has been in the mechanics industry for more than 30 years; he prefers commercial grade equipment because in general, it just lasts longer than residential-grade equipment. Commercial-grade equipment is built specifically for everyday use where residential is designed for use one to two times per week.
Another plus with commercial equipment is that it often has more serviceable parts and replacement parts can usually be easily obtained through local licensed service dealers. These dealers generally require certified mechanics be on staff to help out with any issues with the brands they carry. Residential grade equipment is often constructed with a lot of molded parts and can be much harder if not impossible to service.
Preventative maintenance for a mechanic is also easier when dealing with commercial grade equipment. The main repairs are usually in two groups, mechanical and operator use. The mechanical portion includes filters, spark plugs and other expendables that will usually last a season with an occasional light cleaning. Blades, bars and chains need to be checked periodically depending on use and replaced when necessary. The second group of maintenance is dependent on the operator. It becomes a struggle to keep equipment running properly if you have an operator who is abusive to and who does not take proper care of the equipment. Examples include a broken throttle cable or deteriorated fuel line, this type of breakdown happens maybe a couple times a year on a 1- to 2-year-old piece of equipment. Costs can be minimized by performing quick inspections during the busy season and more detailed inspections in the off season which will give you a more intense look into your equipment.
When the equipment is no longer economical to use we try and reclaim parts that can be used on our other pieces of equipment. If this cannot be done then the item is recycled or discarded. When your fleet is of the same brand it can be of benefit to save some used parts off of an old machine and also gives the facility the ability to use up parts inventory on the remaining equipment that is still in use. This is another way to keep expenses to a minimum on your inventory.
Andy J. Klein is assistant superintendent at Kansas City Country Club in Mission Hills, Kan., and is a frequent GCI contributor.
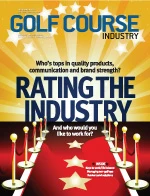
Explore the December 2011 Issue
Check out more from this issue and find your next story to read.
Latest from Golf Course Industry
- Golf Construction Conversations: Reed Anderson
- ’Twas the Night Before Christmas (on turf)
- Twas the Night Before Christmas (the turf version audio)
- Advanced Turf Solutions and The Aquatrols Company release soil surfactant
- Heritage Golf Group acquires North Carolina courses
- Editor’s notebook: Green Start Academy 2024
- USGA focuses on inclusion, sustainability in 2024
- Greens with Envy 65: Carolina on our mind