All of the ideas used in my Travels with Terry column over the years have been fantastic, partly because these innovative ideas each proved to make their golf course maintenance staff more efficient and productive.
I was asked to choose the best of the best, and let me tell you, this was no easy task. Enclosed are my Top 10 great ideas from Travels with Terry from the past six years. – Terry Buchen
July, 2005
Bel-Air Country Club
Los Angeles, Calif.
Brian T. Sullivan, CGCS, MG
Ernie Hernandez, assistant
John Nachreiner, assistant
"Terry Says"
Sullivan and his assistants removed the front bumper from the Club Car utility vehicle, installed a steel plate with two pieces of 2-inch square tubing, welded some 1 1⁄2-inch square tubing onto their Billy Goat push-type blower, drilled bolt holes in the square tubes, slid the blower-mounted square tubing into the vehicles square tubing and then bolted or lynched-pined it in place. No more pushing the blower or hand raking leaves with this simple but extremely effective and efficient way to make better use of their existing labor force. When not in use, the blower is removed, two pieces of 1 1⁄2 x 1 1⁄2-inch square tubing was installed on the inside of the bumper, which was then put back in place and held with bolts or lynch pins. All of the parts were in stock and it took about three hours to design and build.
March 2006
Delaire Country Club
Delray Beach, Fla.
Brian Bowles, superintendent
"Terry Says"
To rake the fairway bunkers real smooth without any rake furrows, Bowles uses a 36 x 76-inch corded rubber slotted drainage mat pulled behind a Toro Sand Pro riding bunker rake. The OEM rake teeth where removed from the riding bunker rake and the remaining five individual feathering rakes were left in place. The rubber mat was bolted on top of the rake mechanism and is rolled-up when transporting in-between bunkers. The three knobby OEM tires were replaced with smooth triplex greens mower tires to keep the bunker sand as smooth as possible. The rubber mat is available from www.mcmaster.comwww.mcmaster.com. The rubber mat cost about $150 and it took about one hour to mount.
October 2006
Salina Country Club
Salina, Kan.
Mike Hulteen, CGCS
Leland Davis, equipment mechanic
"Terry Says"
Why walk when you can ride in a good old-fashioned "sulky" behind a walk-behind greens mower. 11⁄2-inch square metal tubing is used for the frame and supports, and 3⁄8-inch flat steel is used for the seat post, which is bolted and welded to the frame. The pneumatic tires and wheels are replacement for wheelbarrows and the special U-shaped receiver intersects with a flat piece of steel with a hole drilled into it for a bolt to hook it up to the mower. Most of the materials were already in stock and it cost about $100 in additional materials. It took about five hours to build.
July 2007
The Club at Admiral's Cove
Jupiter, Fla.
Bill Brousseau, director of golf course maintenance
Jim Matis, equipment manager
"Terry Says"
The engine on the Buffalo Blower had to be replaced and Matis used an old John Deere 2653 Utility Triplex Hydraulically Operated Reel Motor instead. The hydraulic motor was hooked-up to one 10-inch diameter and one 3-inch diameter pulley and the two hydraulic motor hoses were hooked up to a two-spool hydraulic coupler on the back of a John Deere Pro Gator. The engine battery is used to change the blower nozzle direction, as it is hooked up to the alternator on the tow vehicle with pig tails to keep the battery charged at all times. The blower RPM's are changed as needed by changing the ground speed of the tow vehicle with the throttle lock when desired. The blower is significantly quieter than when it had an engine and it saved the club over $2,000 for a new engine. The used real motor cost $65 and it took about eight hours to build.
September 2008
The Silverleaf Club
Scottsdale, Ariz.
Jeff Prichard, CGCS, director of agronomy
Kent Coburn, superintendent
Bruce Leonard, equipment manager
"Terry Says"
The maintenance staff has to travel 1.7 miles to the first tee and over 2 miles to the farthest green from their turf care center. Coburn and Leonard came up with idea to transport their John Deere Aerocore 800 and Toro green's aerifiers to save valuable time and wear and tear on the machines. The square tubing, wire mesh, golf cart wheels and tires, axle kit, expanded metal and scrap metal cost about $575 each and it took about 40 hours to build the first trailer and 20 hours each to build the second and third trailers.
Editor's Note: All superintendents and personnel reflect their respective positions at the time of the original publication.
December 2008
Muirfield Village Golf Club
Dublin, Ohio
Paul B. Latshaw, MSN, CGCS, director of grounds operations
Jake Gargasz, superintendent
"Terry Says"
To keep wear and tear from the walk-behind greens mowers turning on the collars, these 30 x 60 x 1⁄4-inch HDPE plastic sheets placed end to end on the collars do a great job of protecting them. Four handles are cutout with an electric jigsaw so the operator can move all three easily from one end to the other as each green is being mowed. The plastic pieces cost less than $50 each, they are available from kitchen countertop stores and the labor time is about 15 minutes each to cutout the four handles.
June 2009
The Members Club at Grande Dunes
Myrtle Beach, S.C.
Scott Grumman, superintendent
Jon Stewart, assistant
Joe Corsetti, equipment manager
"Terry Says"
A great idea for towing a John Deere Aerocore 800 green's aerifier behind a turf vehicle to save the operator walking time in-between aerifying greens. The tow bar design uses tubular and flat steel welded together that is attached to the tow vehicle with a hitch and pin with a chain so the pin won't get lost. The other end is attached to the aerifier with a U-shaped metal bracket held in place with two lynch pins that connects/disconnects quite easily. This model aerifier has a neutral free-wheeling shift lever and it can be towed up to 10 MPH. The materials cost about $65 and it took about 3.5 hours to build.
August 2009
Butterfield Trails Golf Club
El Paso, Texas
Joe Perez, head mechanic
Nick Guillen, assistant mechanic
"Terry Says"
To increase the life of the eight conventional-type street brooms on this John Deere TC 125 collection system, Perez and Guillen designed and built 1 x 1 inch thick pieces of oak wood "spacers" bolted to the top end of each broom to compensate for wear of the bristles. This great idea saves about $100 per set of four brushes, $200 total in replacement costs. The materials cost about $15 and the total labor time was approximately one hour.
January 2010
Town & Country Club
Saint Paul, Minn.
William R. Larson, CGCS, superintendent
Ryan Browning, assistant
"Terry Says"
The first-ever Smart Board Interactive White Board in the golf industry was placed in the employee lunch room/meeting room. It is operated in conduction with an LCD projector mounted from the ceiling and a dedicated computer equipped with the necessary software to allow the interactive white board and computer to communicate. Instead of using a "mouse," the screen is operated with the touch of a finger, similar to interactive television boards used on CNN, etc. The Smart Board (www.smarttech.com) can do any function just like a computer monitor, it is totally interactive and it can operate exactly like a dry erase board on a conventional white board using four different colored electronic pens along with an electronic eraser pad. It is used as a daily job assignment board, for training videos, going onto the internet and doing any other computer function interactively. They range in size from 48 inches to 94 inches and Larson choose the 88-inch model costing about $8,000, which includes installation and wiring. The dedicated computer & monitor cost extra.
October 2010
South Hills Golf & Country Club
Fond du Lac, Wisc.
Jim VanHerwynen, CGCS, superintendent
"Terry Says"
A much easier way to eliminate hand raking of leaves and putting branches into piles where the idea actually came from a superintendent's dream. The Hanheraker uses seven Union Tools plastic fan-type leaf rakes that are two feet wide with squared-off bottoms that are attached to the plywood (with muffler clamps) that has a 30-degree angle. Two large springs provide resistance when needed and one of VanHerwynen's employees named the rake after him. Many of the parts/supplies are already in inventory. The rake heads and muffler clamps cost about $80 and it took about four hours to assemble.
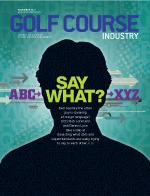
Explore the November 2011 Issue
Check out more from this issue and find your next story to read.
Latest from Golf Course Industry
- Golf Construction Conversations: Reed Anderson
- ’Twas the Night Before Christmas (on turf)
- Twas the Night Before Christmas (the turf version audio)
- Advanced Turf Solutions and The Aquatrols Company release soil surfactant
- Heritage Golf Group acquires North Carolina courses
- Editor’s notebook: Green Start Academy 2024
- USGA focuses on inclusion, sustainability in 2024
- Greens with Envy 65: Carolina on our mind