Today’s water management software comes loaded with myriad bells and whistles. But are superintendents leaving important cards on the table by overlooking some potentially useful applications?
Randy Mills, product manager, golf controls at Hunter Industries, says ET-based irrigation – with EvapoTranspiration being supplied by a weather station – and pick lists as a couple prime examples of technology not being utilized to its fullest.
“Weather stations are popular and watering by water depth is popular, but most people want to look at the weather station ET, then use their own number,” Mills says. “When properly configured, it is possible to allow an irrigation system to almost totally manage itself with the superintendent just confirming the value.”
The superintendent would probably need to make adjustments in some cases where ET is not the overriding factor in determining runtimes, Mills adds.
As for best using pick lists – a table containing a display of common runtime or ET adjustments – Mills considers this a time-saving feature in the software. After assigning entries to groups of stations, superintendents only need to change one number to apply a change to specific groups.
For example: Wind causes increased evaporation, therefore, moisture in that area is depleted more quickly than other areas, which is the same as saying the ET is higher. If a course has traditionally windy areas, a pick list value called “WINDY” can be created. Any sprinkler tagged as WINDY will automatically run 10 percent longer (110 percent) than the weather station says.
“The power of the pick list is that you may eventually have 30, 50 or more sprinklers identified as being in windy areas,” Mills explains. “If you decided 110 percent was too low and you wanted to increase the setting to 120 percent, it would take a long time to make the same change to 50 sprinklers. Instead, because the pick list was used, only the pick list value needs to be changed and instantly, all sprinklers identified as ‘windy’ will run 20 percent longer.
“Allowing your weather stations to have almost complete control over your irrigation system also saves time, but perhaps more importantly, it gives the superintendent extremely fine control over how wet or dry he keeps the course,” he adds. “Once the system is ‘tuned’ to the weather station, you can dry the course out by changing one or maybe a couple of numbers. When you want it a little wetter, the same thing is true.”
Paul Roche, national sales manager for golf at Rain Bird, points to “Temporary Station Adjust” as a key feature often overlooked in central controls. This allows a superintendent to identify areas and sprinklers that either require a little more or a little less water and adjust an irrigation program (runtime/application rate) for a predetermined period of time before defaulting back to their regular run time/application rate.
“Without this feature, adjustments were typically made on post-it notes and index cards as reminders to make readjustments in the future,” Roche says.
Other overlooked features, according to Roche, include:
- Dry Run. Ensures the system is optimized to reduce pump station cycling and maximizes flow management;
- Pump station profiling. Setting maximum flow limits throughout the day to stay within utility company Demand Charge restrictions; and
- Cycle-Soak. Allows a superintendent to set the maximum runtime/application rate on an area, then wait a period of time for percolation before turning the station on again.
“This is ideal for sloped areas or heavy soils where runoff may occur, or on areas that sod or seed is being established, and the irrigation system manager wants to continually wet an area,” he says.
Lack of time and hectic schedules factor in many functions being overlooked, Roche says. The need to keep software updated when renewing central control system service plans also plays a role, he adds.
Use It or Lose It Does an unused function become obsolete? Both Hunter Industry's Randy Mills and Rain Bird's Paul Roche balk at the notion that certain functions have become so underutilized that they’ve become obsolete. “We don’t see these functions becoming obsolete at all,” Roche says. “These features have been asked for by irrigation system managers and added to software at their request. We routinely see irrigation system managers rediscover software functions and incorporate them into their daily routines.” “To me, something becomes obsolete when it used to be used all the time and over time its use has gradually dropped until it stops being important,” Mills adds. “The only things I can think of which fit into that category are features which support irrigation equipment which is rarely used nowadays. For example, there are features designed to help you work with fixed-drive pump stations. Fixed-drive pump stations are disappearing – they are being replaced with VFD (Variable Frequency Drive) pump stations. Eventually there won’t be any more fixed drive systems, so those features will be unnecessary. “Most underutilized features I can think of would truly benefit the superintendent,” he adds. “Pick lists, for example, save a lot of time when adjustments are needed.” |
Mills stresses education, refuting the notion that allowing a weather station to automatically update sprinkler runtimes is underused because it is simply not trusted.
“I believe the real reason this capability is not used is because it is not well understood,” he says. “Weather stations and ET are both well understood, but what actually happens to turn an ET value into a runtime and especially, how to ‘tune’ your system in to match your golf course is not understood.
“Pick lists are not used because they are not well understood,” Mills adds “They are not prominent enough in the software and we have not done a good enough job training people to use the feature.”
The use of pick lists are something that needs to be better emphasized when people are trained on the software, according to Mills, while an intermediate step is missing with weather stations/ET.
“Most superintendents water based on straight minutes of runtime,” he says. “After years of seeing the weather, picking runtimes and seeing the result, they become very good at choosing the correct runtimes, though they often tend to err on the side of too wet as opposed to too dry. Changing from minutes of runtime to inches of water is difficult, No. 1, because they are completely different kinds of units, so it is important for the software to have a way of showing sprinkler runtimes for a given ET. The second problem is most of the time, the way weather stations have been configured, calculated runtimes do not match the runtime the superintendent wants to use, causing distrust in the value.
“To address this problem, the software needs a way for the superintendent to enter the runtime he wants (which is usually very close to the correct one), then the software needs to calculate an adjustment factor to be applied to the weather station ET so the resulting runtimes are automatically adjusted to the minutes the superintendent expects,” Mills says. “Over time, the superintendent will see that the weather station is automatically calculating runtimes that fit his expectations and he will spend less and less time making changes to the computer.”
At Rain Bird, staying current on a Global Service Plan (GSP) entitles users the latest version of software. Bulletins and updates are mailed and emailed to keep superintendents up to date on the latest features.
“Irrigation distributors are also a great resource to point out some of the latest and most used features,” Roche says. “On the manufacturing side, annual software classes are offered around the country. It’s always a good idea to attend every few years or attend a local distributor’s workshop.”
For those looking to better utilize their irrigation systems, Roche recommends education.
“We strongly suggest [superintendents] attend software workshops every few years to keep abreast of the latest technology and to rediscover some existing functionality they may not realize they have,” he says. “Irrigation distributors are also a great resource for how software is being used and what features other managers are using. Global Service Plan representatives are also available for software questions and to answer ‘how-to’ questions.”
Mills agrees that checking with the distributor or manufacturer is a good idea, but also suggests tinkering with the system when the opportunity arises.
“First, make sure you know exactly how to backup and restore your system database,” he says. “Then, find some time to play around with it a little. If you make a backup right before playing with it, you can try anything you want and there is no risk of messing anything up.”
Rob Thomas is a Cleveland-based writer and frequent GCI contributor.
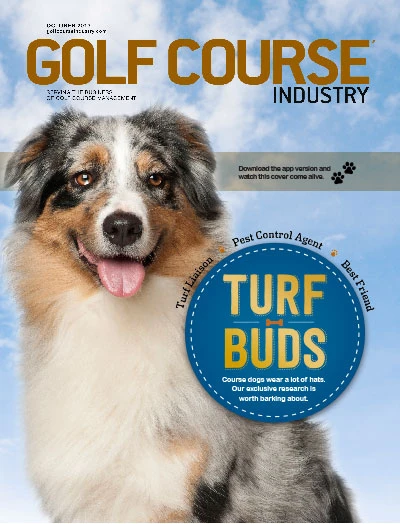
Explore the October 2013 Issue
Check out more from this issue and find your next story to read.
Latest from Golf Course Industry
- Heritage Golf Group acquires North Carolina courses
- Editor’s notebook: Green Start Academy 2024
- USGA focuses on inclusion, sustainability in 2024
- Greens with Envy 65: Carolina on our mind
- Five Iron Golf expands into Minnesota
- Global sports group 54 invests in Turfgrass
- Hawaii's Mauna Kea Golf Course announces reopening
- Georgia GCSA honors superintendent of the year