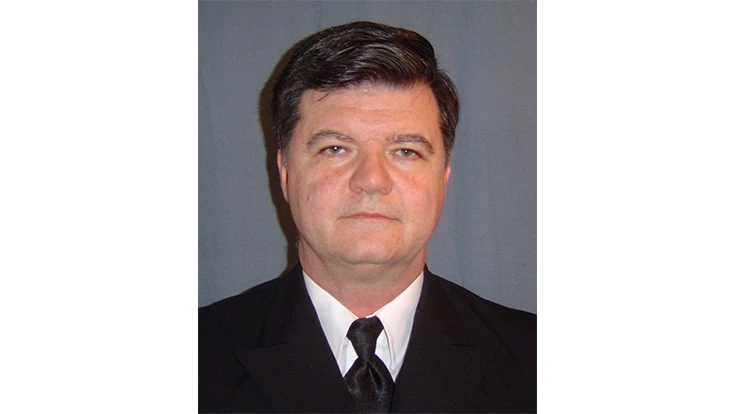
|
Heading into the fall season, here are a few best practices I’ve observed and adopted along the way. Now is as good of a time as any to share them with you as you prepare to either put your equipment to bed for the season, or to kick start your equipment maintenance program for the months to come. GreasingGreasing is an art that costs a lot of bearings to learn and is time consuming to do. A fairway mower typically has 57 zerk grease points. If I spend one minute on each zerk, refill the grease gun and replace bad zerks, the greasing task takes over an hour for one mower. Manufacturers suggest that the mowers should be greased periodically and after each time they are washed. Since the mowers are washed every day after mowing, they should be greased every day — an impossible situation in a one-man shop. Luckily, maintenance is changing. I have been switching to lifetime-lubricated sealed bearings for high speed rotating parts and to plastic bushings for low speed parts eliminating the need for greasing. Some manufacturers are making the same changes. Eliminating greasing also prevents the two most common causes of bearing failure: under greasing and over greasing. The lifetime of a bearing varies depending on how it is used and abused. Plastic bushings are a blend of plastics and fibers that act as a solid lubricant that cannot be washed away or affected by water. This is ideal for the mowing environment which is wet with grass juice, dew, wash water and rain. Plastic lasts longer than greased bronze bushings. Air and oilSome mowers came with “clogged air filter indicators” that worked so well I ordered more as repair parts and added them to other mowers. The indicator lets me know when it is time to change the expensive air filter based on performance rather than appearance. The indicators pay for themselves by eliminating unnecessary air filter changes. After reviewing the maintenance manual for every mower in my motor pool, it looks like the best plan is to change their crank case oil and filter every 100 hours. I also found that 10w30 was an oil option they had in common, so I streamlined the inventory by becoming a one-oil shop. Some mowers reach 100 hours in a little over a week, others every couple of weeks, which means I am doing oil changes almost every day. To deal with this flow of used oil, I built a 55-gallon roll around oil collector with a large funnel, a drain board top and a pump to transfer its contents into the 300-gallon tank outside. A used oil dealer empties the big tank for “no-credit, no-charge.” I get the new oil and filters from NAPA at a special price. Their quart bottle price is actually lower than buying oil in bulk.
RepairsParts wear out over time and need to be replaced or built up with weld. Weak spots in the mowers are discovered and need to be reinforced. Hydraulic hoses age and need to be replaced. Fortunately, the hose shop makes them while I wait. When steel lines fail, I replace them with hoses for a fraction of the cost. Minimalist recordsBecause there are no departmental reporting requirements, the only records I keep are the ones I need for myself. They include a large cardboard master list of each machine I am responsible for and its equipment number, my worklog where I write each maintenance action along with the engine hour meter reading when it happened, a phone list and a strip of blue carpenters tape stuck next to the engine hour meter on each machine. The tape says when the next oil change is due. In the engine compartment of each mower, I have marked what filters it uses, how many quarts of oil it takes, which side the drain plug is on and its wrench size. Oil filters I stock are arranged on the shelf by NAPA number and are marked with what mower they are for. Each time I use one, I put it on my shopping list. My worklog is my personal record of what I do each day. I buy the book out of my own pocket so that it is not company property. It is a 400-page record book, and I have a page for each day. Having been lost in a sea of sticky notes, I have made it a personal rule to not use them anymore. Instead, I write everything that I would have written on a sticky note into my worklog. The pages are numbered and dated so specific pages can be referenced. Each phoned-in parts order is written in my worklog. Parts orderingI keep very little inventory in stock since we are close enough to our vendors to get most parts “next day” and some of them “same day” without additional charges. A hardware store is conveniently located on the corner of the golf course so we have created a trail to reach it by golf cart. Paul F. Grayson is the Equipment Manager for the Crown Golf Club in Traverse City, Mich., a position he’s held for the past decade. Previously, he spent 8½ years as the equipment manager at Grand Traverse Resort & Spa. Prior to that, he worked as a licensed ships engine officer sailing the Great Lakes and the oceans of the world. |
Get curated news on YOUR industry.
Enter your email to receive our newsletters.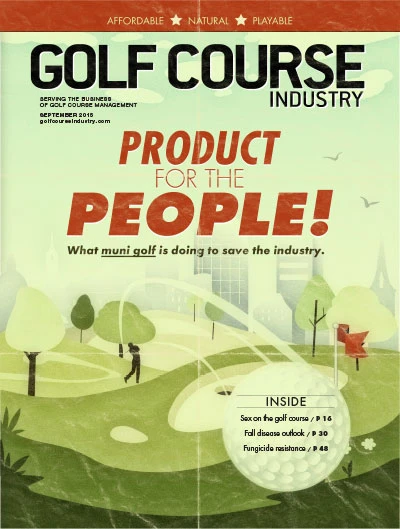
Explore the September 2015 Issue
Check out more from this issue and find your next story to read.
Latest from Golf Course Industry
- Carolinas GCSA raises nearly $300,000 for research
- Advanced Turf Solutions’ Scott Lund expands role
- South Carolina’s Tidewater Golf Club completes renovation project
- SePRO to host webinar on plant growth regulators
- Turfco introduces riding applicator
- From the publisher’s pen: The golf guilt trip
- Bob Farren lands Carolinas GCSA highest honor
- Architect Brian Curley breaks ground on new First Tee venue