Matt Shaffer, director of golf course operations at Merion Golf Club, Ardmore, Pa., has some advice for other golf course operators who are looking to build a brand-new maintenance facility: buy him, Aronimink Golf Club Superintendent John Gosselin and Pine Valley Club Superintendent Rick Christian dinner and a case of beer. Take them out, show them your plans and ask them what you’re doing wrong.
Other than trying to cadge free vittles and booze, why does Shaffer suggest this? Because he, Gosselin and Christian have all built a new facility within the last four years and learned a lot in the process.
One of the things Shaffer learned was that planning and building the maintenance facility – which in his case included chemical storage, equipment storage, boardroom, dorms, living room, men’s and women’s locker room, break room, wash bay, fuel station and loose storage area for sand and soil – was one of the toughest projects he ever undertook. Two grow-ins, building countless greens and redoing countless bunkers didn’t compare to the blood, sweat and tears this project got out of him. It was made especially challenging since they built the new facility where the old one used to be, which forced them to operate out of tractor trailers and tents.
7 tips to maximum chemical storage safety 1. Have a containment area where the chemicals are stored, a curb of concrete around the base of the room or building. A water tight seal should be incorporated in the concrete placement at all concrete control, expansion and construction joints. After concrete cures a concrete sealer and elastomeric joint filler should be applied. 2. Install a controlled temperature system and adequate ventilation system. 3. Build away from the main drainage of water and surface water. A good plan is to have the chemical storage and mix/load building separate from any other structure by at least 200 feet. 4. The most desirable construction materials for walls are Consider concrete masonry units and placed concrete for wall construction materials. 5. A floor sump system should be considered to retain, reuse or dispose of chemical rinsates and unintended releases in storage areas. 6. Store dry and liquids away from each other in separate rooms. Within these rooms, herbicides, insecticides and fungicides should be segregated as well. 7. Be sure your shelving is made of non-absorbing material. |
“And then you’re still expected to deliver the standards even though you’re working like a bunch of gypsies,” says Shaffer. “It took a lot of planning to figure out where, for example, the portable gas tanks and toilet facilities would go. And none of the other course maintenance activities we do stopped. You could probably build a golf course and get 15 change orders, but it would be darn tough to build a maintenance facility and have 15 or less.”
The fill station, chemical storage room and fertilizer building are all self-contained. Shaffer says they ideally would have liked to have put their chemical and fertilizer facilities in a stand-alone building separate from the rest of the maintenance facility so that, in case they ever caught fire, they could burn down without taking everything else with them. But they didn’t have the space. That’s why courses can’t cookie-cutter maintenance facility projects with one ideal design template.
“It depends on your site,” says Shaffer. “Gosselin and Christian had lots of space, which makes it easier.”
It’s all predicated on your budget, Shaffer says, adding that it’s best to back into the project.
“If the club says you have $2.2 million, then you know what you will do and what you won’t do,” he says.
Even though the chemical and fertilizer facilities are not stand-alone, Shaffer says he’s not worried about any catastrophes.
“We haven’t had a leak yet, but it’s contained the whole way around and all floors slope into the building,” he says. “Even if we have a fire and the fire suppression system goes off, quite a bit of water can be contained in that building before it would get loose.”
Shaffer and his team have always been “fastidious” about safety and cited 291 days without a lost-time accident for any of their employees. They have a safety officer on staff and 12 licensed spray applicators.
Everyone has to move up the ranks. In fact, all current supervisors were spray techs first. Any time there is mixing going on in the two 350-gallon tanks, there is an immediate supervisor making sure all protocols are being followed and everyone is wearing the proper safety gear. Spray teams are rotated so they don’t burn out and start taking shortcuts.
“I’m sure our system isn’t perfect, but we’re probably 90 percent there,” says Shaffer.
The entire new facility is self-contained. All the drains run into a central sump, and everything that flows into the sump gets neutralized before being pumped out onto the driving range.
“Any water that gets cut loose in there goes right into the floor drains, which have a pumping system, and then gets pumped into a big holding tank,” Shaffer says.
The fertilizer building has a “high air exchange,” where all air is exchanged every 10 minutes via high-volume, low-voltage pumps.
“You can walk in there in the dead of winter when the doors haven’t been opened in three weeks and you can’t smell any fertilizer,” says Shaffer. “Also, you can run a forklift right into our chemical room, which is nice for off loading product. And everything is behind closed doors.”
It seems like common sense to segregate chemical storage away from the rest of a golf course’s operations, but this is rarely seen in the field, says Mike Vogt, consultant with the McMahon Group.
“By storing all things related to chemical application in a separate area, it’s much safer,” says Vogt. “Plus, the superintendent is in a position to be able to control all of the moving parts of the chemical application process.”
All too often, Vogt sees chemicals, fertilizers, shovels, equipment and coffee makers all stored under the same roof. But Vogt doesn’t necessarily fault superintendents for that.
“It wasn’t until recently that a maintenance facility was considered a steel ‘building-in-a-box’ with a concrete floor and several rooms in one end,” he says. “These cheap metal buildings soon began rusting and getting dented by machinery and, after 10 years, were starting to fall apart and busting at the seams with every maintenance item in one big lump under a metal roof. The biggest reason these metal buildings become popular in the 1960s through the ’80s is that they were a giant step up from the ‘old barn’ and cheap at less than $15 per square foot.”
Now, considering that most maintenance facilities should last 50 years or more, industrial architecture is being used to plan and program buildings to specifically fit the needs of golf course maintenance. No longer are steel buildings being configured to “make do” for a cheap maintenance facility.
Vogt believes one of the best new developments concerning chemical storage safety is chemical manufacturers selling their products in large format packages.
“This packaging makes it easy to safely store large quantities of product,” Vogt says. “The empties are easily recycled, and 10-gallon quantities are slightly cheaper than small format packages.”
Shaffer re-emphasized the need for superintendents to lean on colleagues who have “been there done that” when it comes to building maintenance facilities.
“They can tell you if your containment area is too small, this is how big your chemical room should be, if you’re going to fudge do it here not there, this is the footprint you need to park your sprayers, etc.,” he says. “People who have built these before have a multitude of information that can help you.”
Chemical storage best management practices Store liquids away from dry chemicals. If that’s not possible, store liquids below dry chemicals. Have some type of containment. Even cheap plastic bins can be used to store chemicals on the shelves. Make every effort to keep chemical packages dry and in their original containers with a legible label. Look for old chemicals and get rid of them. “I can’t tell you how many superintendents have old chemicals stashed in the dark corners of the building,” says consultant Mike Vogt. “Many municipalities have programs to dispose of these products.” Get rid of wood shelves. The wood can become contaminated with chemicals over time; toxic waste. Be vigilant. Keep chemicals locked when not using the specific storage area. Breath free. Have a ventilation system in chemical storage areas. Prepare for the worst. Have an emergency plan in place in case of fire, flood or uncontrolled release of chemicals – and be sure to educate all employees on that plan. Documentation. Keep a separate file or a three-ring binder of labels that you have used in a separate place for reference. Safety. Keep personal protection devices (goggles, safety glasses, respirators, dust masks, gloves, face shields, ear protection, etc.) away from chemical storage areas. |
Jason Stahl is a Cleveland-based freelance writer and frequent GCI contributor.
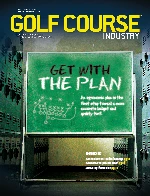
Explore the September 2012 Issue
Check out more from this issue and find your next story to read.
Latest from Golf Course Industry
- Advanced Turf Solutions and The Aquatrols Company release soil surfactant
- Heritage Golf Group acquires North Carolina courses
- Editor’s notebook: Green Start Academy 2024
- USGA focuses on inclusion, sustainability in 2024
- Greens with Envy 65: Carolina on our mind
- Five Iron Golf expands into Minnesota
- Global sports group 54 invests in Turfgrass
- Hawaii's Mauna Kea Golf Course announces reopening