Are you prepared for a hazardous material spill?
Have you ever had a spill, or unintended release of a hazardous material at your course and your first reaction was “Oh s#*!, what do I do now?” No one wants to be responsible for releasing a potentially toxic chemical into the environment and exposing yourself and others to the risk of contamination and injury. You don’t want an emergency to be the first time you’ve thought about how to respond; planning ahead will prepare you to handle the situation and minimize the risks involved.
Let’s start with determining what a hazardous material is. In general terms, hazardous materials are chemicals that pose a threat to the environment and the health and safety of workers and others. We use a lot of chemicals on the golf course — cleaning fluids, fertilizers, pesticides, paints and fuel are all considered hazardous materials. In normal use these chemicals are valuable tools we use to do our jobs, but they also have the potential to cause adverse effects especially in large quantities and concentrations such as a spill.
All employers are required to develop and implement a written safety and health program including emergency response procedures and a Hazard Communication plan. The Emergency Response Plan outlines procedures for dealing with various emergencies and the Hazard Communication Plan makes workers aware of the potential hazards involved in using chemicals. Let’s take a look at how you can develop an Emergency Response Plan for chemical spills, using the information included in your Hazard Communication Plan.
There are five parts to a Hazard Communication plan — 1. Materials Inventory; 2. Labels; 3. Safety Data Sheets; 4. Training; and 5. Written Plan. Labels and Safety Data Sheets give you all of the specific information you need to understand the hazard associated with a product and how to handle and use it in a safe manner. Looking at any product label you’ll quickly see the signal word, either “Warning” or “Danger,” as an indication of the relative severity of the hazard. The signal word tells you at a glance how dangerous the material is. If you see “Danger” and the skull and crossbones pictogram, be extremely careful because this product could be lethal. Every label also has a precautionary statement describing recommended measures to minimize risks associated with exposure to the hazardous chemical in case of accidental spillage. The precautionary statement has other safety information such as the PPE required for handling, use and cleanup; what to do in case of a fire; and first aid treatments.
You’ll find the most detailed information in the product Safety Data Sheet. There are 16 sections to the new GHS (Globally Harmonized System) Safety Data Sheet, four of them provide information you need when responding to a spill.
Section 2, Hazard Identification — Has the hazard class for example “Flammable Liquid,” the signal word, pictograms giving a graphic indication of the type of hazard, and the Precautionary Statement that is on the label.
Section 4, First Aid — Instructions for administering first aid to exposed persons, including important symptoms/effects, acute, delayed; required treatment.
Section 5, Fire-fighting measures — Lists suitable extinguishing techniques, equipment; chemical hazards from fire.
Section 6, Accidental release measures — Lists emergency procedures; protective equipment; proper methods of containment and cleanup. This section distinguishes a small or large spill when volume has a significant impact on the level of the hazard and suggested emergency procedures for evacuations and consulting other experts when needed.
This information, found on product labels and Safety Data Sheets will help you develop your Emergency Response Plan and put it into action. The five steps for addressing chemical spills outlined in your Emergency Response Plan are:
Evaluate/Rescue
When a spill happens or an unintended release of a hazardous material is detected, the first thing you should do is make a quick evaluation of the spill area and provide immediate assistance to anyone involved. The rest of your actions will be determined by where the spill happened, what type of material has been released, gas, solid or liquid, how much has been released, is there a fire or risk of a fire, and has anyone been contaminated or injured.
Confine
Once you’ve made your evaluation of the situation, if material is still leaking, try to stop the discharge, then confine the spill. Depending on where the spill occurred you may need to close doors, cover floor drains and use soil or an absorbent to restrict movement of liquids.
Report
Next, report the spill to a responsible person. This could be your safety coordinator, the superintendent or assistant superintendent, or possibly someone designated as leader of a response team. Be prepared to provide information on injured persons, the material spilled, estimated quantity and the location. In some cases, other agencies or medical assistance should be contacted. Obviously, call the local fire department if the fire is too large for you to extinguish.
Secure
The area should be secured until an emergency response team arrives to make sure no one enters the spill area.
Cleanup
Cleanup should be performed by qualified persons with appropriate training, personal protective equipment and cleanup materials. Typical cleanup procedures include: waiting at least 30 minutes if volatile materials are present, wearing appropriate PPE to protect skin, eyes and respiration, gently sweep or use damp towels to collect powders, absorb free liquids with towels or other absorbents, and collect waste and contaminated PPE for proper disposal.
These two plans provide the information your employees need to respond quickly and appropriately to a chemical spill. When combined with a good training program, including practice drills, your crew will be prepared to appropriately respond to a chemical mishap and reduce the risk of injury to themselves and others.
Mickey McCord is the founder of McCord Golf Services and Safety, providing safety training for superintendents and turf maintenance crews. He is a frequent GCI contributor. Check him out at mccordgolf.com and on Twitter at @mccordgolf.
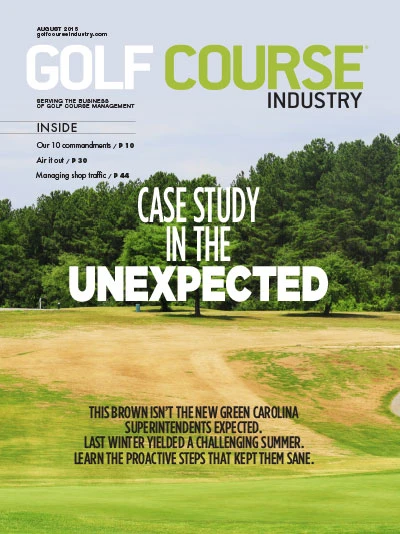
Explore the August 2015 Issue
Check out more from this issue and find your next story to read.
Latest from Golf Course Industry
- Golf Construction Conversations: Reed Anderson
- ’Twas the Night Before Christmas (on turf)
- Twas the Night Before Christmas (the turf version audio)
- Advanced Turf Solutions and The Aquatrols Company release soil surfactant
- Heritage Golf Group acquires North Carolina courses
- Editor’s notebook: Green Start Academy 2024
- USGA focuses on inclusion, sustainability in 2024
- Greens with Envy 65: Carolina on our mind