Tow vehicle hitch
The 2012 Model 07273 Toro Workman MDX turf vehicle came equipped with a factory-mounted Category III Reese-type receiver without a hitch. An in-house hitch was built which extends outward approximately 16 inches and drops down 4 inches to keep the trailer level using 2 inch x 2 inch x 1⁄4 inch square tubing that slides into the receiver. The remaining fabricated flat steel pieces are also 1⁄4 inch thick. A 5⁄8-inch diameter hole was drilled into the hitch so that a lynch pin could slide in to hold the hitch in place. The hitches were welded together and then painted with a primer and a “Toro red” spray enamel. The Rubbermaid Model 6WU47 Trailer (15 cubic yard) navigates short curves easily, does not “jackknife” or hit the tailgate in any way because the hitch is far enough away from the tow vehicle. The cost for each hitch was less than $30 after the R&D was completed and it took no more than 2 hours to build and paint each one. Brad Boyd, director of agronomy, Manual Benitez, equipment manager, and Eliud Cruz, mechanic/fabricator, make up the team at the Dorado Beach Resort & Club in Dorado, Puerto Rico.
Cart path edger
The Dorado Beach Resort & Club in Dorado, Puerto Rico, has a 2005 Toro Sand Pro that has a modified cart path edging wheel. Two maintenance staff used to take about four days to edge the cart paths on 72 holes with trimmers, where it now takes one person 11⁄2 days. The edging wheel blade can be raised, lowered & angled hydraulically, by using the lift handle that used to operate the rear rake mechanism, so that the proper position is achieved, especially when going around curves on the cart paths. Many of the hydraulic components where “cannibalized” from retired triplex mowers and the hoses & fittings are new that cost about $50. The R&D took about three weeks after many field trials for proper refinement. For example, the front length of the Sand Pro had to be reduced because of the variable turning radius of the machine vs. the cutting wheel itself. The engine was also rebuilt in-house. The total labor cost about $400. Brad Boyd is the director of agronomy; Eliud Cruz is the fabricator; and Manuel Benitez is the fleet manager.
Repainting cups
The art of re-painting metal putting green regulation cups is done efficiently first by soaking them in carburetor cleaner for about an hour in a soaking basket that holds three cups at a time. After they are clean and dry, paper cut-out discs are placed at the bottom of the cups so they remain unpainted. A plastic parts bin is then used, which holds nine cups, where they are painted with a high-grade enamel spray paint in a portable can. The parts bins are stackable so they can be stored neatly in the parts room. Zinc cups are easier to paint than the aluminum cups and they will last a lifetime. Eric Kulaas, equipment manager, at the Renaissance Vinoy Resort & Golf Club, St. Petersburg, Fla., came up with this great idea. Kulaas also painted a complete set of cups pink in color for a breast cancer charity golf tournament. It takes about 6-7 hours for the entire process for 18 cups and it costs less than $50 for the carburetor cleaner and paint.
Have you innovated a new contraption in your shop?
Have you tinkered with equipment so it better meets your needs. Share your best ideas by emailing them to gci@gie.net.
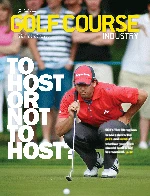
Explore the August 2012 Issue
Check out more from this issue and find your next story to read.
Latest from Golf Course Industry
- Editor’s notebook: Green Start Academy 2024
- USGA focuses on inclusion, sustainability in 2024
- Greens with Envy 65: Carolina on our mind
- Five Iron Golf expands into Minnesota
- Global sports group 54 invests in Turfgrass
- Hawaii's Mauna Kea Golf Course announces reopening
- Georgia GCSA honors superintendent of the year
- Reel Turf Techs: Alex Tessman