Big Canyon Country Club of Newport Beach, Calif., is a quiet place in the early morning, but that doesn’t mean work isn’t getting done. The 18-hole private club sees crew members buzzing about the course with utility vehicles before the first player shows up for the day, even with the course nestled right up against a residential community. “We have 20 silent cars we can use,” says John Hall, head mechanic of golf course maintenance. “At 6 a.m., we’re out and working hard and totally silent. We’re still able to get the job done and stay out of the players’ way.” The turf crew’s dream of clearing the course without interruption is possible, thanks to the batteries powering the electric vehicles. “For the crew, we had a six-year-old fleet that had Trojan batteries,” he says. “When we changed from Club Car to E-Z-Go, we got 20 utility vehicles that are electric in our maintenance fleet. We’ve had those for six years now, and they’ve had Trojan batteries, too.” There are still a healthy number of gas vehicles available to his crew, but electric vehicles are a big part of his fleet. While they help keep the crew moving, they’re certainly not the majority of the electric vehicles on the course after the purchase of their new golf cart fleet last year. “There are 75 golf carts in our fleet,” says Hall. “We received those carts in the first week of December last year. Each of those had the new HydroLink system, which we were excited about. For the golf carts, it’s been about eight months since we’ve started that fleet. We’re just using those batteries on everything else on the course.” Eight months later, the carts are still running strong. Under the lighter strain of the rounds of golf, those batteries don’t see as high a need for replacement, with each battery lasting much longer and reaching a lifetime of four or five years, according to Hall. But when you “put a trailer and a piece of equipment on those, it wears them down,” he says. Under working conditions, the batteries hold up for the maintenance team as well, though not as long. “Of course, we’re working those batteries a little harder than we probably should with the maintenance cars, but we always get the rated life out of them,” says Hall. “We use them up in 16 months like that, hauling things around. But we never have failures or any internal problems. You just think, ‘Wow, this works.’” It doesn’t just work for Hall and his team. Besides being quieter for local residents around the course, keeping gas usage down is beneficial environmentally, even if it is a little bit tougher on his budget at first. “It’s an environmentally good thing to do,” Hall says. “It’s expensive to be green like that. The cost to operate has to be measured against everybody’s happiness. The guys are a little slower with electric right now, but I don’t think it’s enough to affect (productivity). They’re getting the job done.” The slight pressure is worth it for the availability to work early uninterrupted and not have to work with gas-powered machines all the time. But it’s not just about finding a battery that fits the cart for Hall, and not the only reason his crew uses the Trojan batteries. “One of the biggest things I’d think about is the reliability, and to discover that, you can ask around and get others’ opinions,” he says. “I’ve dealt with a number of mechanics over the years and they said it’s the best. It doesn’t take too much from them to know which way to go.”
Besides that reliability, however, there is also the question of time. Normally, a battery usually takes up time with a mechanic when an internal problem develops, but the biggest time sink for battery work otherwise is watering the battery cells. “I’d been having to water batteries one cell at a time,” says Hall. “With 75 cars, that took about 4½-5 hours. It was cumbersome to get the job done.” But the new fleet of cars brought a big change to the maintenance routine in the HydroLink system, which cut down drastically on the time spent watering batteries. “I asked around about a lot of the systems I’d been seeing, because I didn’t have it. With the HydroLink system, it was a major difference,” says Hall. “The HydroLink was just really impressive. With it, I watered four cars with four batteries on each in about a minute. We’ve done it about 10 times since we purchased the cars, and it takes about 1½ hours to do it, and that’s checking the cable nettings, too. My assistant does them – I enjoy seeing him come back by the coffee break for more work.” After having the system, Hall doesn’t want to go back if he is able to use batteries when he upgrades his maintenance vehicles next. “I would want to upgrade my batteries and get the HydroLink system,” he says. “You don’t have to be so concerned about containment and getting it just right inside the battery. “I made sure we had to have that on our golf carts,” he adds. “It’s just really impressive for as little effort as it takes for me to do get that done now.” |
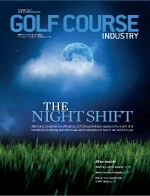
Explore the August 2011 Issue
Check out more from this issue and find your next story to read.
Latest from Golf Course Industry
- Advanced Turf Solutions and The Aquatrols Company release soil surfactant
- Heritage Golf Group acquires North Carolina courses
- Editor’s notebook: Green Start Academy 2024
- USGA focuses on inclusion, sustainability in 2024
- Greens with Envy 65: Carolina on our mind
- Five Iron Golf expands into Minnesota
- Global sports group 54 invests in Turfgrass
- Hawaii's Mauna Kea Golf Course announces reopening