Has the old girl seen better days? Is she causing you more headaches than she’s worth? We talked to several industry experts who shared their opinions on how best to approach the major step of replacing your course’s water pumping station and system.
“Superintendents need to make sure that the pump station meets their flow and pressure requirements,” says Brian Vinchesi, a design engineer with Irrigation Consulting. The superintendent or an outside professional should determine the optimum flow and pressure for the pump station, he says. Once that is accomplished, service will be important.
“What good is it to purchase a station if there is no local company to service it?” Vinchesi says. “Additionally, pump stations last a long time. Is the company you are buying it from going to still be in business in 20 years when it needs service or parts?” Vinchesi says regional pump station manufacturers can sometimes leave a superintendent high and dry (pun intended) when they retire, causing golf courses to have to buy new control panels so they were serviceable.
All pump stations are manufactured by outsourced components except for a few parts, so it’s important to look for quality components and the warranty on those components, says Wayne Mills, superintendent at La Cumbre Country Club in Santa Barbara, Calif.
“I have seen in my 30 years companies come and go, or are bought by a competitor,” Mills says. “So do not count on them being around in 10 years when you really start to need them.”
Superintendents should approach the decision of replacing their pumping station in a measured manner, says John Pollok, Ewing Irrigation’s southwest agronomist.
“First things first,” he says. “You want to know who is going to service the pump station. A pump station is like a very expensive, exotic car and not every mechanic can work on it.” Also, determine who will be servicing the station.
Selling it You’ve identified the need, now how do you sell this costly expenditure to your members or senior management? With maintenance and operation records, says irrigation consultant Brian Vinchesi. “Document how often the station is out of service, how long it takes to water the golf course if it is too small, and how often and how much you are paying for it to be serviced,” Vinchesi says. “Pictures also are needed. Most members have never seen the pump station nor even know where it is. If the pictures show a rusted piece of equipment with wires hanging out of it, most people can relate to that. I once had a superintendent who was having trouble getting a new station bring his board through the pump house. He had approval by the end of the meeting.” It comes down to the fact that water is critical to healthy turf, says Richard Ziegel, sales manager for Pumptronics. "No matter how much fertilizer you put down or what cultural methods you use, without water you will not have healthy turf," he says. "The pump station is the heart of your irrigation system, and critical to its use. In my mind, it is probably the single most important piece of equipment a superintendent has.” |
“Regardless of what type of station you purchase, what bells and whistles you have installed, it will need to be serviced and it will go down,” Pollok says. “It’s Murphy’s Law. Your pump station will typically go down in August when it’s hot and dry, but not January. In my first year as a superintendent, my pump station went down Friday, Sept. 13, two days after I finished aerifying greens and overseeding the rest of the golf course. By the time it was up and running again (two weeks later), we had to re-seed the course.”
Consider all of the factors that contribute to the overall performance and the lowest cost of ownership over the life of the system, says Rex Hansen, west regional sales manager at Rain Bird Golf. Some of the key features include:
- Product quality;
- Energy savings features;
- Water savings features;
- Technology integration between the pump station and the control system;
- Remote monitoring; reporting and control; and
- Local service and support.
Whomever you purchase your pump station and system from must be reliable and have readily available replacement parts to go along with excellent service, Pollok says.
“You also need a good warranty, and always purchase from a reliable company, as most of the parts, components, pumps and motors are extremely similar,” Hansen says. “Variable frequency drive (VFD) is as close to mandatory as there is on any station. This allows your expensive, ‘exotic car’ to run at the correct speed based on the demand.”
Without VFD, the pump station runs wide open all the time when there is demand and it shuts off when there is not a demand.
“What happens is your station will cycle, meaning it will turn off and on repeatedly trying to maintain the proper flow, which is never good,” Hansen says. “A pump station needs to be a well-oiled machine, it needs to purr like a kitten otherwise you are wasting money, energy, placing wear and tear on your pipes, valves, heads, motors and pumps.”
Different pump types have differing features, says Richard Ziegel, sales manager for Pumptronics. “Vertical turbines are usually the most efficient and longest lasting, but are costly and can be loud,” he says. “Submersibles are quiet and less expensive, but can be difficult to service and need deeper wet well depths. Centrifugal pumps are usually the least expensive option and are easy to service, but they are not as efficient and can have issues like losing prime. Proper pump choice is a matter of matching the best pump style to what they have in place, what they want to spend and what they are trying to achieve.”
Quick tips Ideally, you want a pump station installed before the old one breaks down or before overseeding, says John Pollok, Ewing Irrigation’s southwest agronomist. “There is typically an eight to 10 week lead time on a new pump station,” he says. “It’s not an item that is hanging out at Walmart. These pump stations are built per spec and a labor dispute in the country that these components are made could delay the process even longer.” Purchase the station as soon as possible, Pollok says, and install it when you don’t need to water for a few days. Reduce the installation cost by either building a new pump house, or serving as the general contractor. “The course could also buy a prefab building with the station to save on cost,” Gregg says. “After the sale, benefits of a new pump station are the warranty, start up and future service.” When a new pump is ready to be turned on, Pollok advises to lower the rate of flow by 50 percent and gradually raise it up over a few days. “The new pumps will work much more efficient and the speed of water will flow through your pipes at a quicker pace,” he says. “This typically causes damage to pipes, fittings and valves. I’d recommend not turning it on Friday afternoon, as Mr. Murphy knows what will happen.” |
A built-in computer is necessary, as it alarms staff when the system goes down, Pollok says. It gives data, such as current flow, faults within the system and gallons used, and you can set parameters to adjust time of use and flows easily. It also helps trouble shoot your pump station when it goes down.
“Injection systems built into the pump station and its computer can be very a beneficial feature,” Pollok says.
So how do you determine what’s important and what isn’t when you purchase a new pump station?
“Do you need AC in your car?” Pollok asks. “If you live in Phoenix, yes. If you live in Maine, maybe not. The superintendent who pumps 15 million gallons of water a year on his course probably doesn’t need many of the available options. However, when I was pumping 400 million gallons of water in Las Vegas, our pump station had its own AC unit and a lot of bells and whistles because it was our lifeline and we needed to protect our asset.
”It’s a case-by-case basis, he says, and the industry has come a long way with pump station features.
Communications and integration are the “frontier technologies” in pump stations, Hansen says. When properly used, these technologies can add significant value by saving water, electricity and labor. Furthermore, these technologies can be used to mitigate risk by constantly monitoring the system and automatically taking action in the event of a problem. For example, a system that compares actual flow to theoretical demand can sense a pipe break and automatically shut itself down before a green is washed out.
Consider how the pump communicates with the irrigation system, how accurate the reporting software is, the service and quality of components, warranty coverage for parts and labor, and the efficiency of the pump, says Dan Gregg, Dan Gregg, regional sales manager of prepackaged pump stations for Flowtronex, a Xylem brand.
“The more efficient a motor runs, the longer it lasts,” Gregg says. An additional consideration is the return on investment and what costs are associated with pumping water.
Vinchesi advises the pump station have a variable frequency drive. “Look at pump and motor efficiencies,” he says. “Higher efficiencies cost more up front but pay for themselves over time. Minimum motor efficiencies should be in the 93 percent plus range. Pumps vary, but turbines should run at least 84 percent, centrifugals 70 percent and submersibles 60 percent.”
Seek expert advice when considering the purchase. “We had myself and a group of members composed of a civil engineer, a marine engineer and someone who had worked in the oil industry,” Mills says. “We looked at components’ quality and if they were readily available for replacement, simplicity of design and a good service network. We also talked to other supers in the area on their experience with service and issues they had with stations.”
New or used? Buying a used water pumping station is an option for superintendents, but one that should be approached with extreme caution and much consideration. The price of a used pump station can be significantly less expensive, says Dan Gregg, regional sales manager of prepackaged pump stations for Flowtronex. But, he warns, with no warranty you may not know the history of the station and there is no guarantee it won’t go out as soon as you start it up. Also, the station may have out-of-date technology and wind up costing the course more money to operate, negating the savings up front. In addition, getting a station to fit an existing location could be difficult, and pump column length may need to be changed, costing money. “There is only one potential benefit from buying a used pump station; perceived lower initial cost. The downsides, however, can be considerable,” says Rex Hansen, west regional sales manager of Rain Bird Golf. Pump stations are specified, designed and manufactured to meet the unique requirements of each golf course. A used pump station will likely be a compromise and will therefore not be designed to optimize overall operating costs. Hansen recommends considering a used pump station when these conditions exist:
|
John Torsiello is a Torrington, Conn.-based writer and frequent GCI contributor.
![]() | Garden Center is adjusting the way the 2025 Top 100 Independent Garden Centers List is built. This year, for the first time, we are asking all retailers to report annual revenue for *only* their top-performing or flagship location. Submit your IGC for consideration on the list today.
|
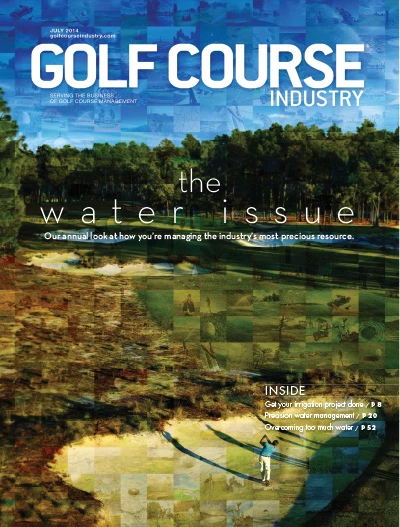
Explore the July 2014 Issue
Check out more from this issue and find your next story to read.
Latest from Golf Course Industry
- PBI-Gordon Company hires marketing manager Jared Hoyle
- Mountain Sky Guest Ranch announces bunker enhancement project
- GCSAA names Joshua Tapp director of environmental programs
- AQUA-AID Solutions bolsters Sunshine State presence
- Escalante Golf acquires secluded Illinois course
- Tartan Talks 105: Nathan Crace and Todd Quitno
- Disease Discussion 24: Let the turf talk to you
- From the publisher’s pen: Foggy intrigue