Replacing an irrigation system might be the biggest – and most important – project in a golf course superintendent’s career.
So much money, so many choices, so little time to get it completed before members or ownership begin to grumble.
So let’s get the process started correctly.
Problems under ground
Brian MacMillan became the superintendent at Port Jefferson Country Club on Long Island in 2010. He inherited a big problem.
The course’s irrigation system, which MacMillan estimates was 20 to 25 years old, didn’t stop leaking. To control the water, MacMillan relegated one of his two assistant superintendents to leak-related duties. The job lacked glamour and offered few respites. Annual repair bills exceeded $20,000.
“I understand fixing a head in the afternoon or two or three heads a week,” MacMillan says. “That’s fine. But having a guy non-stop to just do that. … We knew we could open him up to do so many more things, really paying attention to turf conditions instead of looking at the irrigation system all the time.”
With 63 holes of golf and more than 70 acres of common areas, Timber Pines in Spring Hill, Fla., had what superintendent Robert Wiemer calls a “piecemeal” irrigation system, with components being installed as early as 1982 and as recently as 1995.
The facility’s irrigation needs are vast and the amount of water available is fixed, which made obtaining an efficient system utilizing HDPE piping a priority. “We only have a certain amount of time to water – when it’s dark until it gets light out again because everybody wants to go out and play golf,” Wiemer says.
Poppy Hills Golf Course in Pebble Beach, Calif., sought to upgrade its 16-year-old system to improve efficiency as a means to handle California’s water restrictions and rising utility costs.
“With any system, it’s about efficiency,” says Manny Sousa, the course’s superintendent for the past 24 years. “You want to be efficient in water distribution so your turf is always in good health. You don’t want it wet. You don’t want it dry. There’s also power consumption. That’s all big dollars. We’re also looking at the next big thing. Generally speaking, it’s time anywhere from 16 to 20 years. It’s not that it can’t go any longer, but if you want efficiency, you stay within 16 to 20 years.”
Consultant Dave Davis of David D. Davis and Associates has worked on more than 200 golf course irrigation projects. He says it’s time to start pushing for a new irrigation system when those outside the maintenance crew begin noticing problems.
“When complaints get to the greens committee and it has to do with playability, that’s when it’s time to renovate or repair,” he says. “Or another sign is when you have a single part of your irrigation system that is the majority of your repair bill for a season or a series of seasons.”
Convincing time
Identifying a faulty or inefficient system doesn’t guarantee a greens committee or an owner will propel irrigation atop a priority list.
“The members might see the mowers, but they don’t see the sprinkler heads, they don’t see the pipe, they don’t see the broken fittings,” irrigation consultant Jim Barrett says. “You don’t see irrigation. Part of the decision-making process for the decision-makers or membership is showing them the defects.”
Barrett, founder and president of James Barrett Associates, has worked on 400 golf course irrigation projects and combined with four other experts to publish a 464-page book, “Golf Course Irrigation.” A “realistic appreciation” of the project’s cost must be determined early in the planning process, he says, and superintendents must perform significant research to prove the need justifies the cost. And, yes, irrigation is costly, with many new systems ranging between $1 million and $2.5 million.
Photographs and PowerPoint presentations are traditional ways of demonstrating the need for a new system. Sometimes, though, it takes a bold maneuver to convince a facility’s decision-makers to support a project.
One of Barrett’s favorite stories involves a country club superintendent bringing a cardboard box filled with rusty pipe fittings to a meeting and unloading the contents on a white tablecloth. The superintendent then made his pitch for a new system.
“He said, ‘OK, people, if I was your plumber and took these pipes out of your walls, would you believe me when I said, it’s time to replace your plumbing?’” Barrett says. “There was this sort of stunned silence. And the point is, he was showing them the problems. If he didn’t do it that way, they would never see the problems.”
Philadelphia Cricket Club director of grounds Dan Meersman used more guarded tactics when convincing his board to include an irrigation system replacement in the club’s golf course restoration plans. He used physical changes proposed for the club’s original 9-hole St. Martin Course and 18-hole Wissahickon course as the spark to pitch replacing the irrigation system.
With the U.S. economy reeling, membership voted against the renovations in 2007. But Meersman and architect Keith Foster remained persistent and the club started its restoration project in the fall of 2011. The final stages of the project were completed this past spring. “We had normal wear and tear in our irrigation system,” Meersman says. “But that’s not what drove it and sold it for us. It was mainly an investment in a whole new golf course, new greens, new tees, new bunkers, new fairways, resodding the rough. If they were going to make a new investment over the next 50 to 75 years, a new irrigation system to match those new features was just a necessary process.”
Go team, go Superintendents spend most of their working lives concocting ways to maintain and enhance what rests above the ground. There’s no shame in soliciting help when plotting an irrigation system replacement. In fact, it’s encouraged. “The biggest decision was pretty much finding the right consultant,” says Robert Wiemer, the superintendent at Timber Pines in Spring Hill, Fla. “The consultant is somebody you bounce ideas off. They have the experience to deal with the negatives and positives, and what can happen.” Dedicating an assistant or veteran irrigation technician to the irrigation renovation also helps reduce the stress associated with the installing and digging. “It takes a huge load off the superintendent. (He) still has a golf course to maintain, and if he thinks he can be the 24-7 guy in the trench and run his golf course, he is really going to drive himself to drink, lose his hair or get old in a hurry, more so even than the normal stress of being a superintendent,” says irrigation consultant Jim Barrett. |
Poppy Hills completed a $6.5 million course renovation project this past spring. The project started with discussions about replacing the irrigation system, Sousa says. The discussions, many of them informal, occurred regularly for years, and led to the course’s owners, the Northern California Golf Association, deciding to complete all of the work at once.
“It’s one of those things where it begins with a discussion and somebody says, ‘Our sprinkler heads should be replaced. Our pumps are OK, but they are old and we might get by, but it doesn’t make sense not to replace them,’” Sousa says. “It’s like a train going down a hill. You can’t stop. You try to do one thing, it escalates and they say, ‘Let’s do it right.’”
Choices, choices, choices
Sousa compares the competition to sell irrigation systems to the development and marketing showdowns in one of America’s iconic industries.
“I have been in the business for almost 40 years,” he says. “I have dealt with lots and lots of irrigation systems. Different types, old types, cheesy types, good types. But in the last 20 years, the ones I felt more worth dealing with were Toro and Rain Bird because they are typically like the Ford to Chevy. Ford says, ‘No, we have a better car.’ The next year, Chevy says, ‘No, we have a better one.’ Then Ford says, ‘Good luck. Now we have a better one.’ There are always trying to outdo each other and they are trying to do it to make money. For us, what it does is take technology to the next level. For us, it’s a great thing.”
Price and service were the biggest factors in Timber Pines’ decision. Members and the club’s board of directors heard presentations from the two major suppliers competing for the project. The facility selected a two-wire system to eliminate running copper wires out to the course. The system fit the facility’s budget. “We did a lot of teaching to let our residents and board of directors know why this was the system that fit our needs,” Wiemer says.
Philadelphia Cricket Club considered aesthetics when making its decision. The club wanted to control irrigation on all three of its courses – a third 18-hole course opened in 2002 – from a central location through the Internet, and it didn’t want visible signs of the irrigation system.
“We didn’t really want to see any satellite boxes,” Meersman says. “We have really vast vistas and an old, classic course. We didn’t want to see any infrastructure on the course from the irrigation system. We wanted to get it under one vendor to make that happen.”
The availability of local service must be a priority when picking a system, Davis says. “What we say as somewhat of a parody is that your system fails on the day before the member-guest tournament,” he says. “It always fails at the wrong time, no matter what, no matter how good or bad the system is. You need people that are close.”
Opening and closing
Strangers will be on your course for months, which means operating adjustments must be made.
Port Jefferson, for example, started its project in mid-November of 2013. The weather allowed for regular work until Christmas. Snow then pestered Long Island for the next two months.
The club opened nine holes on April 1. The entire course opened in May. MacMillan calls the disruption to play “minimal.” A normal season consists of the club opening nine holes around St. Patrick’s Day.
Philadelphia Cricket Club completed its course restoration and irrigation project in phases, with work starting in the fall of 2011. The project was finished this past spring. The club has 45 holes, which makes enduring a major project easier compared to courses with 18 or 27 holes. Members also received reciprocal privileges at 50 Philadelphia-area courses. Meersman considers communication with members, especially when it comes to a club’s reciprocal program, key to a successful irrigation or renovation project.
Timber Pines completed its project in phases and limited most of its course closures to nine holes at a time. Because of the scope of its renovation project, Poppy Hills was closed for 13 months. The course reopened this past spring. “Basically, it was 10- to 12-hour days, six days a week when the contractor was here,” Sousa says.
One of the myths surrounding irrigation work includes images of large vehicles tearing into pristine turf. Many members will be surprised by the scenes they witness. “The equipment is very small equipment,” Barrett says. “There aren’t 500 guys all over the golf course.”
A solid presentation to members can eliminate concerns regarding the construction process. To ease member apprehension, Barrett recommends using pictures of successful golf course irrigation work. “That part is really important,” he says. “Most members expect the world to end for two years.”
By the Numbers
Source: GCI State of the Industry research
Guy Cipriano is GCI’s assistant editor.
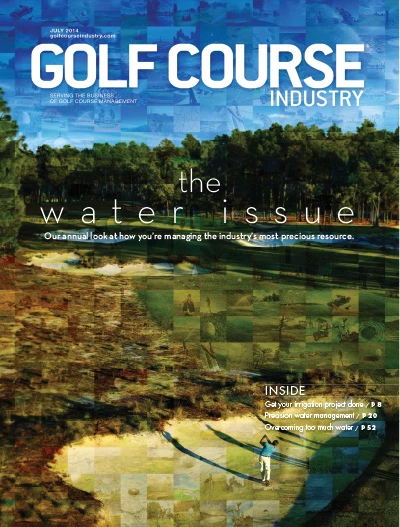
Explore the July 2014 Issue
Check out more from this issue and find your next story to read.
Latest from Golf Course Industry
- PBI-Gordon Company hires marketing manager Jared Hoyle
- Mountain Sky Guest Ranch announces bunker enhancement project
- GCSAA names Joshua Tapp director of environmental programs
- AQUA-AID Solutions bolsters Sunshine State presence
- Escalante Golf acquires secluded Illinois course
- Tartan Talks 105: Nathan Crace and Todd Quitno
- Disease Discussion 24: Let the turf talk to you
- From the publisher’s pen: Foggy intrigue