During morning or evening rounds you notice the condition of your turf is starting to suffer. The culprit – and solution, for that matter – could be your sprayers and spreaders.
Over applying or under applying pesticides and fertilizers pose any number of turf maintenance problems. Improper calibration is one of the top reasons for pesticide or fertilizer performance failure, which in turn leads to turf decline, poor aesthetics and playability issues, says Brooks Hastings, product marketing manager for John Deere Golf.
Excess applications due to improperly calibrated fertilizing equipment can result in nitrate leaching or phosphorous runoff, says Dr. Tamson Yeh, pest management and turf specialist at the Cornell University Cooperative Extension.
“Excess nutrients, especially nitrogen, promotes diseases such as rhizoctonia,” he says. “Too little nitrogen promotes diseases such as anthracnose. Excess phosphorous can promote the growth of algae on greens.”
Over application increases the risk of the product moving out of the intended spray area and damaging nearby desirable plants, says Dr. David Han, associate professor and extension specialist, of turfgrass management at Auburn’s Department of Crop, Soil, and Environmental Sciences.
Lastly, with escalating fertilizers and fungicides costs it makes sound financial sense to accurately control product use, says Trevor Broersma, superintendent at Washington National Golf Club in Auburn, Wash. “On the extreme end of things, it is cheaper to calibrate a sprayer or spreader than it is to re-sod a green due to damage done by non-or poorly calibrated equipment,” he says. “I have seen the end result of courses that had miscalculated lime applications on a driving range and it caused a majority of the turf to die.”
With so many potential negative consequences, why isn’t sprayer and spreader calibration a routine task? For one, Hastings says calibration is often thought of as a time-consuming undertaking. But that isn’t necessarily true. “Calibrating is commonly thought of as a burdensome task,” he says. “But in the grand scheme of things, the amount of time you spend calibrating is nothing compared to the work it would take to repair the turf as a result of over application.”
Often, calibration is only time consuming the first time, says Dr. Aaron J. Patton, associate professor of horticulture and turfgrass extension specialist at Purdue’s Department of Horticulture and Landscape Architecture. “After the first time and when organizing the resources needed to calibrate, calibration can be quick and easy,” he says. “Golf courses should consider creating a tub or box of the necessary materials that they need to calibrate.”
Han has found a number of helpful Smartphone apps. For example, area calculator apps are great and make finding the area to be treated go much faster. “You don’t need a separate calculator and stopwatch anymore, either,” he says. “For calibrating and using handheld or pushed equipment, a metronome app makes walking at a constant speed much easier.”
Getting the math correct is essential, especially when it comes to fertilizing greens, says Broersma. “We do our greens in two directions, wheel to wheel,” he says. “So, while doing the math our guys have to divide by four for the amount of pounds of product being applied per 1,000 square feet. We purchased a spreader calibrator for $250 and it was the best money we ever spent.”
Calibrating equipment shouldn’t be time consuming, says Kevin Stinnett, a Jacobsen territory sales manager in North and South Carolina, especially if superintendents can get into a habit of doing it on a regular basis with a standard procedure.
“It can give turf managers a little piece of mind knowing one of the most important tools they have is dialed in and ready to make precise applications,” he adds.
A firm rule superintendents should follow is that sprayers should be calibrated before using them at the start of each growing season, but more frequent monitoring is advised, Patton says.
“How often you will need to check the calibration after that varies by personal preferences and amount of use,” he adds.
Many turf pros calibrate daily or weekly. These frequent calibration checks ensure consistent application results.
“I advocate for more frequent calibration,” Patton says. “Frequent calibration is especially important to find problems such as clogged nozzles, screens, or possibly to discover that some setting, such as pressure, speed, or nozzle type, was changed since the previous application.”
In addition, always calibrate sprayers after maintenance is performed on them.
“Check nozzles for wear each time you calibrate the sprayer, and frequently clean screens,” he says. “And, before you calibrate your equipment, always inspect it to make sure it is in good working condition. Be sure the tires are properly inflated and hoses are free of cracks and wear.”
Other factors impact calibration, as well, says Yeh. For example, he advises performing calibration based on how frequently it’s being used, how often product is changed, how abrasive the product is to the equipment, how rough the ground covered by the equipment is, and the material the spreader is constructed with (for example, a warped plastic body spreaders will require recalibration).
Rotary and drop spreaders should be calibrated when they are purchased, and at least once a season if the equipment is used for the same product, preferably twice, especially if the spreader has a plastic body, ideally three times if you are not changing product, or if you are going over very rough ground consistently. “If you suddenly encounter rough ground, check calibration after to make sure the bouncing has not thrown off calibration,” says Han.
A back pack spreader calibration should be done when you change applicators (everyone has a different walking speed), when you change nozzles, if there is a noticeable change in product viscosity, or you are using abrasive products with your nozzle tips. Calibrate at least once a season if you are using a single product with a single applicator. Twice a season is preferable to look for nozzle wear and tear.
A boom sprayer should be calibrated each time you change product or change nozzles, at least once a season, preferably two to three times if you are not changing nozzles or product just to make sure all parts are working correctly.
While it’s important to follow the necessary steps in the process for proper calibration, Hastings says it’s also important to not forget about the little things. “One of the most simple, yet commonly overlooked steps in the calibration process is checking the nozzles. Nozzles should be checked for wear each time a machine is calibrated and checked that they are the proper nozzle for what is about to be applied. As a general rule, if they are putting out 10 percent more than what they should be it’s time to replace.”
When assuming what seem like “givens” are correct, such as gearing and speeds when calculating rate or even calibrating a machine, it is always a good idea to double check.
“Even with today’s spray equipment and the new technology which is really incredible it’s still a good idea, in my opinion, to double check what the system is reading,” Stinnett says.
Proper calibration is not something that should be rushed, Yeh says. It should be approached in a concerted, stepwise fashion with all of the steps and their outcomes recorded in a log book. “As spreaders and sprayers become worn, you will be able to look back over records to see when it begins to slip consistently out of calibration, which indicates a change in parts or an entire piece of equipment is necessary,” he says.
Yeh recommends having one or two employees, preferably working together, who check the calibration on a regular basis and even the calibration of equipment right out of the box.
“By having the same individuals perform the calibration this removes some of the variability in technique and in record keeping, which will allow the calibration to be as finely tuned as possible,” he says. “It is good to have two people work together because there can be an operator and a recorder and one can keep check on the other as an extra measure of accuracy. Having different people calibrate and record each time leads to minor inconsistencies due to varying techniques.”
Ideally, the same person who will be operating the equipment calibrates it, Han says. “If your course has a dedicated spray technician, this is the person who should be calibrating.” Consistency in operation, especially in driving or walking speed, is important in maintaining accurate applications. If another person is going to spray that person should check the calibration before doing so.
Many newer sprayers contain a computer type console that reports speed and calibration, Patton says. While these tools that provide details on sprayer speed and flow rate are often “pretty accurate,” remember these tools and sensors “require verification.” You need to calibrate the equipment to verify you can trust the values reported by the equipment.
New tools, which Patton hasn’t tested, can be used to give a quick calibration check by measuring the flow rate of a nozzle. “Using these tools, you wouldn’t have to do a full calibration (assuming speed hadn’t changed), but instead could just check your flow rate (combines nozzle and pressure settings) to verify that it is similar to your previous measurements and settings.”
John Torsiello is a Torrington, Conn.-based writer and a frequent GCI contributor.
Get curated news on YOUR industry.
Enter your email to receive our newsletters.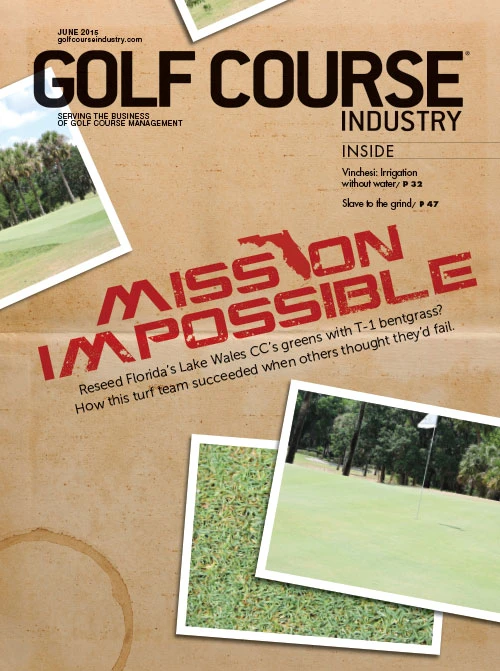
Explore the June 2015 Issue
Check out more from this issue and find your next story to read.
Latest from Golf Course Industry
- Advanced Turf Solutions’ Scott Lund expands role
- South Carolina’s Tidewater Golf Club completes renovation project
- SePRO to host webinar on plant growth regulators
- Turfco introduces riding applicator
- From the publisher’s pen: The golf guilt trip
- Bob Farren lands Carolinas GCSA highest honor
- Architect Brian Curley breaks ground on new First Tee venue
- Turfco unveils new fairway topdresser and material handler