We can all agree the prevailing economic climate has changed the way we do business. Rounds were back up in 2012, which is a great sign that things are beginning to recover, but the National Golf Foundation reported there were some 150 course closures in 2012, while only a handful of new courses opened for play. This is the new reality, and it has prevailed for almost a decade now. It’s on all of us – superintendents, architects, contractors and golfers themselves – to continue the adjustments.
Much of those adjustments have been tough, as we struggle to maintain older golf courses with smaller maintenance budgets and shrunken capital expense allocations.
But there has been one overriding silver lining: When forced to do more with less, professionals get creative. They question the status quo and shed new light on practices we once considered “perfected.”
The best example of this dynamic is greens renovation. Ten years ago, we in the golf industry embraced greens renovation almost as a matter of course. When greens failed to meet expectations, we often rebuilt them because a) there was plenty of money around, b) we had to keep up with the Joneses, especially the new Joneses on the block, and c) renovation was simply something superintendents wanted, and architects delivered.
Today, that situation has been turned on its head. I actually get the impression that some superintendents are afraid to call architects now, if the greens in their charge are failing or seriously underperforming. They’re afraid we’re going to come in there and recommend a full-on green reconstruction program they cannot afford!
Key points
|
Well, any architect with that sort of attitude – that full-blown renovation is the answer to everything – has lost touch with reality. And the fact is, several important alternatives to greens reconstruction have emerged in the last several years. Each one depends on an accurate diagnosis of the problem, of course. And that generally requires several sets of eyes, in addition to your own.
All obvious biases aside, I suggest you start with your course architect. If you don’t have one, you can go to the American Society of Golf Course Architects web site to access a comprehensive list of those working in your region. Fact is, architects get around; they see dozens of courses each year with problem greens, and they’re often a party to fixing those problems. Architects are a resource just like your fellow superintendents, Green Section agronomists and certain vendors are resources. Put them to work as your brain trust.
That said, let’s look at a few ways traditional greens renovation has been reconsidered in the recent past by superintendents and architects alike. If your greens aren’t doing the job, you have more options than you may have thought.
Poor performance. A large percentage of problem putting surfaces are “underperforming” because they’re not draining properly. Ten years ago, that would have meant a greens reconstruction project, but we’ve learned we don’t necessarily have to go there.
Every superintendent knows that deep-tine aerification can remediate drainage issues somewhat by breaking through layering problems, giving water and air an avenue to penetrate the rootzone. But this can often take years to make modest gains, and golfers will quickly tire of the continual punching of deep holes in their greens.
Really poor percolation caused by heavy soil profiles often requires a more radical step: We’ve recommended “slit draining” to many supers struggling with excess saturation, and we’ve been very impressed with the results.
There are several vendors who specialize in this sort of service, but here’s the basic premise: First, the green sod is removed in 5-inch to 7-inch widths at about 6 to 8-foot intervals in a modified herringbone design. The sod is set aside in the order it is removed, so that it goes back in exactly the same spots (to avoid mixing up color patterns… usually of Poa annua). Then a 16-inch-deep drainage trench is cut into the stripped areas, a 2-inch drainage tile system is placed in the bottom of the trenches, and they are refilled with a heavy mix of sand, soil and peat such as a 6:3:1 – heavy enough to retain moisture so the drainage lines don’t show up during dry times. The sod is then re-laid.
Golfers are usually back on these greens shortly after completion, and I can’t think of an example where this didn’t radically improve drainage. Think about it: You’re not just creating a new drainage profile – you’re actually adding a drainage system inside the green, and you’re not rebuilding. It’s rather brilliant, really.
Turf turnover. Sometimes the problem isn’t the drainage capability but the turf itself. It’s either outdated or Poa infested and beyond repair. We’re planning a greens re-grassing project this summer at a private course in Indiana where the superintendent told me he had finally had enough. He just didn’t think his old Poa greens could compete anymore with the new courses in town that were maintaining A1 and A4 bentgrass putting surfaces. He’s been pushing them hard for years to provide the performance his members expect, often edging on the brink of disaster. With the extremes in weather that seem to be the norm these days, he’s finally convinced the club to invest in a re-grassing program, which they’ve embraced as a very worthy insurance policy.
As a firm, we have overseen the re-grassing of greens at dozens of golf courses across the upper Midwest, with nary a dissatisfied client. It’s hard to argue the value of the new bents on the market these days and the benefits they provide in terms of drought and disease control, not to mention playing performance.
Of course, the re-grassing process is not all grins and giggles. While the actual expense of re-grassing is reasonable (roughly $5,000 to $6,000 per green), it’s the downtime that makes clubs hesitate. But it pales in comparison to rebuilding those greens (and re-grassing them) or doing nothing as the old greens eat away at your budget, your nerves, and the patience of golfers.
One last note on re-grassing: we often recommend a slit-drainage and tree removal regimen in concert with re-grassing, to provide the best possible long-term growing environment. To be honest, I’m not sure which of the two is more important. Drainage and sunlight are always critical, no matter what type of grass you’re trying to nurture.
Material matters. Think back 10 years and consider how certain we all were about the materials you needed to effectively topdress a green. We knew just the type and size of sand to use, because the conventional wisdom (the USGA recommendations) seemed so strong and unimpeachable.
In short, the USGA published a study in their Green Section Record by turf specialist Dr. James Murphy of Rutgers University, who cites example after example where coarse sand shouldn’t work but it does, where fine sand doesn’t work – in situations where you’d have sworn it would.
The takeaway is this: The sand you deploy in your greens maintenance and/or construction is vital to maintaining good drainage conditions, and identifying that sand depends on half a dozen factors that are particular to your climate, your turf, the soil profile on that particular green, and wet/dry nature of the green’s micro-climate. All of these angles should be fully explored and tested with a certified lab before you outline a renovation program of any sort.
Alternative methods. One of the big arguments that we’ve heard – and even used – in the past for implementing an 18-hole green reconstruction program was consistency. Any superintendent who has maintained a USGA-profile green side by side with an old push-up green knows that each behaves, maintains and generally performs completely differently. The only way to have consistency, then, is to have all your greens the same.
So what do you do when you have a golf course with 18 push-up greens and only one or two greens are in dire need of renovation – or, more apropos today, you can only afford to rebuild one or two?
In years past, many superintendents and architects would have chosen to build those two greens with USGA recommended profiles, despite the fact that they were destined to behave, maintain and perform differently from their other 16 – likely for many, many years. Why? Because the USGA-profile was and remains the standard, scientifically proven method, and very few decision-makers were willing to take the agronomic risk of an alternative approach.
Well, we’ve discovered that there are ways to rebuild greens and achieve consistency with those old push-up models. The method we prefer uses a profile we’ve dubbed the “modified push-up.”
We begin by taking core samples of a few existing greens on the course, which we send to a testing lab for profile analysis. Often that analysis will indicate a layer of sand/organic mix on the upper several inches (from top-dressing accumulation) over some type of silty loam. The lab then gives recommendations for creating a rootzone/layering that closely matches those results.
We always recommend adding a slit-drainage regimen to the green profile to ensure adequate drainage (can’t stress enough the importance of drainage) and then choose a bentgrass that will perform well under the super’s existing cultural practices and performance standards. That may not always mean the latest and greatest bentgrass varieties, though we always strive to maximize disease-resistance and drought tolerance.
While the performance of the modified push-up method has yet to be validated by scientific testing, we are proud to say that it has the endorsement of numerous superintendents in our region. Each reports that their “new” greens perform and maintain almost identically to their old greens. As an added bonus, most were able to save a bit of money on their material budgets.
Of course, pricing will always vary depending on location, availability of material and the results of testing, which will indicate material depths. Indeed, we’ve got three projects this summer where we’ll be deploying this method and each of them is pricing out a bit differently. Even so, we’re always glad to share data with anyone who’s considering a project or presenting a budget to their decision makers.
Big-picture take-away: I’m not sure any of these alternatives would have been developed in a boom market. I guess we should step back and appreciate the fact that necessity is and always will be the mother of invention.
Bob Lohmann is founder, president, and principal architect of Lohmann Golf Designs and a frequent GCI contributor. Check out his blog at lohmanncompanies.blogspot.com
To learn more…
Looking for a golf course architect, or have you lost touch with your course architect? Enter asgca.org/members into your web browser for a comprehensive list of golf architects working in your region courtesy of the American Society of Golf Course Architects.
Get curated news on YOUR industry.
Enter your email to receive our newsletters.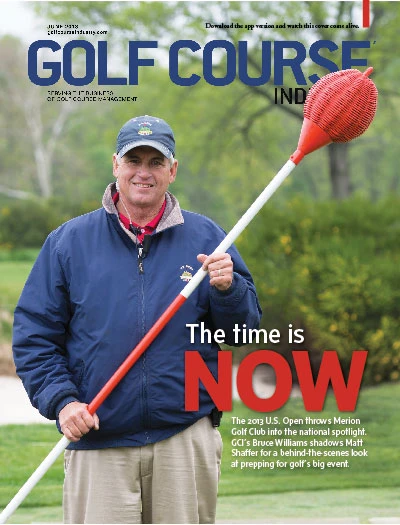
Explore the June 2013 Issue
Check out more from this issue and find your next story to read.
Latest from Golf Course Industry
- Carolinas GCSA raises nearly $300,000 for research
- Advanced Turf Solutions’ Scott Lund expands role
- South Carolina’s Tidewater Golf Club completes renovation project
- SePRO to host webinar on plant growth regulators
- Turfco introduces riding applicator
- From the publisher’s pen: The golf guilt trip
- Bob Farren lands Carolinas GCSA highest honor
- Architect Brian Curley breaks ground on new First Tee venue