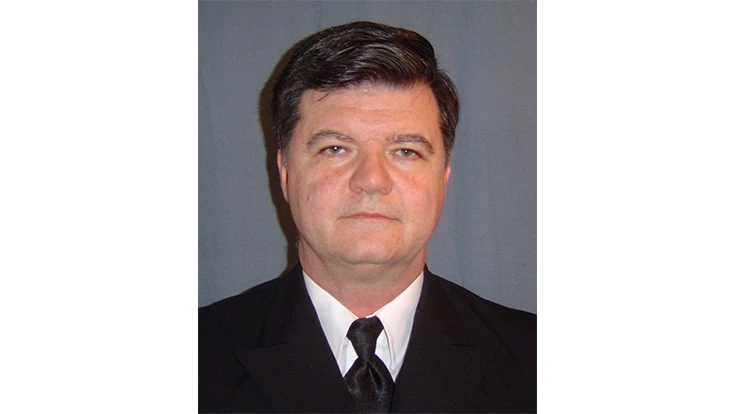
|
The Crown Golf Club is a typical 18-hole course with a practice green and driving range. It’s located in a town with substantial tourist traffic, and is open to members and the public. As equipment manager, I run a small motor pool necessary for a course this size and, being typical, two of each kind of machine. Some of these machines have cutting edges that need to be sharpened regularly to maintain their efficiency. Self-sharpening reelsEleven of the 34 reels I take care of sharpen themselves. The technology has been available for about nine years, but I didn’t get them until about four years ago. The key to their success is the EdgeMax bedknife. The bedknife is set with a light pressure on the reel to continuously sharpen the reel. The bedknife takes off no more metal than I would backlapping and has the advantage of keeping the reel sharp continuously rather than going through the cycle of gradually getting dull until sharpened again. Minor dings in the reel are often cleared up by the bedknife before the machine in the shop. I plan to switch all the reels to the self-sharpening version. Next, I would like someone invent self-adjusting reels that automatically maintain the proper pressure between reel and bedknife. Reels and bedknivesA truly sharp blade has one flat face meeting another flat face at some angle with no rounded edge to reflect light between them; any reflection of light you see on the cutting edge is dullness that needs to be ground away. The older, not self-sharpening reels require frequent backlapping and the bedknives require frequent face grinding to reveal a fresh edge. The backlapping, because of reels’ spiral design, causes the reels to become cone shaped over the course of the season. Spin grinding in the winter returns them to cylinder shape. Relief grinding thins the blades so less material needs to be removed when backlapping to find the new edge. For greens mowers, I test the cut with a single thickness of copier paper. You should hear a clean, crisp cut all along the reel. For other mowers, I use two thicknesses of copier paper. Ideally, it would cut the first and fold the second, but adjusting a reel to do this takes about three times the amount of time as adjusting it for light contact. To save time, most people adjust the bedknives for light contact with the reel. Rotary mower bladesFor the seven-deck Toro GroundsMaster 4700-D with high-lift, aggressive mulching rotary blades, if I wait until the blades are dull, it takes about 15 minutes of grinding per cutting edge to get a properly shaped edge. That is 3½ hours devoted to sharpening one mowers’ blades. The more frequently the blades are sharpened, the less metal you need to take off each time, and the quicker you’re done. The total amount of metal removed in a season is the same; you are just doing it in smaller amounts more frequently. The blade sharpening machine sales people recommend rotary blades be sharpened every eight hours of operation. This mower mows eight hours a day, five days a week, which means I should sharpen it every day. To prevent the mower from being out of service for any long period of time, I keep a second set of blades sharp that can be swapped out in about 15 minutes. Sharpening the dull set of blades can be done while the mower is out. There are pencil sharpener-like automatic machines on the market to sharpen rotary blades; you put in a dull blade and take it out sharpened and balanced. The machines seem to be priced for large contract sharpening companies, not for small maintenance shops like mine. The compromise I have made is to use a 4½-inch DeWalt disk grinder to find the new edge with the blade clamped in a bench vise. Disk grinders are easier to control and faster cutting than the grinding wheel on the shops pedestal grinder. Other edged weaponsOther edged tools need sharpening, too. Sod cutters of various sizes are used for cutting sod. Cup cutters of regulation and novelty sizes need an especially sharp edge. The test is to drop them on the green, and they should stick like yard darts. There are loppers, hedge trimmers, chainsaws, scissors and chisels. In each case, the general goal of making the bright dullness line disappear is the trick. Paul F. Grayson is the Equipment Manager for the Crown Golf Club in Traverse City, Mich., a position he’s held for the past decade. Previously, he spent 8½ years as the equipment manager at Grand Traverse Resort & Spa. Prior to that, he worked as a licensed ships engine officer sailing the Great Lakes and the oceans of the world. |
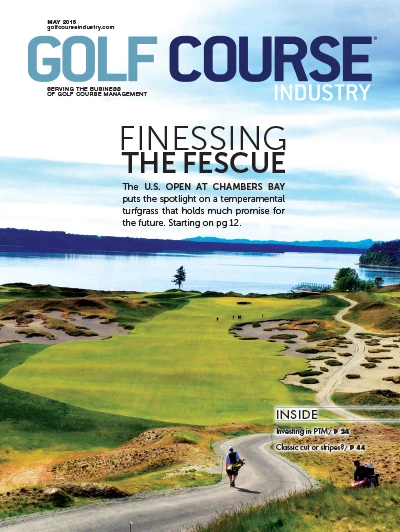
Explore the May 2015 Issue
Check out more from this issue and find your next story to read.
Latest from Golf Course Industry
- Editor’s notebook: Green Start Academy 2024
- USGA focuses on inclusion, sustainability in 2024
- Greens with Envy 65: Carolina on our mind
- Five Iron Golf expands into Minnesota
- Global sports group 54 invests in Turfgrass
- Hawaii's Mauna Kea Golf Course announces reopening
- Georgia GCSA honors superintendent of the year
- Reel Turf Techs: Alex Tessman