Golf course drainage problems are aptly named. They drain superintendents’ budgets and manpower, they drain the patience of golfers forced to leave their carts on the path while they slog through puddles to their ball, and perhaps most critically, they drain the course’s revenues if the course is too wet for play.
While drainage issues, like most golf course maintenance problems, are rarely solved forever with a one-time fix, there are some generally accepted solutions to the most commonly encountered drainage woes.
From the start, superintendents need to correctly identify the cause of their drainage issues. A solution that works for, say, a high-water table may not work for impermeable soil conditions, although the damage to turf caused by resulting poor drainage may look the same at first glance, according to Steve Ami and John Kelly of the Montreal-based Kelly Ami Inc. drainage engineering consulting firm described in a 2004 GreenMaster magazine article entitled “Solving Drainage Problems.” Drilling an auger hole near surface water accumulations, allowing it to fill and then checking to see how the water table level in the hole compares to the level of the accumulated surface water will tell you what you’re dealing with. If it is more than 18 inches below the accumulated surface water or ponding, the problem is impermeable soils rather than a high water table, according to Kelly and Ami.
The four drainage problems addressed by Kelly & Ami are the aforementioned impermeable soils and high water table, depressional areas and side hill seepage. Their nature and solutions are as follow.
Impermeable soils. Characterized by clay-like texture, flat topography and poor water filtration rates which prevent percolation of excess water through the soil layers. The best solution, according to Kelly & Ami, is a slit drainage approach consisting of a 3-inch wide trench, 10 to 22 inches deep, with a drain pipe measuring 1.5 to 2 inches in diameter to channel excess water to a larger collector pipe to carry it off-site.
Depressional areas. Exactly what they sound like – depressed areas where water congregates after a storm. Conventional sub-surface drains often don’t work well because they can’t move sudden accumulations of storm water through the turf, soil and backfill material fast enough to prevent ponding. A better solution is installation of surface inlet drains, making sure they have large enough openings to move the water quickly and are sturdy enough to withstand damage from maintenance equipment and other golf course traffic.
Depressional areas don’t need to be a bad thing. “Instead of trying to fill shallow depressed areas, you can take advantage of those existing low areas by lowering them and installing catch basins,” says Tom West of Victoria, Minn.-based Hartman Companies, a golf course renovation firm.
High water table. One sign is water weeds accumulating in the area, and the auger hole testing will confirm that the water table is too high in the affected areas. The recommended solution is the installation of parallel sub-surface drains. These are deeper, 30 to 48 inches deep, using 4-inch diameter pipes to lower the water table to the desired levels.
Side hill seepage. Problem occurs when impermeable soil is located below relatively permeable soil on a slope, or when holes in the impermeable soil in a slope have been created by machinery. In either case, water pools there and cannot escape vertically, so it goes horizontally and “seeps” out on one side or the other of the slope. The best solution to the problem is installation of 4-inch “interceptor” drains backfilled by very permeable drainage sand and penetrating just into the impermeable soil layer. Interceptor drains should be placed just above or just below the seepage area, and the process may require multiple drains, ensuring that the backfill sand is extremely permeable, or clear stones may be used for the purpose.
Insufficient slope
Both course architect Jeff Brauer and Joel Weinan, a senior designer with the McDonald & Sons golf course design and construction firm, stressed that in most cases, pooling of water in chronically wet areas can be avoided by ensuring that both fairways and greens have a proper amount of “pitch” or slope built in to enlist gravity’s help in moving water off the turf in those areas.
“One thing I see a lot is courses that have laid their [drainage] pipe too flat,” Brauer says. “You have to lay it to a minimum slope to get grass and other materials flowing and not clog up your drains. We call it ‘self-cleaning velocity.’ You can never underestimate the power of water. If you guess a 4- to 6-inch pipe, you probably need a bigger pipe. A lot of people think an 8-inch pipe has double the capacity of a 4-inch pipe, but it actually has four times the capacity. So if you’re worried about cost, remember that the cost goes up linearly, but the capacity goes up by four.”
Nothing beats proper surface grade, Weinan says. “You want to achieve at least 3 percent pitch on fairways and 1.5 percent on greens,” he says. “One mistake I see a lot is courses put pipe in the ground and a pipe inlet basin, but they don’t contour the surface so that water goes into the drain. We call those ‘drive-by’ inlets. And if you get super-saturated fairways, what can happen is that when the sun comes out, it can almost boil the turf.”
Do it in-house or hire a contractor? When a drainage problem occurs these days, one of a superintendent's first thoughts is likely how much it will cost to fix in time, labor and materials. The next concern is whether the repairs will necessitate closing all or parts of the golf course for any length of time. And in many cases, a third consideration will be whether the superintendent and his crew can handle the job in-house or if it will be necessary, or preferable, to bring in a contractor who specializes in that type of work. The determining factors on whether to do it yourself or bring in a hired gun are directly related to the first two of those questions. If the maintenance budget is already accounted for and the owner isn't willing or able to spend the money necessary to hire the job out at the time, it's up to the superintendent to do the best he or she can to at least put a Band-Aid on the wound until a more permanent solution is found. However, if doing the job in-house means closing all or parts of the course for any length of time, and a specialist could do the job in a fraction of the time, this may motivate the owner to come up with the necessary funds. Industry veteran Tommy Sasser, Recreational Community Consultants, Eatonton, Ga., says the decision depends upon the extent and complexity of the drainage project. "To do relatively minor things in-house, such as maybe 100 feet of pipe, that's OK, but if you're doing whole fairways, I think you should always go with an experienced contractor," Sasser says. "A two-week project might take five weeks or more if it's done in-house, and (contractors) are so good now that they can do it while the course is open and not disrupt play. The superintendent should figure out what the cost is to do it in-house, but when he's doing that, he has to also figure out what won't get done in terms of their regular maintenance duties, and what the real cost of doing it in-house is." Samson Bailey, owner of Middleboro, Ky.-based Golf Preservations, agrees that while a contractor's cost may be relatively straightforward, there are other considerations when calculating the cost of doing a drainage project in-house. In addition to a golf course crew's time and wages, there may be equipment rental or purchase costs if the course doesn't have the necessary tools on hand, not to mention potential revenue loss if the course is unplayable. "Many courses don't have enough equipment to do some of those jobs properly and efficiently, so their cost per foot is higher (than a contractor's)," Bailey says. "One superintendent we worked with told me that he started out trying to do the drainage on his greens in-house, but after it took between two and five days each to do two greens, his crew was ready to quit, so he asked us to take over. We came in and did one a day, and he said that's the way he's going to go from now on." Since greens, and to a lesser extent bunkers, draw the most attention from golfers, John Pollok, Southwest agronomist for Ewing Irrigation, says many superintendents want to do drainage projects involving those areas in-house where they can oversee every detail of the work. "When it comes to drainage around greens and bunkers, most of my guys want to keep that work in-house, and I agree with that," Pollok says. "For larger projects, though, it's usually best to bring in a contractor." For superintendents with limited budgets, Sasser suggests a strategy for getting the money necessary to fix all or most of the course drainage issues at once. "Over a period of time, you might want to identify areas that are trouble spots so you can bundle those into one budget item," he says. "That way, you can discuss it up front with the owner or the board of the club rather than springing it on them every time something crops up." In other words, while it may be hard to plan for a 4-inch rainstorm, it is possible to have plans – and drainage – in place in case you get one. |
Standing water in swales
West, Weinan and Brauer all noted that many courses run into problems with soggy areas in swales, which can be caused by either rain or excessive irrigation. All three stated more is usually better in terms of surface drains in swales. Both Weinan and Brauer recommend drains be no farther apart than 150 feet if possible to ensure that water doesn’t accumulate between drains
. Swale drainage should be “feathered out” with a dip at the ends to access a larger drain pipe, the bigger the better, says John Pollok, Southwest agronomist for Ewing irrigation.
Don’t lose your inlets
Many courses, especially those built before the current superintendent was on site, have no idea where their inlet and outlet drains are located around their greens, assuming that they weren’t built with an above-ground station, and most are not.
West suggests courses install a tracer wire with the drain tile and stake tile outlets. Pollok adds superintendents need to know where those inlets and outlets are located so they can find them and flush them with fresh water and air once a month or so to keep them free-flowing. The same problem occurs with bunkers, when inlet drains are buried and require time consuming and expensive effort to check them periodically. Pollok has talked with a number of contractors who tell him the specs for the job called for the inlets to be buried. If that is the case, he strongly recommends the superintendent or contractor create a record on where they are for future reference.
Golf course drainage issues are inevitable from time to time, thanks to Mother Nature, bad course design, the occasional irrigation system malfunction or good old human error. So, as veteran course builder and former Golf Course Builders Association of America President Tommy Sasser says: “The bad thing about it is that they will continue.”
On the other hand, with proper diagnosis of the problem and timely corrections, an individual drainage problem shouldn’t last for long.
Jim Dunlap is an Encinitas, Calif.-based writer and frequent GCI contributor.
Get curated news on YOUR industry.
Enter your email to receive our newsletters.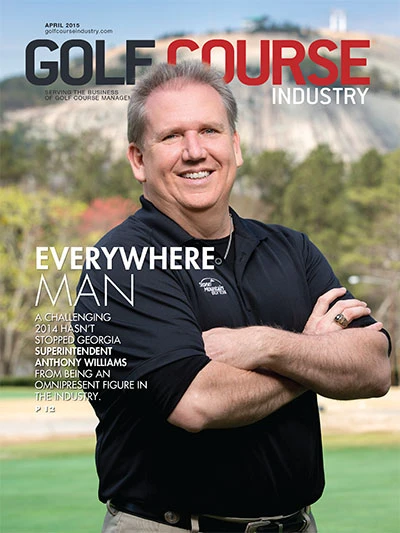
Explore the April 2015 Issue
Check out more from this issue and find your next story to read.
Latest from Golf Course Industry
- Standard Golf announces new product lineup for 2025
- The Salt Pond taps Troon for management
- KemperSports selected to manage Swansea Country Club
- From the publisher’s pen: Grab that guide
- Introducing our April 2025 issue
- South Carolina leaders honor golf course superintendent
- One and only
- Wild can be good