The questions are: soup or salad, paper or plastic, flat or relief? The answers are: salad if you’re on a diet, paper if you’re out to save the planet and for flat or relief – check with your equipment manager. Golf course equipment managers, formerly known as golf course mechanics, all have an opinion on how best to sharpen and maintain reel mowing equipment.
Flat or relief, which is better? I took this question to four equipment managers who work for the City of Aurora, Colorado Golf Division. After my interviews, I categorized their responses as, two relief and two flat. Bob, 29 years of experience, and Greg, 20 years of experience, are in the flat-grind camp. Ben, 15 years of experience, and Jarrett, 31 years of experience, are in the relief-grind camp. All four remember the old manual grinders when they stood for hours moving the stone one pass at a time back and forth over the reel or bedknife. Jarrett says the new automated spin grinding equipment has added 20 years’ longevity to his knees and back. Jarrett, the most senior of the group, also recalls the old sharpening equipment and the “art” of setting it up. He says, back then, to grind reels the equipment was so imprecise the set-up was about 80 percent feel and 20 percent technology. Today, with the new gauges and equipment, he says the set-up is almost 100 percent technology. He can now teach anyone to grind reels and bedknives.
The great debate To subvert the simplicity gained from modern machines to enable technicians to perfect the grinding process efforts confusing the issues rage on. Following, is just a sampling of controversial issues relating to the art of sharpening mowers:
|
When it comes to grinding, Ben uses a 35-degree relief grind on reels and an 8-degree relief grind on his bedknives. Jarrett says a relief grind at about 20 degrees on reels and 4 to 5 degrees on bedknives is his preference. Jarrett says his new Foley Grinder can put a flat or relief grind on reels. When he sharpens his units in the winter, he grinds the reels flat, and then puts on a relief grind. Jarrett likes the way his reels mow and says it is easier for him to keep the reels in adjustment with a relief grind.
Mowers, once sharpened, also have to be maintained. Jarrett still back-laps greens mower reels the old-fashioned way. That is, with the reels still attached to the mower on the floor spinning backwards. He also touches up greens mower reels on the spin grinder depending on what the issues are. The other three equipment managers feel their days of brushing back-lapping compound on the reels as they spin backwards are gone forever. Ben says back-lapping the old way was a way to true the reel to the bedknife. If the bedknife was out of shape, the reel became even more out of shape. Eventually, the mower would have to be broken down and the reel and bedknife would have to be re-ground. In maintaining his cutting units Ben feels the bedknife is key. With an 11-blade greens mower reel, the bedknife has metal to metal contact 11 times more often than a reel blade. Ben is always checking his bedknives and touching them up with a hand file to ensure the bedknife stays sharp.
But back to the question: flat or relief? Jarrett is of the opinion with a relief grind there is less friction because when the mower is cutting turf as there is less metal to metal contact. This reduction in friction decreases drag on the engine and mower hydraulics. Less drag means a longer mower life and a more efficient engine, which can be particularly important for high-altitude courses in Colorado. Jarrett also asks those on the flat grind side of the ledger, if flat grinding is preferable, why do new mower reels always come with a relief grind?
Greg and Bob believe the flat grind is the preferred method and use the Express Duel Anglemaster grinder. The Express Dual is considered a flat grind system. The manufacturer calls it a hammer grind. The stone and carrier actually move on contact with the reel blade and provide approximately 4-5 degrees of relief. With his automotive background Greg says it seems strange to see the spin grinder in action as the reel tends to vibrate as it goes over the grinding stone. But he says it works. Back before the days of spin grinders Bob would use the old relief-type grinders and get as close to a flat grind as possible. He feels a reel with a flat grind will stay sharp longer and will last longer. He says with the new grinding systems, rather than back-lapping he will replace the bedknife on greens mowers and touch up the reel about once per month. Bob’s other cutting units are sharpened during the winter and on an as-needed basis during the season.
Flat or relief, which is better? That decision is best left to the expert on staff responsible for ensuring the mowers are sharp and ready to mow each day. As for quality assurance, one of the things Ben likes best about his job is grabbing a cup of coffee in the mornings and driving the course to check his mowers. “In addition to the course being beautiful that time of day, it is very satisfying to see well-groomed turf with tiny, precisely cut blades of grass coming off the mowers,” says Ben.
Dennis Lyon, CGCS, is a former GCSAA president, managed the city of Aurora, Colo., golf program for 37 years and is a GCI columnist and frequent contributor.
What Was & What Is Superintendents should have a cursory knowledge of reel grinding and sharpening, including how it was done in the past.
Backlapping was the final stage of this process and often needed to be conducted for an hour or more to mate the reel with the bedknife. In the 1970s, manufacturers of grinders with names like Neary, Foley and Atterton & Ellis raced to the industry with the spin grinder. Now a novice turf technician could produce a great grind in less time and be certain that the reel was close to a true cylinder. During the rapid expansion of the golf industry of the late 1980s and 1990s turf mangers were lowered the height of cut on turfgrass areas in response to better turf varieties and better overall turf management. Superintendents and turf technicians were challenged to repair, maintain and keep sharp a new generation of turf equipment that delivered much lower and better quality of cut. Greens that were maintained at a height of cut of .316 inch in the 1970s were now maintained at .18 inch.
Today’s reel sharpener manufacturers responded with advances in technology, making it possible to return a reel to original equipment manufacturers (OEM) specifications with the “touch of a button.” Even though these high-tech machines that sharpen reels and bedknives are much less reliant on touch, the superintendent and equipment technician must have a thorough understanding of how the relationship between reel and bedknife work to keep turf healthy and maintained at desirable heights of cut. Michael D. Vogt, CGCS, CGIA, is a consultant with the McMahon Group and a frequent contributor to GCI. |
Get curated news on YOUR industry.
Enter your email to receive our newsletters.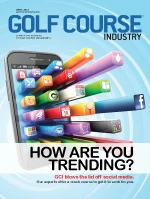
Explore the April 2012 Issue
Check out more from this issue and find your next story to read.
Latest from Golf Course Industry
- SePRO to host webinar on plant growth regulators
- Turfco introduces riding applicator
- From the publisher’s pen: The golf guilt trip
- Bob Farren lands Carolinas GCSA highest honor
- Architect Brian Curley breaks ground on new First Tee venue
- Turfco unveils new fairway topdresser and material handler
- Ignite Attachments adds new box plane and grapple
- Mackenzie & Ebert working on new Caribbean course