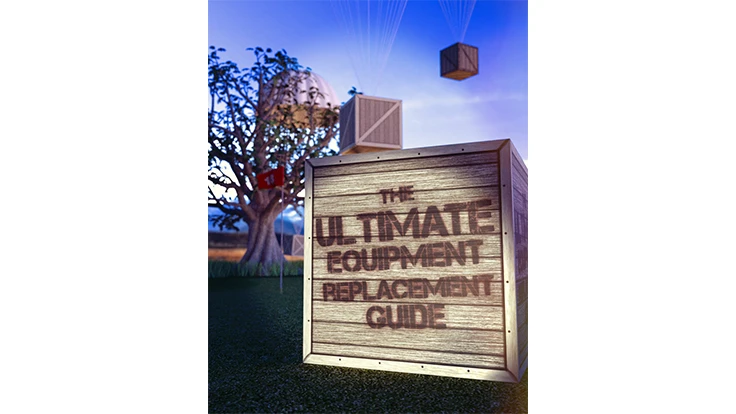
Golf course superintendents should be proactive in providing a complete maintenance equipment inventory, five-year equipment replacement program – updated annually – and a comprehensive preventative equipment maintenance program.
As a result, long-term cash-flow projections to course and club officials for equipment replacement can be made accurately regardless of whether the equipment is purchased or leased. With thorough documentation procedures in place, a superintendent can accurately determine if each piece of equipment costs too much for repairs or if it’s best to replaced. These programs are worthwhile so that capital and leased operating cost funding is available annually to replace worn-out equipment and to acquire new technology on a regular basis.
In addition, a comprehensive equipment-replacement chart is a helpful guide for projecting when to replace equipment.
Maintenance equipment inventory
Efficient, routine maintenance equipment inventories, updated annually, include extensive line items such as: date of purchase; equipment description; where it will be used; original prices and sales taxes; replacement costs; model number; serial number; model and serial number of all attachments such as engine, transmission, cutting units and verticut reels; original expected life; current expected life; when the warranty expires; equipment shop number; and depreciation (if purchased).
The original expected life and current life expectancy should be updated annually, showing where some equipment may last longer than projected, or that equipment may not last nearly as long as originally projected. Also, the trend to lease equipment that normally does not last as long, such as all mowers, turf vehicles, and bunker rakes, and purchasing longer-lasting equipment, such as tractors, loader/backhoes, dump trucks, and trenchers, has gained in popularity.
![]() |
There should be two pieces of motorized equipment, minimum, for each specific area that is being maintained. The equipment includes rough mowers, intermediate rough mowers, fairway mowers, riding bunker rakes and sprayers. This provides one backup piece while servicing and repairs are being done. This helps improve productivity and to get jobs done ahead of golfers. The two motorized equipment minimum rule is also useful in case there are breakdowns during tournaments.
Instead of trading in or selling equipment that normally would be replaced, superintendents will keep, depending on local conditions, the old equipment for other tasks. Old mowing equipment can be used after topdressing greens, collars, tees, fairways and approaches. Likewise, greens mowers can be used to mow tees, collars and approaches.
Five-year equipment replacement program
This program should be updated annually so capital and leasing forecasting and budgeting are thorough and complete.
There are two basic golf industry standards for equipment replacement: to allocate 10 to 15 percent minimum of the total replacement equipment inventory value each year, or approximately 15 or 25 percent of the annual maintenance operating budget. Leasing is more popular with facilities that require their frequently used equipment to be replaced more often, such as walk-behind and riding reel and rotary mowers for all of the maintained areas, turf vehicles, riding bunker rakes and sprayers. When the lease expires, the course has the option of turning the equipment in and acquiring new equipment, or with a one-dollar buyout where the course owns the equipment. The former is more popular because it makes the most sense to keep replacing equipment when it’s worn out and not cost effective to keep repairing it.
There is also an added side benefit to replacing leased or capital equipment, where more modern, state-of-the-art equipment technology is acquired. This replacement program also allows for additional new technology equipment to be acquired that is not being replaced – but added to the inventory so that additional improved agronomic and playing conditioning standards are achieved as dictated by golfer demands.
Leased equipment typically has a separate line item on the maintenance operating budget. And when this occurs, the total operating budget amount can be very deceiving, as it usually appears that this budget is much higher than normal because lease payments are included. Purchased equipment is placed on a separate capital expense budget.
The purchasing of longer-lasting equipment, such as tractors, loader/backhoes, skid-steer loaders and attachments, dump trucks, dump trailers, fairway aerifiers, and fairway topdressers with material handling systems, is more the rule than the exception for courses nationwide. The life expectancy on this equipment is usually longer, which makes purchasing more cost effective. An added side benefit is it is usually depreciated on the course’s financial statements because it is a capital expense.
Terry’s tips
|
Preventative maintenance, repairs and equipment modification
A solid equipment manager is paramount to not only keep maintenance equipment up and running, but for it to meet its life expectancy.
Maintenance equipment gets more sophisticated each year, with more and more diesel, hybrid and electric variants designed and built by multiple domestic and international manufacturers. The total amount of equipment in the inventory has rapidly expanded over recent years, mostly because of player demands for better conditioning standards. Because of the sophistication and larger amounts of equipment, many 18-hole courses employ two equipment technicians: the equipment manager, who performs repairs, sharpening and equipment modifications; and an assistant mechanic/technician, who performs routine preventative maintenance programs and lapping/sharpening. Only one equipment manager for 18 holes, in most cases, is too much work for an individual.
Maintenance equipment replacement chart
The chart on page 18 has a complete listing of everything an 18-hole golf course and practice areas require to be maintained. Since the equipment usage differs noticeably in different areas of the country, the chart highlights the three climatic zones: the cool-season, transition zone and warm-season climates. The range in years for each climatic zone is a good estimate and projection for when equipment typically should be replaced, especially before it becomes too costly to continue to repair. How long equipment will last is based on frequency of use, climatic conditions, employee’s care when operating the equipment, preventative maintenance programs, whether it’s stored inside or outside in the damaging sunlight and moisture, operating budget equipment maintenance line items, etc.
This chart is based on years when the equipment should normally be replaced instead of hour meter readings, because all maintenance equipment does not normally come equipped with them. Typically one hour equals about 60 miles on average on an automobile, meaning 3,000 hours equals approximately 180,000 auto miles equivalent. Newer equipment models are being installed with hour meters, especially on engines that do not have electric starters.
Typically motorized equipment costs more to maintain between the second and third year of the acquisition – or typically between 3,000-4,000 hours (180,000-240,000 miles equivalent). Monitoring the annual equipment repairs and maintenance costs for each piece of equipment provides insight on when it is more cost effective to replace instead of repair.
Photo/video journal
One final note: To be complete in keeping good, up-to-date efficient records, superintendents must take individual photographs/videos of each respective piece of maintenance equipment as proof that it was in inventory during an insurance company loss. Duplicate digital copies of each photo/video should be kept on a flash drive or CD Rom disc and stored in a safe place, such as in a fireproof file cabinet or even off site.
Terry Buchen, CGCS, MG, is president of Golf Agronomy International and regular GCI columnist.
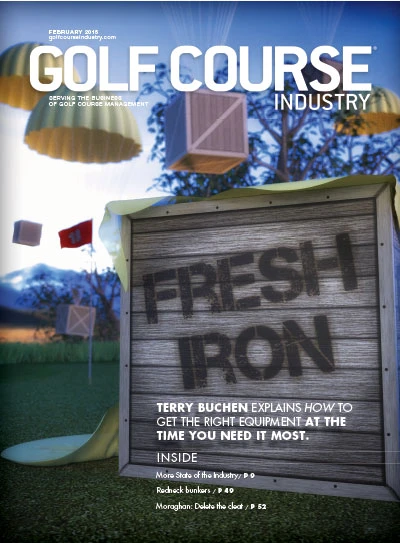
Explore the February 2015 Issue
Check out more from this issue and find your next story to read.
Latest from Golf Course Industry
- Heritage Golf Group expands into Tennessee
- Making the grade — at or near grade
- PBI-Gordon receives local business honor
- Florida's Windsor takes environmental step
- GCSAA names Grassroots Ambassador Leadership Award winners
- Turf & Soil Diagnostics promotes Duane Otto to president
- Reel Turf Techs: Ben Herberger
- Brian Costello elected ASGCA president