Many wise superintendents have said to me over the years that a good mechanic is worth his weight in gold. Jay Rehr prefers to think he’s worth his weight in iron.
Rehr is perhaps the best-known turf equipment mechanic and shop management expert in the world. He’s worked nearly two-dozen majors – including 16 Masters during his long tenure at Augusta National Golf Club – and is currently helping Merion Golf Club prep for the 2013 US Open. More importantly, in the often isolated sphere of turf technicians, he’s reached out to share his insights about life in the world of grease and grinders with thousands of colleagues through consulting and seminars.
The big-league mechanic was born and raised in the Little League city, Williamsport, Pa. High school classes bored him. He was more interested in cars so Rehr enlisted in the Marine Corps and spent 10 years fixing everything the jarheads needed fixed. Curiously, that sometimes included tanks and APCs, but it also occasionally included mowers and turf equipment used on local base golf courses. Rehr liked the precise, weird nature of the high-tech mowers and stuck with it after his retirement from the Corps (remember, there is no such thing as an ex-Marine) and eventually ended back up north working for a distributor, Mid-Atlantic Turf Equipment Co. in 1986.
After a year back in Pennsylvania, he headed back to his old military stomping grounds in Albany, Ga., and continued to work informally on equipment at the local base’s course. That’s when a phone call out of the blue changed his life. "Paul Latshaw was looking for a new mechanic at Augusta and he knew the people at Mid-Atlantic," Rehr recalls. "He called them and they said, ‘Hey, there’s a guy right down there in Georgia you might want to talk to.’ Paul called, introduced himself and made me an offer I couldn’t refuse!"
Rehr was at Augusta from 1988 to 2004, mostly as head mechanic. "I’d worked around golf courses for years, but until I got there I had no idea what was involved with a facility and a tournament of that magnitude," says Rehr. "You can’t understand what it’s like by just volunteering for a week or so. You have to work the whole cycle a few times to really get it."
After years of people telling him how valuable his experience could be to others with shop challenges, Rehr gulped hard in 2004 and went out on his own as a consultant. For several years, he traveled the nation spending days at a time analyzing shop operations at facilities and suggesting changes to improve efficiency, quality and logistics. Then, in 2006, Matt Shaffer from Merion called and asked for Rehr’s help. The two had become friends during Shaffer’s time as an August assistant and, with the Open approaching, Merion needed some intensive care to get its shop operations to top-level standards. "It wasn’t an easy decision but Matt’s a friend and he said he needed help. So I helped."
Now Rehr has nearly finished his task at Merion. He has designed and set up a new shop and trained a new equipment manager and he is pondering what to do next. The only thing for sure is it will involve big-league golf courses and lots of grease.
What have you been doing for Matt this past year or so?
Some of the changes have been big, like completely redoing the shop, but I’m very into proactive maintenance so we’ve spent a lot of time rebuilding equipment, doing bearings, belts, grinding, stuff like that. We’ve built a system where we’re way more proactive about lapping and grinding before someone notices it needs it.
We’ve also done a lot of in-house fabrication. The coolest thing was that we built a very neat fairway roller. It took a couple of tries but we eventually got it right. It’s built on a five-gang frame, but we created custom rollers out of five-inch pieces of solid steel. We used a system of weights to add or subtract weight and balance it out so it rolls evenly over the whole span. Matt wants the fairways to be as true as possible, almost like greens. One of the biggest challenges was figuring out the overall weight so it could be transported behind a tractor. That took a lot of head-scratching and math based on the capabilities of the tractor and the design of the roller, but we got it done.
How does the life of the chief mechanic change as a major approaches?
It’s all about getting the schedule right and working around mowing. The rule of thumb I use is based on a 2.5-hour mowing plan. Essentially, we assume it’ll be 2.5 hours from the time (the mower) rolls until the time it comes back in. Most good superintendents use that time frame. From there, I can figure out how much extra equipment I’m going to need. If I need six units normally, now I’ll need 12. The time schedule dictates everything. From there, I work with the superintendent to figure out the overall schedule, mowing teams and everything else.
The other thing is that you can always find volunteers for events, but you really need good-quality, experienced people for majors. I have a core group of people I trust who I know can handle anything that comes down the pike. We really worked well together during the Walker Cup a few years ago and I have no reason not to think it won’t be just as good for the Open.
The last big thing is deciding when I’m going to put my last grind and bedknives and reels, do final oil changes and lubes, etc., beforehand. At some point you have to gamble and stop greasing so you’re sure that you won’t have any leaks or other problems for the event.
What were the biggest lessons you learned at Augusta?
One important thing you learn there is that there actually is a budget. (Laughs.) It’s not small, but there’s a budget. You still have to make the most of what you can with the money and resources available.
One other little thing that was very cool there was helping to develop the "wacky mower." It’s a unit that set to cut at ¾" on one side and 5/16" on the other. The head is at an angle but the reels are true. The idea is to cut so the ball keeps rolling evenly over the transition line rather than dropping and bouncing. It’s a very cool little innovation.
It was also neat to watch my friends (notably Marsh Benson) there perfect the SubAir. That thing has really been a game-changer all over the country.
Finally, yes we did have a ton of equipment there to help us produce those conditions (for the tournament). Anyone who had the latest and greatest widget would send it to us because we had the best mechanics and they wanted us to check it out and evaluate it. But the big thing that most people don’t understand is that even though we moved heaven and earth to make sure things were perfect for Masters week, what you see on TV is pretty much the conditions the members there see every day.
Tell us about your consulting business.
Several really knowledgeable people told me to do it and I found out there were lots of guys who needed a little or even a lot of help. Typically, a superintendent feels like his shop isn’t quite where it should be and one of his buddies will suggest he bring me in. I come in and work side-by-side with the mechanic at your course for three days. We evaluate reel settings, cutting heights, parking, flow in and out of the facility, lifts, organization – everything! The objective is to take an average mechanic with an average shop and make him a tournament-quality mechanic with a great shop. It’s just like I was saying about Augusta, you want to treat the course like it’s a tournament all season long and you have to have world-class shop support to do that. And a better course means happier members.
What were some of the really interesting or innovative things you saw at shops around the nation?
You pick up little things. One guy put in a little ramp from the lift table to the grinder. Flip the ramp down and move it over in one step. It’s small, but it saves a few minutes each time you grind, but that eventually adds up to a day or two over the course of year. A good mechanic can do a hell of a lot with an extra day or two per year. If you look around your facility enough, you can usually find a lot of those little time-savers. It can make a huge difference in the long run.
I saw a ton of operator-ease modifications – too many cool ones to list. Hey, we’re all tinkerers but when you’re a tinkerer who really listens to the operators, you can come up with all sorts of neat ways to help them out and improve their performance.
I also found a lot of amazing fabrication stuff. Almost everyone had built some sort of customized transport carts that work for them at their course but wouldn’t work at the place up the street. I’ve also seen lots of cool winches and stands. A good mechanic will eventually piece together anything that makes life easier.
What were some things that made you cringe?
I’m always shocked at how many people don’t take mowing accuracy as seriously as they should. By now, every mechanic out there should have an Accu-Gauge, but there’s still guys using HOC cards or even timecards! That’s just dumb. But, you have to be patient and work with them to explain that even though it might be a fairway unit, it can and should cut like a greens unit with just a little extra care.
Obviously, there are also still some places that just don’t have a mechanic and the superintendent or the assistant simply just don’t have the time to actually put their hands on the unit every day. In my view, if it goes out every day, you need to have your hands on it every day and make sure it’s working exactly like it’s designed to.
What’s the most common mistake superintendents make in their relationship with or management of technicians?
Unfortunately, there are still superintendents who like to tell the mechanic how to do things. It tends to happen mostly with veteran guys who were very hands-on coming up through the ranks. Instead of looking over the tech’s shoulder and dictating every little thing, it should be "tell me what you want and leave me alone." If I don’t know how to do it, I’ll find out how to do it. You go do your job and I’ll do mine. Want to drive a mechanic crazy? Come into his shop and tell him what to do.
Newer mechanics can definitely get overwhelmed. There’s too much equipment, it’s all different and a lot of it is extremely sophisticated these day. Even older mechanics have this problem when they get new stuff after running essentially the same units for 20 years. Now he’s gotta figure stuff out and sometimes it’s just trial and error. The superintendent has to be patient. Hey, we’re all egotistical and we never want to admit that we don’t have a clue, but there are times we don’t and we simply have to slowly go through the steps and figure out the problem on our own. I’d rather be wrong on the safe side than do damage out on the course.
There have been many efforts to organize and promote golf course technicians. Have they begun to make a difference?
It’s starting to work. Look at GCSAA way back when. They had to evolve from being greenkeepers who made no money to where they are today. We used to just be grease monkeys and now were called technicians, so we’ve begun that same evolution. In the end, it’ll be just like the superintendent – better recognition, better conditions, better compensation. It takes time but it will happen. It improves things for everybody, even old farts like me.
The Internet has revolutionized everything. It’s so much easier now to find help with a problem than it used to be. You can contact manufacturers in seconds or put out a post on one of the technical forums. You may not necessarily like all the responses you get, but usually you’ll find someone who really has the solution and you can take what works and use it.
What are the basic things every course can do to improve its shop operations?
Well, golf courses are like snowflakes – they’re all different. So I don’t want to generalize too much. But there are a few simple things. First, every course should have a lift, lift table and Accu-Gauge. Those are just givens but it’s surprising how many guys are still improvising.
The other necessity for me is a separate grinding room to keep the place cleaner. I realize there are a lot of guys are in old shops or even barns. It’s like being in a bunker when you’re in a shop with no windows or air movement. It’s a real problem.
Which technologies have most dramatically changed the world of equipment maintenance?
It sounds silly, but the top of my list was the first lift that was actually made for golf course equipment. How wonderful was that! I’m harping on this, but the Accu-Gauge really was a big deal. It finally allowed you to dial things in better.
Finally, I’d say the introduction of MIG welders and plasma cutters pretty much opened the door for really good fabrication. That stuff didn’t exist when I was learning. We had a nasty old stick welder and cutting torches. It was like going from a horse-drawn cart to a Ferrari when the better fabrication tools came along.
What’s your advice for folks considering this as a career?
Here are the reasons to do it. You can work anywhere in the U.S. or the world, for that matter. Golf may be down a little but it survives. It’s always going to be here. Once you get to a certain level, traveling is nice and you get to check out different places. Best of all, you have a job where you get to play with cool equipment but you also get to regularly be outside. That’s great.
The flip side is that you can definitely hurt yourself. We work with very sharp things. There are a lot of guys missing fingers or at least parts of fingers. The bad part of the getting to work outside thing is that sometimes you’re out their in the rain or the mud. You just have to do it sometimes. Finally, you have to get along with the boss or you’re gone.
Final thoughts?
My life and my career are intertwined. I love what I do but my greatest joys are my wife, my son and my grandchildren. I’ve got friends around the world because of what I do, and not many people can say that.
I’m pretty proud of what I’ve done so far and I’m looking forward to the next stage of my career. I don’t know exactly what the future will hold, but I know that it will be interesting, challenging and fun. How cool is that? GCI
Jay Rehr can be reached at 706-840-0929 or equiptec@meriongolfclub.org.
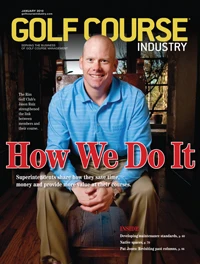
Explore the January 2010 Issue
Check out more from this issue and find your next story to read.
Latest from Golf Course Industry
- GCSAA’s Health in Action 5K/2K reaches fundraising goal
- Landscapes Golf Management to participate in data analyzation initiative
- Reel Turf Techs: Carl Michael
- Atlanta Athletic Club approves funding for master plan
- Maximizing Cultural Practices and Agronomic Benefits with Minimal Surface Disruption
- Real Answers about Spray Nozzle Choices
- From the Course to the Factory: How Customer Insights Drive Innovation
- New & Proven Enzyme Strategies for Sprayable Thatch Management